LEYLAND'S VITAL CON
Page 26
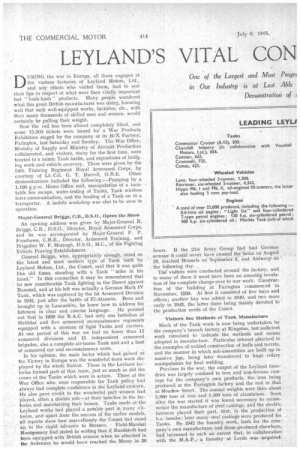
Page 27
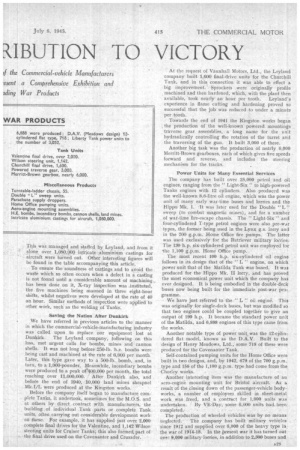
Page 28
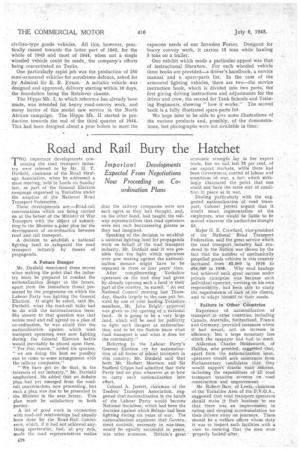
If you've noticed an error in this article please click here to report it so we can fix it.
IBUTION TO VICTORY
On ol the Largest and Most Progn in Our Industry is at Last Able Demonstration of 1 J. the Commercial-vehicle Manufacturers .esent a Comprehensive Exhibition and iding War Products D' URING the war in Europe, all those engaged at the various factories of Leyland Motors, Ltd., and any others who visited them, had to seal their lips in respect of what were then vitally important but " hush-hush " products. Many people wondered what this great British manufacturer was doing, knowing well that such well-equipped works, factories, etc., with Clout many thousands of skilled men and women, would certainly be pulling their weight.
Now the veil has been almost completely lifted, and some 15,000 tickets were issued fora War Products Exhibition staged by the company at its B/X Factory, Faring-ton, last Saturday and Sunday. The War Office, Ministry of Supply and Ministry of Aircraft Production collaborated, and visitors, many for the first time, were treated to a mimic Tank battle, and expositions of bridging work and vehicle recovery. These were given by the 54th Training Regiment Royal Armoured Corps, by
courtesy of Lt.-Col. G. T. Burrell, O.B.E. Other demonstrations included the following :—Pumping by a 1,100 g.p.m. Home Office unit, manipulation of a turntable fire escape, water-testing of Tanks, Tank wireless inter-communication, and the loading of a Tank on to a transporter. A mobile workshop was also to be seen in operation.
Major-General Briggs, C.B., D.S.O., Opens the Show An opening address was given by Major-General R. Briggs, C.B.• D.S.O., Director, Royal Arinoured Corps, and he was accompanied by Major-General F. P. Fanshawe, C.B.E., Director, Armoured Training, and Brigadier W. F. Morrogh, D.S.O., M.G., of the Fighting Vehicle Proving Establishment.
General Briggs, who, appropriately enough, stood on the latest and Most modern type of Tank built by Leyland Motors,. Ltd., the Comet, said that it was quite like old times, standing with a Tank "mike in his hand." In this connection it may be remembered that he saw considerable Tank fighting in the Desert against Rommel, and at his left was actually a German Mark IV Tank, which was captured by the 1st Armoured Division in 1042, just after the battle of El-Alamein. Born and brought up in Lancashire, he knew how to address his listeners in clear and concise language. He pointed out that in 1939 the R.A.C. had only one battalion of Matildas and five armoured reconnaissance regiments equipped with a mixture of light Tanks and carriers. At one period of this war we had no fewer than 11 armoured divisions and 15 independent armoured brigades, also a complete air-borne Tank unit and a host of armoured car and reconnaissance units.
In his opinion, the main factor which had gained us the Victory in Europe was the wonderful team work displayed by the whole Nation. Those in the Leyland factories formed part of that team, just as much as did the crews of the Tanks which were in action. Those at the War Office who were responsible for Tank policy had always had complete confidence in the Leyland concern. He also gave credit to the wonderful part women had played, often a double role—at their benches in the factories and maintaining their homes. Tanks made at the Leyland works had played a notable part in many victories, and apart from the success of the earlier models, all reports show how marvelously the Cornet had stood up to the rapid advanee to •Brernen, Field-Marshal Montgomery had stated in writing that if Rundstedt had been equipped with British armour when he attacked in the Ardennes he would have reached the Meuse in 36 hours. If the 21st Army Group had had German armour it could never have crossed the Seine on August 28, reached Brussels on 'September 3, and Antwerp ' the following day.
The-visitors were conducted around the factory, and to many of them it 'must have been an amazing revelation of the complete change-over to war work. Construction of thebuilding at Farington commenced in November, 1939. At first it consisted of five bays and offices; another bay was added in 1940, and two more early in 1943, the latter three being mainly devoted to the production needs of the Comet.
Visitors See Methods of Tank Manufacture Much Of the Tank work is now being undertaken by the company's branch factory at Kingston, but sufficient work remained to indicate the methods and means adopted in manufacture. Particular interest attached to the examples of welded construction of hulls and turrets, and the manner in which sub-assemblies are built ,up in massive_ jigs, being later transferred to huge rofary manipulators for final welding.
Previous to the war, the output, of the Leyland foun; dries was largely confined to iron and non-ferrous castings for the company's own products; the iron being _produced, at the Faringtdri factory and the rest in that at Meadow Street. The annual weights were then about 2,860 tons of iron and 1,500 tons of aluminium. Soon after the war started it was found necessary to recommence the manufacture of steel'castings, and the electric furnaces played their part, first, in the production of h.e.•bombs; latermany steel castings were produced fot Tanks, .By 1942 the foundry work,. both for the coin-pany's own manufactures and those produced elsewhere, had increased to such an extent that, in collaboration with the M.A.P.,a foundryat Leeds was acquired-,
This was managed and staffed by Leyland, and from it alone, over 1,080,000 intricate .aluminium castings for aircraft were turned out. Other interesting figures will be found in the table accompanying this article.
To ensure the soundness of castings and to aVoid the waste which so often occurs when a defect in a casting is not found until a considerable amount of machining, has been done on it, X-ray inspection was .instituted, the live machines being manned in three eight-hour shifts, whilst negatives were developed at the rate of 40 an hour. Similar methods of inspection were applied to other work, such as the welding of Tanks.
Saving the Nation After Dunkirk
We have referred in previous articles to the manner in which the commercial-vehicle-manufacturing industry was called upon to replace our 'equipment lost at Dunkirk. The Leyland company, following on this loss, met urgent calls for bombs, mines and cannon shells. It was not long before 250-1b. h.e. bombs were being cast and machined at the rate of 6,000 per month. Later, this type gave way to a 500-1b. bomb,. and,. in turn, to a 1,000-pounder, Meanwhile, incendiary bombs were produced to a peak o400,000 per month, the total reaching over 11,000,000. • After Dunkirk also, and before the end of 1940, 10,000 /and mines shrapnel Mk.I/L were produced at the Kingston works.
.Before the company itself began to manufacture complete Tanks, it undertoOk, sometimes for the M.O.S. and at others by direct contract with Manufacturers,the building of individual Tank parts or complete Tank. units, often carrying out considerable development work on these. For example,. it has suppliedjut over 2,000 complete final drives for the Valentine, and 1,142 Wilson steering units for Cruiser Tanks; this also formed, part of the final drive used on the Covenanter and Crusader. At the request of Vauxhall Motors, Ltd., the Leyland company built 1,600 final-drive units for the Churchill• Tank, and in this connection it was able to effect a big improvement. Sprockets were originally profile machined and then hardened, which, with the plant then available, 'took nearly an hour per tooth. Leyland's experience in flame cutting and hardening proved so successful that the job was reduced to under a minute per tooth.
Towards the end of 1941 the Kingston works began , the production of the well-known powered mountings traverse gear assemblies, a long name for the /mit hydraulically controlling the rotation of the turret and the traversing of the gun. It built 3,000 of these. Another big task was the production of nearly 6,000 Merritt-Brown gearboxes, each of which gives five speeds forward and reverse, and includes the steering mechanism for the tracks.
Power Units for Many Essential Services The company has built over 25,000 petrol and oil engines, ranging from the " Light-Six " to high-powered Tanks engines with 12 cylinders. Also produced was the well-known 8.6-litre oil engine, which was the power unit of many early war-time buses and lorries and the Hippo Mk. I. It was later used for the Double " sweep (to combat magnetic mines), and for a nUmber of war-time fire-escape chassis. The " Light-Six " and four-cylindered T-type petrol engines were also pre-war types, the former being used in the Lynx g.s. lorry and in the 700 g.p.m. Home Office fire pumps. The latter was used exclusively for the Retriever military lorries. The 139 h.p. six-oylindered petrol unit was employed for the 1,100 g.p.m. Home Office pump.
The most recent 100 h.p. six-cylindered oil engine follows in its design that of the " L " engine, on which power unit that of the Matilda Tank viras based. It was produced for the Hippo Mk. II lorry, and has proved the most economical power unit which the company has ever designed. It is being embodied in the double-deck buses now being built for the immediate post-war programme.
We have just referred to the " L " oil engine'. This was originally for single-deck buses, but was modified so that two engines could be coupled together to give an output of 190 h.p. It became the standard power unit of the Matilda, and 6,888 engines of this type came from the works.
Another notable type of power unit was the 12-cY1inriered flat model, known as the D.A.V. Built to the design of Henry Meadows, Ltd.. some 718 of these were produced for the Covenanter Tank.
Self-contained pumping units for the Home Office were built in two designs, and, by 1942, 679 of the 700 g.p.rii. type and 156 of the 1,100 g.p.in. type had come from the .Chorley works.
Another interesting item was the manufacture of an • aero-engine mounting unit for Bristol aircraft. As a result of the closing down of the passenger-vehicle bodyworks, a number of employees skilled in sheet-metal work was freed, and a contract for 1,000 units was undertaken. By VE-Day, some 0,000 units had been completed. The production of wheeled vehicles was by no means neglected. The company has built military vehicles since 1912 and supplied over 6,000 of the heavy type in the war of 1914-18. In the present war it has turned out over 9,000 military lorries, in addition to 2,300 buses and civilian-type goods vehicles. All this, however, practically ceased towards the latter part of 1942, for the whole of 1943 and most of 1944, when not a single wheeled vehicle could be made, the company's efforts being concentrated on Tanks.
One particularly rapid job was the production of 250 serni-armoured vehicles for aerodrome defence, asked for by Admiral Sir E. R. Evans. A suitable vehicle was designed and approved, delivery starting within 10 days, the foundation being the Retriever chassis.
The Hippo Mk. I., to which reference has already been made, was intended for heavy road-convoy work, and many lorries of this model saw service in the North African campaign. The Hippo Mk. II started in production towards the end of • the third quarter of 1944. This had been designed about a year before to meet the expected needs of our Invasion Forces. Designed for heavy convoy work, it carries 10 tons while hauling 5 tons on a trailer.
One exhibit which made a particular, appeal was that Of.. instructional literature. For each wheeled vehicle three books are provided—a driver's handbook, a service manual and a spare-parts list. In the case of the armoured fighting vehicles, there are two—the service instruction book, which is divided into two parts; the-first giving driving instructions and adjustments for the driver and crew, the second for Tank Schools and Train. ing Regiments, showing "how it works." The second book is a fully illustrated spare-parts list.
We hope later to be able to give some illustrations of the various products and, possibly, of the dernonstrations, but photographs were not available in time.