Amalgamated Roadstone Corporation (Eastern) Ltd.
Page 62
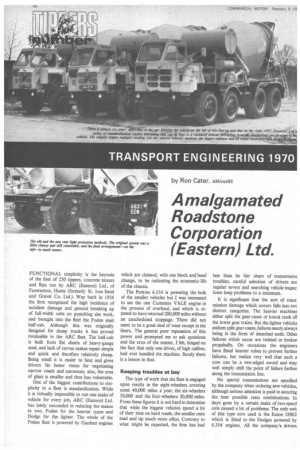
Page 63
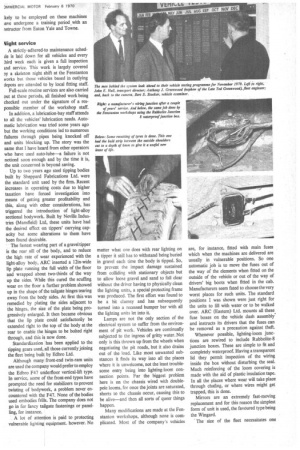
Page 64
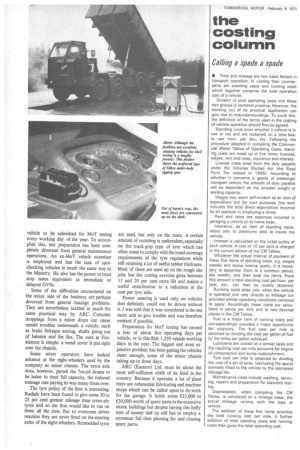
If you've noticed an error in this article please click here to report it so we can fix it.
by Ron Cater, AMInstBE FUNCTIONAL simplicity is the keynote of the fleet of 250 tippers, concrete mixers and flats run by ARC (Eastern) Ltd., of • Fenstanton, Hunts (formerly St. Ives Sand and Gravel Co. Ltd.). Way back in 1956 the firm recognized the high incidence of accident damage and general breaking up of full-width cabs on punishing site work, and brought into the fleet the Foden steel half-cab. Although this was originally designed for dump trucks it has proved invaluable in the ARC fleet. The half-cab is built from flat sheets of heavy-gauge • steel, and lack of curves makes repair simple and quick and therefore relatively cheap. Being small it is easier to heat and gives drivers far better vision for negotiating narrow roads and entrances; also, the area of glass is smaller and thus less vulnerable.
One of the biggest contributions to simplicity in a fleet is standardization. While it is virtually impossible to run one make of vehicle for every job, ARC (Eastern) Ltd. has lately succeeded in reducing the makes to two, Foden for the heavier types and Dodge for the lighter. The whole of the Foden fleet is powered by Gardner engines which are claimed, with one block and head change, to be outlasting the economic life of the chassis.
The Perkins 6.354 is powering the bulk of the smaller vehicles but I was interested to see the one Cummins VALE engine in the process of overhaul, and which is reputed to have returned 200,000 miles without an unscheduled stoppage. There did not seem to be a great deal of wear except in the liners. The general poor reputation of this power unit prompted me to ask questions and the crux of the matter, I felt, hinged on the fact that only one driver, of high calibre, had ever handled the machine. Surely there is a lesson in that.
Keeping troubles at bay The type of work that the fleet is engaged upon results in the eight-wheelers covering some 40,000 miles a year, the six-wheelers 30,000 and the four-wheelers 20,000 miles. From these figures it is not hard to determine that while the biggest vehicles spend a lot of their time on hard roads, the smaller ones load and tip much more often. Contrary to what might be expected, the firm has had less than its fair share of transmissior troubles; careful selection of drivers an regular severe and searching vehicle inspec tions keep problems to a minimum.
It is significant that the sort of trans mission damage which occurs falls into twc distinct categories. The heavier machines either split the gear-cases or knock teeth ofl the lower gear trains. But the lighter vehicles seldom split gear-cases, failures nearly always being in the form of detached teeth. Other failures which occur are twisted or broken propshafts. On occasions the engineers have fitted heavier tubes to prevent further failures, but realize very well that such a cure can be a two-edged sword and may well simply shift the point of failure farther along the transmission line.
No special transmissions are specified by the company when ordering new vehicles, although serious attention is paid to securing the best possible ratio combinations. In days gone by a certain make of two-speed axle caused a lot of problems. The only unit of this type now used is the Eaton 18802 which is fitted to the Dodges powered by 6.354 engines. All the company's drivers ikely to be employed on these machines Lave undergone a training period with an nstructor from Eaton Yale and Towne.
Might service
A strictly-adhered-to maintenance sehed is laid down for all vehicles and every third week each is given a full inspection Ind service. This work is largely covered by a skeleton night shift at the Fenstanton works but those vehicles based in outlying depots are attended to by local fitting staff. Full-scale routine services are also carried out at these periods, all finished work being checked out under the signature of a responsible member of the workshop staff. In addition, a lubrication-bay staff attends to all the vehicles' lubrication needs. Automatic lubrication was tried some years ago but the working conditions led to numerous failures through pipes being knocked off and units blocking up. The story was the same that I have heard from other operators who have used auto-lube—a failure is not noticed soon enough and by the time it is, the unit concerned is beyond saving. Up to two years ago steel tipping bodies built by Sheppard Fabrications Ltd. were the standard unit used by the firm. Recent increases in operating costs due to higher taxation have forced investigation into means of getting greater profitability and this, along with other considerations, has triggered the introduction of light-alloy sectional bodywork. Built by Neville Industries (Mansfield) Ltd, these units have had the desired effect on tippers' carrying capacity but some alterations to them have been found desirable.
The fastest wearing part of a gravel tipper is the rear sill of the body, and to reduce the high rate of wear experienced with the light-alloy body, ARC inserted a 12in-wide lip plate running the full width of the floor and wrapped about two-thirds of the way up the sides. While this cured the scuffing wear on the floor a further problem showed up in the shape of the tailgate hinges tearing away from the body sides. At first this was remedied by plating the sides adjacent to the hinges, the size of the plate being progressively enlarged. It then became obvious that the lip plate could satisfactorily be extended right to the top of the body at the rear to enable the hinges to be bolted right through, and this is now done.
Standardization has been applied to the tipping gears used, all those currently joining the fleet being built by Edbro Ltd.
Although many front-end twin-ram units are used the company would prefer to employ the Edbro F47 underfloor vertical-lift type. In service, some of the front-end types have prompted the need for stabilizers to prevent twisting of bodywork, a problem never encountered with the F47. None of the bodies used embodies frills. The company does not go in for fancy tailgate fastenings or panelling, for instance.
A lot of attention is paid to protecting vulnerable lighting equipment. however. No matter what one does with rear lighting on a tipper it still has to withstand being buried in gravel each time the body is tipped. So, to prevent the impact damage sustained from colliding with stationary objects but to allow loose gravel and sand to fall clear without the driver having to physically clean the lighting units, a special protecting frame was produced. The first effort was found to be a bit clumsy and has subsequently turned into a recessed bumper bar with all the lighting units let into it.
Lamps are not the only section of the electrical system to suffer from the environment of pit work. Vehicles are continually subjected to the ingress of gritty water. Not only is this thrown up from the wheels when negotiating the pit roads, but it also drains out of the load. Like most unwanted substances it finds its way into all the places where it is unwelcome, not the least troublesome entry being into lighting-loom connection points. Far the biggest problem here is on the chassis wired with doublepole looms, for once the joints are saturated, shorts to the chassis occur, causing this to be alive—and then all sorts of queer things happen. Many modifications are made at the Fenstanton workshops, although none is complicated. Most of the company's vehicles are, for instance, fitted with main fuses which when the machines are delivered are usually in vulnerable positions. So one automatic job is to move the fuses out of the way of the elements when fitted on the outside of the vehicle or out of the way of drivers' big boots when fitted in the cab.
Manufacturers seem fated to choose the very worst places for such units. The standard positions I was shown were just right for the units to fill with water or to be walked over. ARC (Eastern) Ltd. mounts all these fuse boxes on the vehicle dash assembly and instructs its drivers that the fuses can be removed as a precaution against theft. Whenever possible, lighting-loom junctions are rewired to include Rubbolite-8 junction boxes. These are simple to fit and completely waterproof. Having a transparent lid they permit inspection of the wiring inside the box without disturbing the seal.
Much reinforcing of the loom covering is made with the aid of plastic insulation tape.
In all the places where wear will take place through chafing, or where wires might get trapped, this is done. Mirrors are an extremely fast-moving replacement and for this reason the simplest form of unit is used, the favoured type being the Wingard.
The size of the fleet necessitates one vehicle to be submitted for MoT testing every working day of the year. To accomplish this, test preparation has been completely divorced from general maintenance operations. An ex-MoT vehicle examiner is employed and has the task of spotchecking vehicles in much the same way as the Ministry. He also has the power to issue stop notes equivalent to immediate or delayed GV9s.
Some of the difficulties encountered on the mixer side of the business are perhaps divorced from general haulage problems. They are nevertheless tackled in much the same practical way by ARC. Concrete droppings from a mixer drum can cause untold troubles underneath a vehicle, such as brake linkages seizing, shafts going out of balance and the like. The cure at Fenstanton is simple: a metal cover is put right over the chassis.
Some mixer operators have looked askance at the eight-wheelers used by the company as mixer chassis. The extra axle does, however, permit the 7cu.yd drums to be laden to their full capacity, the reduced tonnage rate paying its way many times over.
The tyre policy of the firm is interesting. Radials have been found to give some 20 to 25 per cent greater mileage than cross-ply tyres and so the firm would like to run on these all the time. But to overcome driver reaction they are never fitted on the steering axles of the eight-wheelers. Remoulded tyres are used, but only on the rears. A certain amount of recutting is undertaken, especially on the track-grip type of tyre which can often cease to comply with the tread coverage requirements of the tyre regulations while still retaining a lot of useful rubber thickness. Most of these are used up on the rough site jobs but the cutting exercise gives between 15 and 20 per cent extra life and makes a useful contribution to a reduction in the cost per tyre mile.
Power steering is used only on, vehicles that definitely could not be driven without it. I was told that it was considered to be one more unit to give trouble and was therefore omitted if possible.
Preparation for MoT testing has caused a loss of about five operating days per vehicle, or in this fleet 1,250 vehicle working days in the year. The biggest and most expensive problem has been getting the vehicles clean enough, some of the mixer chassis taking up to three days.
ARC (Eastern) Ltd. must be about the most self-sufficient outfit of its kind in the country. Because it operates a lot of plant there are substantial fabricating and machine shops which can be called upon to do work for the garage. It holds some £25,000 to £30,000-worth of spare parts in the extensive stores buildings but despite having this hefty sum of money tied up still has to employ a storeman full time phoning for and chasing spare parts.