DISTRIBUTION H
Page 40
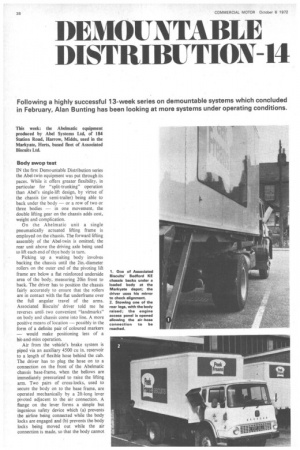
Page 41
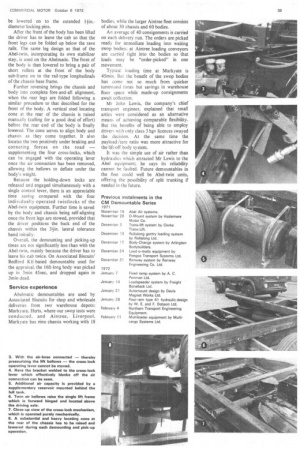
If you've noticed an error in this article please click here to report it so we can fix it.
This week: the Abelmatic equipment produced by Abel Systems Ltd, of 184 Station Road, Harrow, Middx, used in the Markyate, Herts, based fleet of Associated Biscuits Ltd.
Body swop test
IN the first Demountable Distribution series the Abel-twin equipment was put through its paces. While it offers greater flexibility, in particular for –split-trunking" operation than Abel's single-lift design, by virtue of the chassis (or semi-trailer) being able to back under the body — or a row of two or three bodies — in one movement, the double lifting gear on the chassis adds cost, weight and complication.
On the Abelmatic unit a single pneumatically actuated lifting frame is employed on the chassis. The forward lifting assembly of the Abel-twin is omitted, the rear unit above the driving axle being used to lift each end of thye body in turn.
Picking up a waiting body involves backing the chassis until the 2in.-diameter rollers on the outer end of the pivoting lift frame are below a flat reinforced underside area of the body, measuring 20in front to back. The driver has to position the chassis fairly accurately to ensure that the rollers are in contact with the flat underframe over the full angular travel of the arms. Associated Biscuits' driver told me he reverses untiltwo convenient "landmarks" on body and chassis come into line. A more positive means of location — possibly in the form of a definite pair of coloured markers — would make positioning less of a hit-and-miss operation.
Air from the vehicle's brake system is piped via an auxiliary 4500 cu in. reservoir to a length of flexible hose behind the cab. The driver has to plug the hose on to a connection on the front of the Abelmatic chassis base-frame, when the bellows are immediately pressurized to raise the lifting arm. Two pairs of cross-locks, used to secure the body on to the base frame, are operated mechanically by a 2ft-long lever pivoted adjacent to the air connection. A flange on the lever forms a simple but ingenious safety device which (a) prevents the airline being connected while the body locks are engaged and (b) prevents the body locks being moved out while the air connection is made, so that the body cannot
be lowered on to the extended diameter locking pins.
After the front of the body has been lifted the driver has to leave the cab so that the front legs can be folded up below the rave rails. The same leg design as that of the Abel-twin, incorporating its own stabilizer stay, is used on the Abelmatic. The front of the body is then lowered to bring a pair of short rollers at the front of the body sub-frame on to the rail-type longitudinals of the chassis base frame.
Further reversing brings the chassis and body into complete fore-and-aft alignment, when the rear legs are folded following a similar procedure to that described for the front of the body. A vertical steel locating cone at the rear of the chassis is raised manually (calling for a good deal of effort) before the rear end of the body is finally lowered. The cone serves to align body and chassis as they come together. It also locates the two positively under braking and cornering forces on the road — supplementing the four cross-locks, which can he engaged with the operating lever once the air connection has been removed, allowing the bellows to deflate under the body's weight.
Because the holding-down locks are released and engaged simultaneously with a single control lever, there is an appreciable time saving compared with the four individually-operated twistlocks of the Abel-twin equipment. Further time is saved by the body and chassis being self-aligning once the front legs are stowed, provided that the driver positions the back end of the chassis within the 3-1-in. lateral tolerance band initially.
Overall, the demounting and picking-up times are not significantly less than with the Abel-twin, mainly because the driver has to leave his cab twice. On Associated Biscuits' Bedford K h-based demountable used for the appraisal, the 16ft-long body was picked up in 3min 45 see, and dropped again in 3min dead.
Service experience Abelmatic demountables are used by Associated Biscuits for shop and wholesale deliveries from two warehouse depots: Markyate, Hefts, where our swop tests were conducted, and Aintree, Liverpool. Markyate has nine chassis working with 18 bodies, while the larger Aintree fleet consists of about 30 chassis and 60 bodies.
An average of 40 consignments is carried on each delivery run. The orders are picked ready for immediate loading into waiting swop bodies; at Aintree loading conveyors are carried right into the bodies so that loads may be "order-picked" in one movement.
Typical loading time at Markyate is 45min. But the benefit of the swop bodies has come not so much from quicker turnround limes but savings in warehouse floor space while made-up consignments await collection.
Mr John Lewis, the company's chief transport engineer, explained that small artics were considered as an alternative means of achieving comparable flexibility. But the benefits of being able to employ drivers with only class 3 hgv licences swayed the decision. At the same time the payload/tare ratio was more attractive for the lift-off body system.
It was the simple use of air rather than hydraulics which attracted Mr Lewis to the Abel equipment; he says its reliability cannot he faulted. Future demountables in the fleet could well be Abel-twin units, offering the possibility of split trunking if needed in the future.