Steering Defects and Their Remedies
Page 63
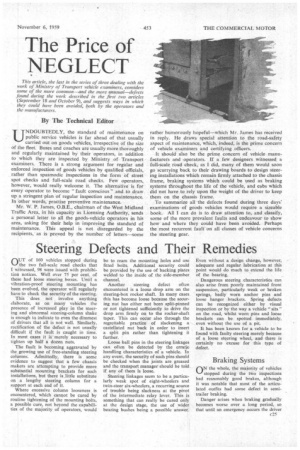
Page 64
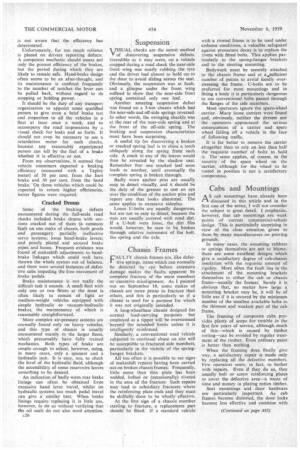
Page 67
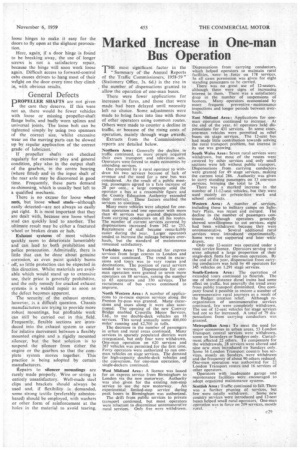
If you've noticed an error in this article please click here to report it so we can fix it.
OUT of 160 vehicles stopped during the two full-scale road checks that I witnessed, 98 were issued with prohibition notices. Well over 75 per cent, of these had loose steering boxes. Until a vibration-proof steering mounting has been evolved, the operator will regularly have to check the security of the steering.
This does not involve anything elaborate, as on many vehicles the presence of increased play in the steering and abnormal steering-column shake is enough to indicate to even the dimmest of drivers that all is not well. Similarly, rectification of the defect is not usually difficult if the fault is caught in time. In most cases it is merely necessary to tighten up half a dozen nuts.
The fault is becoming aggravated by the growing use of free-standing steering columns. Admittedly, there is some evidence to suggest that a few chassis makers are attempting to provide more substantial mounting brackets for such installations, but there is little substitute on a lengthy steering column for a support at each end of it.
Where excessive column looseness is encountered, which cannot be cured by routine tightening of the mounting bolts, a possible cure, not beyond the capabilities of the majority of operators, would be to ream the mounting holes and use fitted bolts. Additional security could be provided by the use of backing plates welded to the inside of the side-member channel.
Another steering defect often encountered is a loose drop arm on the steering-box rocker shaft. In many cases this has become loose because the securing nut has either not been split-pinned or not tightened sufficiently to drive the drop arm firmly on to the rocker-shaft taper. This can occur also through the regrettable practice of slackening a castellated nut back in order to insert a split pin rather than tightening it further. •
Loose ball pins in the steering linkages can often be detected by the erratic handling characteristics of a vehicle. In any event, the security of such pins should be checked when the joints are greased and the transport manager should be told if any of them is loose.
Steering linkages seem to be a particularly weak spot of eight-wheelers and twin-steer six-wheelers, a recurring source of trouble being slackness at the pivot of the intermediate relay lever. This is something that can really be cured only at the design stage, the use of wider bearing bushes being a possible answer.
Even without a design change, however, adequate and regular lubrication at this point would do much to extend the life of the bearing.
Dangerous steering characteristics can also arise from poorly maintained front suspension, particularly weak or broken springs, badly worn anchor pins and loose hanger brackets. Spring defects can be recognized either by visual inspection or by the way a vehicle " sits" on the road, whilst worn pins and loose brackets can be spotted immediately, even without the use of a pit.
It has been known for a vehicle to be found with faulty steering merely because of a loose steering wheel, and there is certainly no excuse for this type of defect.
Braking Systems
ON the whole, the majority of vehicles stopped during the two inspections had reasonably good brakes, although it was notable that most of the articulated outfits had some defect in semitrailer braking.
Danger arises when braking gradually becomes worse over a long period, so that until an emergency occurs the driver c25 is not aware that the efficiency has deteriorated.
Unfortunately, far too much reliance is placed on drivers reporting defects. A competent mechanic should assess not only the present efficiency of the brakes, hut the period during which they are likely to remain safe. Hand-brake design often seems to be an after-thought, and its maintenance is confined frequently to the number of notches the lever can be pulled back, without regard to its stopping or holding power.
It should be the duty of any transport organization to appoint some qualified person to give even a brief brake test and inspection to all the vehicles in a fleet at least once a week, and to accompany the road impressions by a visual check for leaks and so forth. It should not even be necessary to use a retardation meter for such checks. because any reasonably experienced person can tell by the feel of a brake whether it is effective or not.
From my observations, it seemed that vehicle examiners expected a braking efficiency (measured with a Tapley meter) of 50 per cent, from the foot brake and 30 per cent, from the hand brake:-On those vehicles which could be expected to return higher efficiencies, better figures were required, Cracked Drums
Some of the braking defects encountered during the full-scale road cheeks included brake drums with sections cracked out of them (a common fault on one make of chassis, both goods and passenger); partially ineffective servo systems; loose hand-brake levers; and poorly placed and secured brake pipes and hoses: Frequent evidence was found of makeshift adjustments to handbrake linkages which could well have thrown the whole _system out of balance, and there were several instances of defecfive cabs impeding the free movement of ,brake pedals.
Brake maintenance is not really the difficult task it sounds. A small fleet with only one or two fitters at the Most is often likely to consist of light or medium-weight vehicles equipped with simple hydraulic or vacuum-hydraulic brakes; the maintenance of which is reasonably straightforward.
-More complex air-pressure systems are normally found only on heavy vehicles, and this . type of chassis is usually encountered mainly in the larger fleets, which presumably have fully trained mechanics. Both types of brake are simple enough to adjust, however, using, in many eases, only a spanner and a hydraulic jack. It is easy, too, to check the level of the hydraulic fluid, although the accessibility of some reservoirs leaves something to be desired.
An indication of badly worn rear brake linings can often be obtained from excessive hand lever travel, whilst on hydraulic .systems too much pedal travel can give a similar hint. When brake linings require replacing it is little use, however, to do so without verifying that the oil seals do not also need attention.
c26
Suspension
mum., checks are the surest method V of discovering suspension defects. Incredible as it may seem, on a vehicle stopped during a road check the near-side front wing was nearly rubbing the tyre and the driver had almost to hold on to the door to avoid sliding across the seat. Obviously, the suspension was at fault, and a glimpse under the front wing sufficed to show that the near-side front spring contained only one leaf.
Another amazing suspension defect was found on a 3-ton chassis which had the near-side and off-side springs reversed. In other words, the swinging shackle was at the rear of the near-side spring and at the front of the off-side spring. The braking and suspension characteristics must have been surprising.
A useful tip for discovering a broken or cracked spring leaf is to shine a torch obliquely along the spring from each side. A crack in any of the leaves would then be revealed by the shadow cast. Remember that one cracked leaf soon leads to another, until eventually the complete spring is broken through.
Badly worn anchor pins are usually easy to detect visually, and it should be the duty of the greaser to cast an eye over the condition of the anchor pins and report any that looks abnormal, The same applies to excessive sidepIay.
Loose U-bolts are equally dangerous, but are not as easy to detect, because the Outs are usually covered with road dirt.. If a U-bolt were loose, the dirt film would. however, be seen to be broken through relative movement of the bolt, the spring and the axle.
• Chassis Frames
FA'ILTY chassis frames are, like defective springs, items which can normally be detected by eye before extensive damage makes the faults apparent by complete fracture of the main members or 'excessive misalignment. As I pointed out on September 18, some makes of chassis are more prone to fracture than others, and this is particularly so if a chassis is used for a purpose for which it was not originally intended.
A long-wheelbase chassis designed for normal load-carrying purposes but employed as a tipper will be overstressed -beyond the intended limits unless it is intelligently reinforced.
Similarly, a conventional road vehicle subjected to continual abuse on site will be susceptible to fractured side members, particularly in the vicinity of the springhanger brackets.
All too often it is possible to see signs of makeshift repairs. having been carried out on broken chassis frames. Frequently, little more than thin plate has been welded, bolted or (occasionally) riveted in the area of the fracture. Such repairs may lead to subsidiary fractures where the reinforcing plate ends and they must be skilfully done to be wholly effective.
At the first sign of a chassis member starting to fracture, a replacement part should be fitted. If a standard vehicle with 'a riveted frame is to be used under. arduous conditions, a valuable safeguard against premature decay is to replace the rivets with fitted bolts. This applies particularly to the spring-hanger brackets and to the steering mountieg.
Bodywork must be securely attached to the chassis frame and at _a sufficient number of points to avoid locally overstressing the frame, U-bolts are to be preferred for most mountings and in fitting a body it is particularly dangerous to use conventional bolts passed through the flanges of the side members.
Most operators ignore the spare-wheel carrier. Many loose carriers were found and, obviously, neither the drivers nor the operators appreciated the serious consequences of a carrier and spare wheel falling off a vehicle in. the face of following traffic.
It is far better to remove the carrier altogether than to rely on less than half the requisite number of bolts to hold it. The same applies, of course, to the security of the spare wheel on the carrier, although for the wheel to be rusted in position is not a satisfactory compromise.
Cabs and Mountings .
A S cab mountings have already been PA discussed in this article and in the first one of the series, I will not consider the subject in great detail. I emphasize, however, that cab mountings are weak points of current commercial-vehicle design. This is particularly surprising in view of the close attention given to them by many manufacturers on proving grounds.
In many cases, the mounting rubbers or springs themselves are not to blame; there are some excellent designs which give a, satisfactory degree of cab-chassis insulation with the requisite amount of rigidity. More often the fault lies in the attachment of the ,mounting brackets themselves to either the cab or chassis frame—usually the former. Surely it is obvious that, no matter how large a mounting bracket may be, it will be of little use if it is secured by the minimum number of the smallest available bolts to the thinnest and weakest part of the cab frame.
The framing of composite cabs provides plenty of scope for trouble in the first few years of service, although. much of this—which is caused by timber rotting—can be avoided by regular treatment of the timber. Even ordinary paint is better than nothing.
When the framing does finally give way, a satisfactory repair is made only by replacing all t_ e defective members. Few operators seem, in fact, to bother with repairs. Even if they do so, they usually bolt or screw reinforcing plates to cover the defective area—a waste of time and money in plating rotten timber.
Seat mountings and door hardware are particularly important. As cab frames become distorted, the door locks become less effective and cornbine with loose hinges to make it easy for the doors to fly open at the slightest provocation.
Here, again, if a door hinge is found to be breaking away, the use of longer screws is not a satisfactory repair, because the hinge will soon work loose again. Difficult Access to forward-control cabs causes drivers to hang most of their weIght on the door every time they climb in, with obvious results.
General Defects
Di MOELLER SHAFTS are not given I the care they deserve. If this were not so, there would be fewer vehicles with loose or missing propeller-shaft flange bolts, and badly worn splines and universal joints. The loose bolt can be tightened simply by using two spanners of the correct size, whilst excessive wear on the moving parts can be slowed up by regular application of the correct grade of lubricant.
• If propeller shafts are Checked regularly for excessive play and general condition, play also. in the output shaft of the gearbox, in the centre bearing (where fitted)and in the input shaft of the rear axle may be discovered in good time. Frequently, these parts demand re-shimming, which is usually best left to a qualified mechanic.
There is no excuse for loose wheel nuts, but loose wheel studs—although easily detected—are not always so easily put right, It is. most important that they are dealt with, because one loose wheel stud can quickly lead to another. The ultimate result may be either a fractured wheel. or broken drum Or hub,
Exhairst systems of most vehicles quickly seem to deteriorate lamentably and can lead to both prohibition and police prosecution. Admittedly, there is little that can be dope about genuine corrosion, as even paint quickly burns off; so little protection can be expected in this direction, Whilst materials are available which would stand up to extensive use, their price is generally prohibitive, and the only remedy for cracked exhaust systems is a welded repair as soon as the defect becomes apparent.
The security. of the exhaust system, however, is a difficult question. Chassis manufacturers are trying to provide more robust mountings, but profitable work can still be carried out in Allis . field. Frequently,. flexible sections are introduced into the exhaust system to eater for relative movement between a flexibly mounted engine and a rigidly mounted silencer, but the best solution is to' suspend. the silencer from either the engine or the gearbox so that the complete system moves together. This practice is being adopted by certain manufacturers.
Itepairs to silencer mountings are rarely made properly. Wire or string is entirely unsatisfactory. Well-made steel clips and brackets should always be used and, if flexibility is demanded, some strong textile (preferably asbestosbased) should be employed, with washers or other form of reinforcement at the holes in the material to avoid tearing.