Sterling performance
Page 106
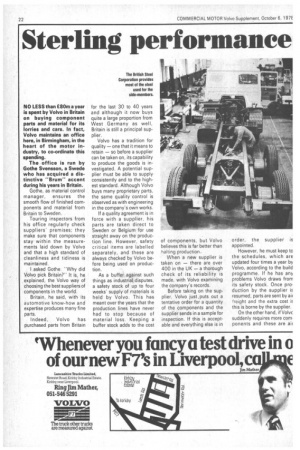
If you've noticed an error in this article please click here to report it so we can fix it.
NO LESS than £80m a year is spent by Volvo in Britain on buying component parts and material for its lorries and cars. In fact, Volvo maintains an office here, in Birmingham, in the heart of the motor industry, to co-ordinate this spending.
The office is run by Gothe Svensson, a Swede who has acquired a distinctive "Brum" accent during his years in Britain.
Gothe, as material control manager, ensures the smooth flow of finished components and material from Britain to Sweden.
Touring inspectors from his office regularly check suppliers premises; they make sure that components stay within the measurements laid down by Volvo and that a high standard of cleanliness and tidiness is maintained.
I asked Gothe -Why did Volvo pick Britain?'' It is, he explained, the Volvo way of choosing the best suppliers of components in the world.
Britain, he said, with its automotive know-how and expertise produces many fine parts.
Indeed, Volvo has purchased parts from Britain for the last 30 to 40 years and although it now buys quite a large proportion from West Germany as well, Britain is still a principal supplier.
Volvo has a tradition for quality — one that it means to retain — so before a supplier can be taken on, its capability to produce the goods is investigated. A potential supplier must be able to supply• consistently and to the highest standard. Although Volvo buys many proprietary parts, the same quality control is observed as with engineering in the company's own works.
If a quality agreement is in force with a supplier, his parts are taken direct to Sweden or Belgium for use straight away on the production line. However, safety critical items are labelled separately, and these are always checked by Volvo before being used on production.
As a buffer against such things as industrial disputes, a safety stock of up to four weeks' supply of materials is held by Volvo. This has meant over the years that the production lines have never had to stop because of material loss. Keeping a buffer stock adds to the cost of components, but Volvo believes this is far better than halting production.
When a new supplier is taken on — there are over 400 in the UK — a thorough check of its reliability is made, with Volvo examining the company's records.
Before taking on the supplier. Volvo just .puts out a tentative order for a quantity of the components and the supplier sends in a sample for inspection. ff this is acceptable and everything else is in order, the supplier is appointed.
However, he must keep tc the schedules, which are updated four times a year by Volvo, according to the build programme. If he has any problems Volvo draws from its safety stock. Once production by the supplier lE resumed, parts are sent by au freight and the extra cost k this is borne by the supplier.
On the other hand, if Volvc suddenly requires more cornponents and these are aui