PLASTICS RE] COST AND WEIGHT
Page 60
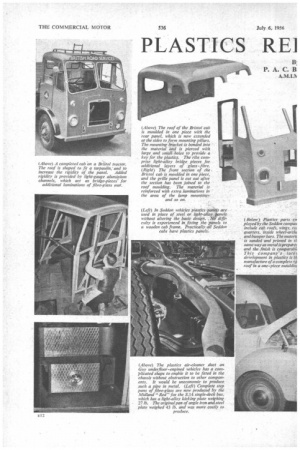
Page 61
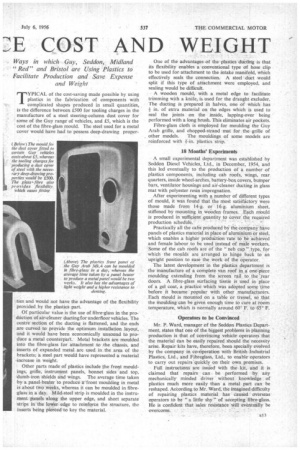
Page 62
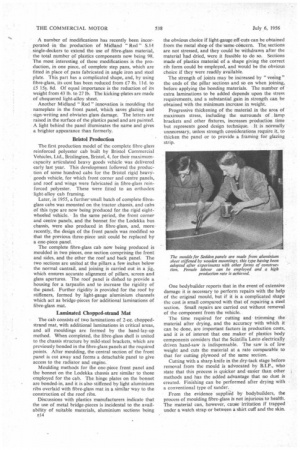
If you've noticed an error in this article please click here to report it so we can fix it.
Ways in which Guy, Seddon,. Midland "Red" and Bristol are Using Plastics to Facilitate Production and Save Expense and Weight
TYPICAL of the cost-saving made possible by using plastics in the fabrication of components with complicated shapes produced in small quantities, is the difference between £500 for tooling charges in the manufacture of a steel steering-column dust cover for some of the Guy range of vehicles, and ES, which is the cost of the fibre-glass mould. The steel used for a metal cover would have had to possess deep-drawing proper ties and would not have the advantage of the flexibility Provided by the plastics part.
Of particular value is the use of fibre-glass in the production of aircleaner ducting-for underfloor vehicles. The centre section of the ducting is flattened, and the ends are curved to provide the optimum installation layout, -and it would have been economically unsound to produce a metal counterpart. Metal brackets are moulded into the fibre-glass for attachment to the chassis, and inserts of expanded metal are used in the area of the brackets; a steel part would have represented a material -increase in weight.
Other parts made of plastics include the front mouldings, grille, instrument panels, bonnet sides and top, dumb-iron shields and wings. The average time taken by a .panel-beater to produce a front moulding in metal is about two weeks, whereas it can be moulded in fibreglass in a day. Mild-steel strip is moulded in the instrument panels along the upper edge, and short separate strips in the loWer edge to reinforce the structure, the inserts being pierced to key the material. One of the advantages of the plastics ducting is that its flexibility enables a conventional type of hose clip to be used for attachment to the intake manifold, which effectively seals the connection. A steel :duct -would split if this type of attachment were employed, and sealing would be difficult.
A wooden mould, with a metal edge to facilitate trimming with a knife, is used for the draught excluder. The ducting is prepared in halves, one of which has -} in. of extra material on the edges which is used to seal the joints on the inside, lapping-over being performed with a long brush. This eliminates air pockets.
Fibre-glass cloth is employed for moulding the Guy Arab grille, and chopped-strand mat for the grille of other models. The mouldings of some models are reinforced with plastics strip.
18 Months' Experiments
A small experimental department was established by Seddon Diesel Vehicles, Ltd., in December, 1954, and this led eventually to the production of a number of plastics components, including cab roofs, wings, rear quarters, inside wheel-arches, battery-box covers, bumper bars, ventilator housings and air-cleaner ducting in glass mat with polyester resin impregnation.
After experimenting with a number of different types of mould, it was found that the most satiifictory were those made from 14-g. or 16-g. aluminium sheet, stiffened by mounting in wooden frames. Each niould is produced in sufficient 9nanfity to Cover the required production schedule. r • Practically all the cabs produced by the company have panels of plastics material in place of aluminium or steel, which enables a higher production rate to be 'achieved and female labour to be used instead of male workers. Some of the cab roofs are of the " neb cap "type, for which the moulds are arranged to hinge back to an upright position to ease the work of the operator.
The latest development in the plastics department is the manufacture of a complete van roof in a one:piece moulding extending from the 'screen rail to the -year doors. A fibre-glass surfacing tissue is used in place of a gel coat, a practice which was adopted some time before it became popular with, other manufacturers. Each mould is mounted on a table or tressel, so that the moulding can be given enough time to cure at room temperature, which is normally around 60°F. to 65° F.
Operators to be Convinced
Mr. P. Ward, manager of the Seddon Plastics Department, states that one of the biggest problems in planning production is that of convincing vehicle operators that the material can be easily repaired should the necessity arise. Repair kits have, therefore, been specially evolved by the company in co-operation with British Industrial Plastics, Ltd., and Fibreglass, Ltd., to enable operators to carry out repairs 'quickly on their own premises.
Full instructions are issued with the kit, and it is claimed that repairs can be performed by any mechanically minded driver without knowledge of plastics much more easily than a metal part can be reshaped. According to Mr. Ward, the imagined difficulty of repairing plastics material has caused overseas operators to be " a little shy" of accepting fibre-glass. He is confident that sales resistance 'Will eventually be overcome. A number of modifications has recently been incorporated in the production of Midland " Red " S.14 single-deckers to extend the use of fibre-glass material, the total number of plastics components now being 98. The most interesting of these modifications is the production, in one piece, of complete step pans, which are fitted in place of pans fabricated in angle iron and steel plate. This part has a complicated shape, and, by using fibre-glass, its cost has been reduced from £7 8s. 11d. to £5 15s. 8d. Of equal importance is the reduction of its weight from 43 lb. to 27 lb. The kicking-plates are made of chequered light-alloy sheet.
Another Midland " Red " innovation is moulding the nameplate in the front panel, which saves glazing and sign-writing and obviates glass damage. The letters are raised in the surface of the plastics panel and are painted. A light behind the panel illuminates the name and gives a brighter appearance than formerly.
Bristol Production
The first production model of the complete fibre-glass reinforced polyester cab built by Bristol Commercial Vehicles, Ltd., Brislington, Bristol, 4, for their maximumcapacity articulated heavy goods vehicle was delivered early last year. This development followed the production of some hundred cabs for the Bristol rigid heavygoods vehicle, for which front corner and centre panels, and roof and wings were fabricated in fibre-glass reinforced polyester. These were fitted to an orthodox light-alloy cab framing.
Later, in 1955, a further-small batch of complete fibreglass cabs was mounted on the tractor chassis, and cabs of this type are now being produced for the rigid eightwheeled vehicle. In the same period, the front corner and centre panels, and the bonnet for the Lodekka bus chassis, were also produced in fibre-glass, and, more recently, the design of the front panels was modified so that the previous three-piece unit could be replaced by a one-piece panel.
The complete fibre-glass cab now being produced is moulded in two pieces, one section comprising the front and sides, and the other the roof and back panel. The two sections are united at the pillars a few inches below the normal cantrail, and joining is carried out in a jig, which ensures accurate alignment of pillars, screen and glass apertures. The roof panel is dished to provide a housing for a tarpaulin and to increase the rigidity of the panel. Further rigidity is provided for the roof by stiffeners, formed by light-gauge aluminium channels which act as bridge-pieces for additional laminations of fibre-glass mat.
Laminated chopped-strand Mat
The cab consists of two laminations of 2-oz. choppedstrand mat, with additional laminations in critical areas, and all mouldings are formed by the hand-lay-up method. When completed, the fibre-glass shell is united to the chassis structure by mild-steel brackets, which are previously bonded in the fibre-glass panels at the required points. After moulding, the central section of the front panel is cut away and forms a detachable panel to give access to the radiator and engine.
Moulding methods for the one-piece front panel and the bonnet on the Lotiekka chassis are similar to those employed for the cab. The hinge plates on the bonnet are bonded-in, and it is also stiffened by light aluminium ribs overlaid with fibre-glass mat in a similar way to the construction of the roof ribs.
Discussions with plastics manufacturers indicate that the use of metal bridge-pieces is incidental to the availability of suitable materials, aluminium sections being the obvious choice if light-gauge off-cuts can be obtained from the metal shop of the same concern. The sections are not stressed, and they could be withdrawn after the material had dried, were it feasible to do so. Sections made of plastics material of a shape giving the correct rib form could be employed, and would be the obvious choice if they were readily available.
The strength of joints may be increased by " veeing " the ends of the pillar sections and so on when joining, before applying the bonding materials. The number of extra laminations to be added depends upon the stress requirements, and a substantial gain in strength can be obtained with the minimum increase in weight.
Progressive thickening of the material in the area of maximum stress, including the surrounds of lamp brackets and other fixtures, increases production time but represents good design technique. it is normally unnecessary, unless strength considerations require it, to thicken the panel or to provide a framing for glazing strip.
One bodybuilder reports that in the event of extensive damage it is necessary to perform repairs with the help of the original mould, but if it is a complicated shape the cost is small compared with that of repairing a steel section. Small repairs are carried out without removal of the component from the vehicle..
The time required for cutting and trimming the material after drying, and the accuracy with which it can be done, are important factors in production costs, and it is of interest that one maker of plastics body components considers that the Scintilla Lesto electrically driven hand-saw is indispensable. The saw is of low weight and cuts the material at a rate comparable to that for cutting plywood of the same section.
Cutting with a sharp knife in the dry-tack stage before removal from the mould is advocated by B.I.P., who state that this process is quicker and easier than other methods and has the added advantage that no dust is created. Finishing can be performed after drying with a conventional type of sander.
From the evidence supplied by bodybuilders, the process of moulding fibre-glass is not injurious to health. The material can, however, cause irritation if trapped under a watch strap or between a shirt cuff and the skin.