Geared to the Future
Page 128
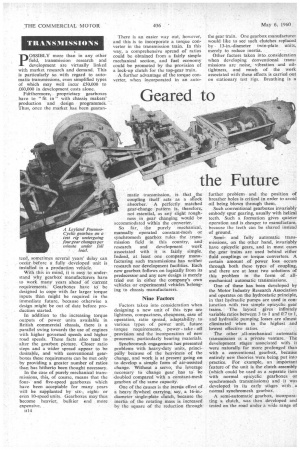
Page 129
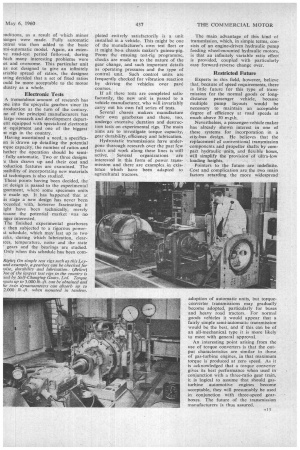
If you've noticed an error in this article please click here to report it so we can fix it.
TRANSMISSIONS
POSSIBLY more than in any other field, transmission research and development are virtually linked with market research and demand. This is particularly so with regard to automatic transmissions, even simplified types of which may well incur 00,000 to I60,000 in development costs alone.
Fuithermore, proprietary gearboxes have to "fit in" with chassis makers' production and design programmes. Thus, once the market has been cuaran teed, sometimes several years' delay can occur before a fully developed unit is installed in a production vehicle.
With this in mind, it is easy to understand why gearbok manufacturers have to work many years ahead of current requirements. Gearboxes have to be designed to cope with far larger torque inputs than might be required in the immediate future, because otherwise a design might be out of date before production started.
In addition to the increasing torque outputs of power units available in British commercial chassis, there is a parallel swing towards the use of engines with higher governed speeds and higher road speeds. These facts also tend to alter the gearbox picture. Closer ratio steps and a wider spread appear to be desirable, and with conventional gearboxes these requirements can be met only by providing a greater number of ratios than has hitherto been thought necessary.
In the case of purely mechanical transmissions, this, of course, means that the fourand five-speed gearboxes which have been acceptable for many years will be supplanted by six-, eightor even 10-speed units. Gearboxes may thus become heavier, bulkier and more expensive.
1414 There is an easier way out, however, and this is to incorporate a torque converter in the transmission train. In this way, a comprehensive spread of" ratios could be obtained from a fairly simple mechanical section, and fuel economy could be promoted by the provision of a lock-up clutch for the top-gear train.
A further advantage of the torque converter. when incorporated in an auto
matic transmission, is that the coupling itself acts as a shock absorber. A perfectly matched gear-change pattern is, therefore, not essential, as any slight roughness in gear changing would be accommodated within the converter.
So far, the purely mechanical, manually operated constant-mesh or synchromesh gearbox rules the transmission field in this country, and research and development work associated with it is fairly simple. Indeed, at least one company manufacturing such transmissions has neither research nor development facilities. Each new gearbox follows on logically from its predecessor and any new design is merely tried out in either the company's own vehicles or experimental vehicles *belonging to chassis manufacturers.
Nine Factors
Factors taken into consideration when designing a new unit of this type are lightness, compactness, cheapness, ease of operation, ratio spread, adaptability to various types of power unit, future torque requirements, power take off provision and the incorporation of new processes, particularly bearing materials.
Synchromesh engagement has presented problems with heavy-duty units, principally because of the heaviness of the change, and work is at present going on to develop a simple form of air-assisted change. Without a servo, the leverage necessary to change gear has to be doubled compared with a constant-mesh gearbox of the same capacity.
One of the causes is the inertia effect of a heavy flywheel carrying, say, a 16-in.diameter single-plate clutch, because the inertia of the rotating mass is increased by the square of the reduction through the gear train. One gearbox manufacturer would like to see such clutches replaced by • 13-in.-diameter twin-plate units, merely to reduce inertia.
Other factors taken into consideration when developing conventional transmissions are noise, vibration and oiltightness, and much of the work associated with these effects is carried out on stationary test rigs. Breathing is a further problem and the position of breather holes is critical in order to avoid oil being blown through them.
Such conventional gearboxes invariably embody spur gearing, usually with helical teeth. Such a formation gives quieter operation and is cheaper to manufacture, because the teeth can be shaved instead of ground.
Semiand fully automatic transmissions, on the other hand, invariably have epieyelic gears, and in most cases the gear trains are used behind either fluid couplings or torque converters. A certain amount of power loss occurs through both these types of coupling, and there are at least two solutions of this problem in the form of allmechanical automatic transmissions.
One of these has been developed by the Motor Industry Research Association and operates on the hydrostatic principle, in that hydraulic pumps are used in conjunction with two simple epicyclic gear trains. The layout gives infinitely variable ratios between 3 to 1 and a7 to 1, and hydraulic pumping hisses are almost eliminated when in the highest and lowest effective ratios.
The other all-mechanical automatic transmission is a private venture. The development stages associated with it were naturally far more prolonged than with a conventional gearbox, because entirely new theories were being put into practice. For example, an important feature of the unit is the clutch assembly (which could be used as a separate item with normal epicyclic gearboxes or synchromesh transmissions) and it was developed in its early stages with a normal synchromesh gearbox.
A semi-automatic gearbox, incorporating a clutch, was then developed and tested on the road under a wide range of
mditions, as a result of which minor ianges were made. Fully automatic 3ntrol was then added to the basic !mi-automatic model. Again, an extenve road-test period followed, during hich many interesting problems were tet and overcome. This particular unit as not designed to give an infinitely triable spread of ratios, the designer wing decided that a set of fixed ratios ould be more acceptable to the motor Ldustry as a whole.
Electronic Tests
A tremendous amount of research has The into the epicyclic gearbox since its rtroduction at the turn of the century. ne of the principal manufacturers has large research and development departent equipped with specialized electronic st equipment and one of the biggest St rigs in the country.
Having ascertained a need, a specificaon is 'drawn up detailing the potential irque capacity, the number of ratios and hether the operation should be semifully automatic. Two or three designs -e then drawn up and their cost and -oduction features are examined. The 3ssibility of incorporating new materials id techniques is also studied.
These points having been decided, the !st design is passed to the experimental :partment, where some specimen units 'e made up. It has happened that at Lis stage a new design has never been -oceeded with, however fascinating it ight have been technically, merely !cause the potential market was no nger interested.
The finished experimental gearboxes e then subjected to a rigorous powerst schedule, which may last up to two eeks, during which lubrication, clearices, temperature, noise and the state gears and the bearings are studied. Only when this schedule has been corn
pieted entirely satisfactorily is a unit installed in a vehicle. This might be one of the manufacturer's own test fleet or it might be,a chassis maker's guinea-pig. From the ensuing test-rig programme, checks are made as to the nature of the gear change, and such important details as operating pressures and the type of control unit. Such control units are frequently checked for vibration reaction by driving the vehicles over pave courses.
If all these tests are completed satisfactorily, the new unit is passed to a vehicle manufacturer, who will invariably carry out his own full series of tests.
Several chassis makers manufacture their own gearboxes and these, too, undergo extensive duration and destruction tests on experimental rigs. The main aims are to investigate torque capacity, gear durability, efficiency and lubrication.
Hydrostatic transmissions have undergone thorough research over the past few years and work along these lines is still active. Several organizations are interested in this form of. power. transmission and there are examples in existence which have been adapted to agricultural tractors. The main advantage of this kind of transmission, which, in simple terms, consists of an engine-driven hydraulic pump feeding wheel-mounted hydraulic motors, is that an infinitely variable ratio effect is provided, coupled with particularly easy forward-reverse change over.
Restricted Future
Experts in this field, however, believe that, because of speed requirements, there is little future for this type of transmission for the normal goods or longdistance passenger vehicle, because multiple pump layouts would be necessary to maintain an acceptable degree of efficiency at road speeds at much above 30 m.p.h.
Nevertheless, a passenger-vehicle maker has already shown interest in one of these systems for incorporation in a city-bus design. He believes that the replacement of conventional transmission components and propeller shafts by compact hydraulic units, and flexible hoses, will simplify the provision of ultra-low loading heights. •
Pointers to .tbe future •are indefinite. Cost and complication are the two main factors retarding the more widespread
adoption of automatic units, but torqueconverter transmissions may gradually become adopted, particularly for buses and heavy road tractors. For normal goods vehicles it would appear that a fairly, simple semi-automatic transmission would be the best, and if this can be of an all-mechanical, type it is more likely to meet with general approval.
An interesting point arising from the use of torque converters is that the output characteristics are similar to those of gas-turbine engines, in that maximum torque is produced at zero speed. As it is acknowledged that a torque converter gives its best performance when used in conjunction with a three-ratio gear train, it is logical to assume that should gasturbine automotive engines become acceptable, they will presumably be used in conjunction with three-speed gearboxes. The future of the transmission manufacturers is thus assured.