Rigid basis to
Page 102
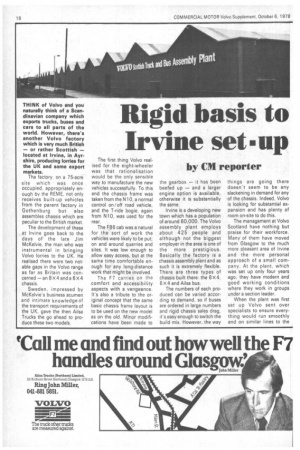
Page 103
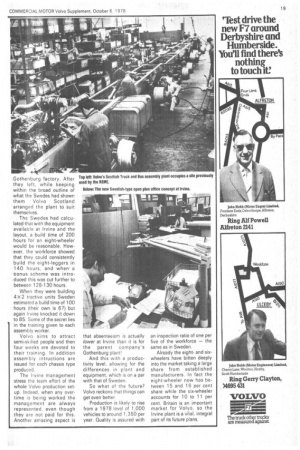
If you've noticed an error in this article please click here to report it so we can fix it.
Irvine set-up
by CM reporter
THINK of Volvo and you naturally think of a Scandinavian company which exports trucks, buses and cars to all parts of the world. However, there's another Volvo factory which is very much British — or rather Scottish — located at Irvine, in Ayrshire, producing lorries for the UK and some export markets.
The factory, on a 75-acre site which • was once occupied, appropriately enough by the REME. not only receives built-up vehicles from the parent factory in Gothenburg but also assembles chassis which are peculiar to the British market.
The development of these at Irvine goes back to the days of' the late Jim McKelvie, the man who was instrumental in bringing Volvo lorries to the UK. He realised there were two notable gaps in the Volvo range as far as Britain was concerned — an 8 x 4 and a 6 x 4 chassis.
Sweden, impressed by McKelvie's business acumen and intimate knowledge of the transport requirements of the UK, gave the then Ailsa Trucks the go ahead to produce these two models. The first thing Volvo realised for the eight-wheeler was that rationalisation would be the only sensJble way to manufacture the new vehicles successfully. To this end the chassis frame was taken from the N10, a normal control on/off road vehicle, and the T-ride bogie, again from N 10, was used for the rear.
The F86 cab was a natural for the sort of work the vehicles were likely to be put; on and around quarries and sites. It was low enough to allow easy access, but at the same time comfortable enough for any long-distance work that might be involved.
The F7 carries on the comfort and accessibility aspects with a vengeance. It's also a tribute to the original concept that the same basic chassis frame layout is to be used on the new model as on the old. Minor modifications have been made to the gearbox — it has been beefed up — and a larger engine option is available, otherwise it is substantially the same.
Irvine is a developing new town which has a population of around 60,000. The Volvo assembly plant employs about 425 people and although not the biggest employer in the area is one of the more prestigious. Basically the factory is a chassis assembly plant and as such it is extremely flexible. There are three types of chassis built there. the 8 x4, 6 X 4 and Ailsa bus.
The numbers of each produced can be varied according to demand, so if buses are ordered in large numbers and rigid chassis sales drag, it's easy enough to switch the build mix. However, the way things are going there doesn't seem to be any slackening in demand for any of the chassis. Indeed, Volvo is looking for substantial expansion and has plenty of room on-site to do this.
The management at Volvo Scotland have nothing but praise for their workforce. Many of them have moved from Glasgow to the much more pleasant area of Irvine and the more personal approach of a small company. At the plant, which was set up only four years ago, they have modern and good working conditions where they work in groups under a section leader.
When the plant was first set up Volvo sent over specialists to ensure everything would run smoothly and on similar lines to the .Gothenburg factory. After they left, while keeping within the broad outline of what the Swedes had shown them Volvo Scotland arranged the plant to suit themselves.
The Swedes had calculated that with the equipment available at Irvine and the layout, a build time of 200 hours for an eight-wheeler would be reasonable. However, the workforce showed that they could consistently build the eight-leggers in 140 hours, and when' a bonus scheme was introduced this was cut further to between 1 28-1 30 hours.
When they were building 4 X 2 tractive units Sweden estimated a build time of 100 hours (their own is 67) but again Irvine knocked it down to 85. Some of the secret lies
• in the training given to each
assembly worker.
Volvo aims to attract semi-skilled people and then four weeks are devoted to their training. In addition assembly Intructions are issued for each chassis type produced.
The Irvine management stress the team effort of the whole Volvo production setup. Indeed, when any overtime is being worked the management are always represented, even though they are not paid for this. Another amazing aspect is that absenteeism is actually lower at Irvine than it is for the parent company's Gothenburg plant!
And this with a productivity level, allowing for the differences in plant and equipment, which is on a par with that of Sweden.
So what of the future? Volvo reckons that things can get even better.
Production is likely to rise from a 1978 level of 1,000 vehicles to around 1,350 per year. Quality is assured with an inspection ratio of one per five of the workforce — the same as in Sweden.
Already the eightand sixwheelers .have bitten deeply into the market taking a large share from established manufacturers. In fact the eight-wheeler now has between 15 and 16 per cent share while the six-wheeler accounts for 10 to 11 per cent. Britain is an important market for Volvo, so the Irvine plant is a vital, integral part of its future plans.