Makers versus Users on Injection Equipment
Page 59
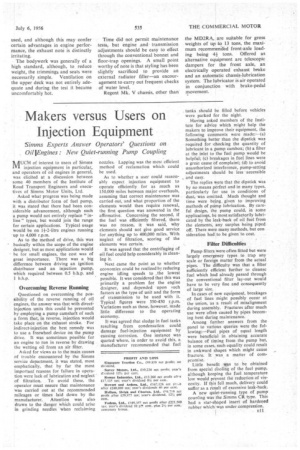
If you've noticed an error in this article please click here to report it so we can fix it.
Simms Experts Answer Operators' Questions on OillEngines : New Quiet-running Pump Coupling
MUCH of interest to users of Simms injection equipment in particular, and operators of oil engines in general, was elicited at a discussion between some 40 members of the Institute of Road Transport Engineers and executives of Simms Motor Units, Ltd.
Asked what progress was being made with a distributor form of fuel pump, it was stated that there had been considerable advancement, although such a pump would not entirely replace " inline " types, but would join the range for certain applications. Typical usage would be on 1+-2-litre engines running up to 4,000 r.p.m.
As to the method of drive, this was basically within the scope of the engine designer, but as most applications would be for small engines, the cost was of great importance. There was a big difference between driving an ignition distributor and an injection pump, which required between 0.5 b.h.p. and 1 b.h.p.
Overcoming Reverse Running
Questioned on overcoming the possibility of the reverse running of oil engines, the answer was that with directinjection units this could be prevented by employing a pump camshaft of such a form that, in reverse, injection would take place on the exhaust stroke. For indirect-injection the best remedy was to use a freewheel device on the pump drive. It was sometimes possible for an engine to run in reverse by drawing the wetting oil from an air filter.
Asked for views as to the main causes of trouble encountered by the Simms service department, it was stated, most emphatically, that by far the most important reasons for failure in operation were lack of lubrication and neglect of filtration. To avoid these, the operator must ensure that maintenance was carried out at the recommended mileages or times laid down by the manufacturer. Attention was also drawn to the danger which could arise in grinding needles when reclaiming nozzles. Lapping was the most efficient method of reclamation which could be used.
As to whether a user could reasonably expect injection equipment to operate efficiently for as much as 150,000 miles between major overhauls, assuming that correct maintenance was carried out, and what proportion of the elements would then require renewal, the first question was answered in the affirmative. Concerning the second, if the fuel was efficiently filtered, there was no reason, it was said, why elements should not give good service for anything up to 400,000 miles. With neglect of filtration, scoring of the elements was certain.
It was agreed that the centrifuging of oil fuel could help considerably in cleaning it.
Next came the point as to whether economies could be realized by reducing engine idling speeds to .the lowest possible. It was considered that this was primarily a problem for the engine designer, and depended upon such factors as the type of unit and the form of transmission to be used with it. Typical figures were 350-450 r.p.m. Variations such as these, however, made little difference to the operating economy.
It was agreed that sludge in fuel tanks resulting from condensation could damage fuel-injection equipment by causing corrosion. One instance was quoted where, in order to avoid this, a manufacturer recommended that fuel tanks should be filled before vehicles were parked for the night.
Having asked members of the Institute for advice which might help the makers to improve their equipment, the following comments were made:—(a) Something better than the dipstick was required for .checking the quantity of lubricant in a pump cambox; (b) a filter at the inlet to the fuel pump would be helpful; (c) breakages in fuel lines were a great cause of complaint; (d) to avoid unauthorized interference, pump-setting adjustments should be less accessible and easy.
The replies were that the dipstick was by no means perfect and in many types, particularly for use in conditions of dust, was omitted. Much thought and time were being. given to improving methods of pump lubrication. By careful design, the pump could, in some applicatio9s, be most satisfactorily lubricated by the leak-back of oil fuel from the elements, any surplus being piped off. There were many methods, but con sideration had to be given to cost.
Filter Difficulties
Pump filters were often fitted but were largely emergency types to trap any scale or foreign matter from the actual pipes. The difficulty was that a filter sufficiently efficient further to cleanse fuel which had already passed through the conventional filter lay-out would have to be very fine and consequently of large size.
In cases of new equipment, breakages of fuel lines might possibly occur at the union, as a result of misalignment during assembly. Fractures after much use were often caused by pipes becoming bent during maintenance.
Among further answers from the panel to various queries were the following:—Fuel pipes of equal length were beneficial in obtaining accurate balance of timing from the pump but, in some cases, such equality could result in awkward shapes which might cause fracture. It was a matter of compromise.
Little benefit was to be obtained from special Cooling of the fuel pump, although keeping the fuel temperature low would prevent the reduction of viscosity. If this fell much, delivery could suffer as a result of excessive leak-back.
A new quiet-running type of pump coupling was the Simms CR type. This had a star-shaped insert of hardened rubber which was under compression.