Optrak's routeing and sc eduling package is complex but comprehensive
Page 38
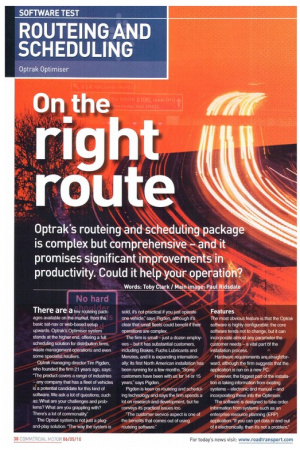
Page 39
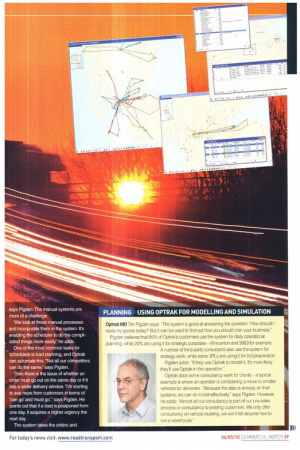
Page 40
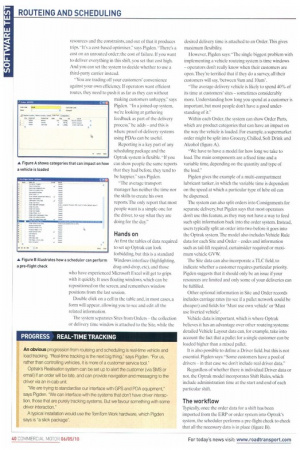
Page 41
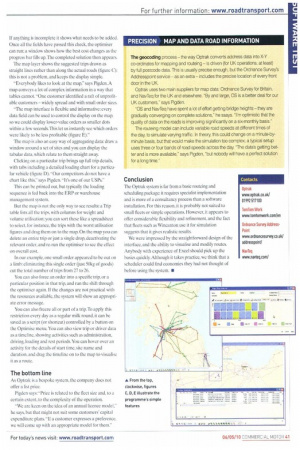
If you've noticed an error in this article please click here to report it so we can fix it.
and it promises significant improvements in productivity. Could it help your operatio
Words: Toby Clark / Main image: Paul Ridsdale INo hard There are a few routeing packages available on the market, from the basic sat-nay or web-based setup upwards. Optrak's Optimiser system stands at the higher end, offering a full scheduling solution for distribution firms, waste management operations and even some specialist hauliers
Optrak managing director Tim Pigden, who founded the firm 21 years ago, says. "The product covers a range of industries — any company that has a fleet of vehicles is a potential candidate for this kind of software. We ask a lot of questions, such as. What are your challenges and problems? What are you grappling with? There's a lot of commonality."
The Optrak system is not just a plugand-play solution The way the system is sold, its not practical if you just operate one vehicle," says Rgden, although its clear that small fleets could benefit if their operations are complex.
The firm is small — just a dozen employees — but it has substantial customers. including Brakes, Fuchs Lubricants and Menzies, and it is expanding internationally. its first North American installation has been running for a few months "Some customers have been with us for 14 or 15 years," says Pigden.
Ryden is keen on routeing and scheduling technology and says the firm spends a lot on research and development, but he conveys its practical issues too.
"The customer service aspect is one of the benefits that comes out of using routeing software"
Features
The most obvious feature is that the Optrak software is highly configurable: the core software tends not to change, but it can incorporate almost any parameter the customer needs — a vital part of the installation process Hardware requirements are straightforward, although the firm suggests that the application is run on a new PC.
However, the biggest part of the installation is taking information from existing systems — electronic and manual — and incorporating these into the Optimiser.
The software is designed to take order information from systems such as an enterprise resource planning (ERP) application "If you can get data in and out of it electronically, then it's not a problem," says Pigden The manual systems are more of a challenge.
We look at those manual processes and incorporate them in the system It's enabling the scheduler to do the complicated things more easily he adds
One of the most common tasks for schedulers is load planning, and Optrak can automate this "Not all our competitors can do the same: says Pigden.
Then there is the issue of whether an order must go out on the same day or if it has a wider delivery window. "I'm starting to see more from customers in terms of can go' and 'must go'," says Pigden. He points out that if a load is postponed from one day, it acquires a higher urgency the next day.
The system takes the orders and
resources and the constraints, and out of that it produces trips. "It's a cost-based optimiser,says Pigden. -There's a cost on an unrouted order; the cost of failure. If you want to deliver everything in this shift, you set that cost high. And you can set the system to decide whether to use a third-party carrier instead.
"You are trading off your customers' convenience against your own efficiency. If operators want efficient routes, they need to push it as far as they can without making customers unhappy," says Pigden. "In a joined-up system, we're looking at gathering feedback as part of the delivery process." he adds and this is where proof-of-delivery systems using PDAs can be useful.
Reporting is a key part of any scheduling package and the Optrak system is flexible. If you can show people the same reports that they had before, they tend to be happier.says Pigden.
"The average transport manager has neither the time nor the skills to create his own reports.The only report that most people want is a simple one for the driver, to say what they are doing for the day."
Hands on At first the tables of data required to set up Optrak can look forbidding, but this is a standard Windows interface (highlighting, drag-and-drop, etc), and those who have experienced Microsoft Excel will get to grips with it quickly. It uses floating windows, which can be repositioned on the screen, and remembers window positions from the last session.
Double click on a cell in the table and, in most cases, a form will appear, allowing you to see and edit all the related information.
Com
The system separates Sites from Orders the collection or delivery time window is attached to the Site. while the desired delivery time is attached to an Order. This gives maximum flexibility.
However, Pigden says: "The single biggest problem with implementing a vehicle routeing system is time windows operators don't really know when their customers are open.They're terrified that if they do a survey, all their customers will say, 'between 9am and lOarn'.
"The average delivery vehicle is likely to spend 40% of its time at customers' sites sometimes considerably more. Understanding how long you spend at a customer is important. but most people don't have a good understanding of it."
Within each Order, the system can show Order Parts, which are product categories that can have an impact on the way the vehicle is loaded. For example. a supermarket order might be split into Grocery, Chilled, Soft Drink and Alcohol (figure A).
"We have to have a model for how long we take to load. The main components are a fixed time and a variable time, depending on the quantity and type of the load."
Pigden gives the example of a multi-compartment lubricant tanker, in which the variable time is dependent on the speed at which a particular type of lube oil can be dispensed.
The system can also split orders into Consignments for separate delivery, but Pigden says that most operators don't use this feature, as they may not have a way to feed such split information hack into the order system. Instead, users typically split an order into two before it goes into the Optrak system. The model also includes Vehicle Rule data for each Site and Order codes and information such as tail-lift required, curtain.sider required or maximum vehicle GVW The Site data can also incorporate a TLC field, to indicate whether a customer requires particular priority Pigden suggests that it should only be an issue if your resources are limited and only some of your deliveries can be fulfilled.
Other optional information in Site and Order records includes carriage rates (to see if a pallet network could be cheaper) and fields for 'Must use own vehicle' or 'Must use liveried vehicle'.
Vehicle data is important, which is where Optrak believes it has an advantage over other routeing systems: detailed Vehicle Layout data can, for example, take into account the fact that a pallet for a single customer can be loaded higher than a mixed pallet.
It is also possible to define a Driver field, but this is not essential. Pigden says: "Some customers have a pool of drivers in that case we don't include real driver data."
Regardless of whether there is individual Driver data or not, the Optrak model incorporates Shift Rules, which include administration time at the start and end of each particular shift, The workflow Typically, once the order data for a shift has been imported from the ERP or order system into Optrak's system, the scheduler performs a pre-flight check to check that all the necessary data is in place (figure B). If anything is incomplete it shows what needs to be added. Once all the fields have passed this check, the optimiser can run; a window shows how the best cost changes as the progress bar fills up. The completed solution then appears.
The map layer shows the suggested trips drawn as straight lines rather than along the actual roads (figure C): this is not a problem, and keeps the display simple.
"Everybody likes to look at the map," says Pigden. A map conveys a lot of complex information in a way that tables cannot. "One customer identified a raft of unprofitable customers — widely spread and with small order sizes.
"The map interface is flexible and informative: every data field can be used to control the display on the map. so we could display lower-value orders as smaller dots within a few seconds. This let us instantly see which orders were likely to be less profitable (figure E)."
The map is also an easy way of aggregating data: draw a window around a set of sites and you can display the tabular data, which relate to them straight away Clicking on a particular trip brings up full trip details, with tabs including a detailed loading chart for a particular vehicle (figure D). "Our competitors do not have a chart like this," says Pigden. "It's one of our I.:SPs."
This can be printed out, but typically the loading sequence is fed back into the ERP or warehouse management system.
But the map is not the only way to see results: a Trip table lists all the trips, with columns for weight and volume utilisation; you can sort these like a spreadsheet to select, for instance, the trips with the worst utilisation figures and drag them on to the map. On the map you can delete an entire trip or just a single drop, deactivating the relevant order, and re-run the optimiser to see the effect on overall cost.
In our example, one small order appeared to be out on a limb: eliminating this single order (just 50kg of goods) cut the total number of trips from 27 to 26.
You can also force an order into a specific trip, or a particular position in that trip, and run the shift through the optimiser again. If the changes are not practical with the resources available, the system will show an appropriate error message.
You can also freeze all or part of a trip. To apply this restriction every day as a regular milk round, it can be saved as a script (or shortcut) controlled by a button on the Optimise menu. You can also view trip or driver data as a timeline, showing activities such as administration, driving, loading and rest periods. You can hover over an activity for the details of start time, site name and duration, and drag the timeline on to the map to visualise it as a route.
The bottom line
As Optrak is a bespoke system, the company does not offer a list price.
Pigden says: "Price is related to the fleet size and. to a certain extent, to the complexity of the operation.
"We are keen on the idea of an annual licence model,he says, but that might not suit some customers' capital expenditure plans. "If a customer expresses a preference. we will come up with an appropriate model for them."
Conclusion
The Optrak system is far from a basic routeing and scheduling package: it requires specialist implementation and is more of a consultancy process than a software installation. For this reason, it is probably not suited to small fleets or simple operations. However, it appears to offer considerable flexibility and refinement, and the fact that fleets such as Wincanton use it for simulation suggests that it gives realistic results.
We were impressed by the straightforward design of the interface, and the ability to visualise and modify routes. Anybody with experience of Excel should pick up the basics quickly. Although it takes practice, we think that a scheduler could find economies they had not thought of before using the system. E