road and workshop
Page 45
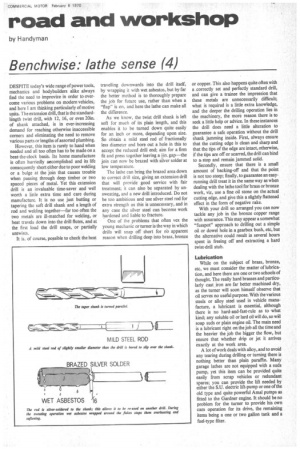
If you've noticed an error in this article please click here to report it so we can fix it.
by Handyman
Benchwise: lathe sense (4)
DESPITE today's wide range of power tools, mechanics and bodybuilders alike always find the need to improvize in order to overcome various problems on modern vehicles, and here I am thinking particularly of motive units. The extension drill, that is the standardlength twist drill, with 12, 16, or even 20in. of shank attached, is in ever-increasing demand for reaching otherwise inaccessible corners and eliminating the need to remove various parts or lengths of assorted plumbing.
However, this item is rarely to hand when needed and all too often has to be made on a beat-the-clock basis. Its home manufacture is often hurriedly accomplished and its life consequently short either due to poor welding or a bulge at the join that causes trouble when passing through deep timber or two spaced pieces of metal. Yet this extension drill is an invaluable time-saver and well worth a little extra time and care during manufacture. It is no use just butting or tapering the soft drill shank and a length of rod and welding together—far too often the two metals are ill-matched for welding, or heat travels down into the drill flutes, and at the first load the drill snaps, or partially untwists.
It is, of course, possible to check the heat travelling downwards into the drill itself, by wrapping it with wet asbestos, but by far the better method is to thoroughly prepare the job for future use, rather than when a "flap" is on, and here the lathe can make all the difference.
As we know, the twist drill shank is left soft for much of its plain length, and this enables it to be turned down quite easily for an inch or more, depending upon size. So obtain a mild steel rod of fractionally less diameter and bore out a hole in this to accept the reduced drill end; aim for a firm fit and press together leaving a ,*in. gap—the join can now be brazed with silver solder at low temperature.
The lathe can bring the brazed area down to correct drill size, giving an extension drill that will provide good service with fair treatment; it can also be separated by unsweating, and a new drill introduced. Do not be too ambitious and use silver steel rod for extra strength as this is unnecessary, and in any case the silver steel can become work hardened and liable to fracture.
One of the problems that often vex the young mechanic or turner is the way in which drills will snap off short for no apparent reason when drilling deep into brass, bronze
or copper. This also happens quite often with a correctly set and perfectly standard drill, and can give a trainee the impression that these metals are unnecessarily difficult; what is required is a little extra knowledge, and the deeper the drilling operation lies in the machinery, the more reason there is to seek a little help or advice. In these instances the drill does need a little alteration to guarantee a safe operation without the drill shank jamming inside. First, always ensure that the cutting edge is clean and sharp and that the tips of the edge are intact, otherwise, if the tips are off or scarred, the drill can bind to is stop and remain jammed solid.
Secondly, ensure that there is a small amount of backing-off and that the point is not too steep; finally, to guarantee an easyrunning drill treat it in the same way as when dealing with the lathe tool for brass or bronze work, viz, use a fine oil stone on the actual cutting edge, and give this a slightly flattened effect in the form of negative rake.
With your drill so arranged you can now tackle any job in the bronze copper range with assurance. This may appear a somewhat "fusspot" approach to drilling out a simple oil or dowel hole in a gearbox bush, etc, but the alternative could result in several hours spent in freeing off and extracting a hard twist-drill stub.
Lubrication While on the subject of brass, bronze, etc, we must consider the matter of lubrication, and here there are one or two schools of thought. The really hard brasses and particularly cast iron are far better machined dry, as the turner will soon himself observe that oil serves no useful purpose. With the various steels or alloy steel used in vehicle manufacture, a lubricant is essential, although there is no hard-and-fast-rule as to what kind; any soluble oil or lard oil will do, so will soap suds or plain engine oil. The main need is a lubricant right on the job all the time and the heavier the job the bigger the flow, but ensure that whether drip or jet it arrives exactly at the work area.
A lot of work deals with alloy, and to avoid any tearing during drilling or turning there is nothing better than plain paraffin. Many garage lathes are not equipped with a suds pump, yet this item can be provided quite easily from scrap vehicles or redundant spares; you can provide the lift needed by either the S.U. electric lift-pump or one of the old type and quite powerful Amal pumps as fitted to the Gardner engine. It should be no problem for the turner to provide his own cam operation for its drive, the remaining items being a one or two gallon tank and a fuel-type filter.