Standard Maintenance Schedules
Page 84
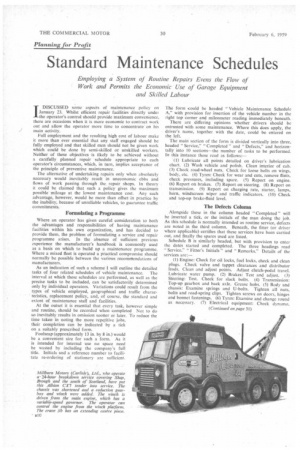
Page 87
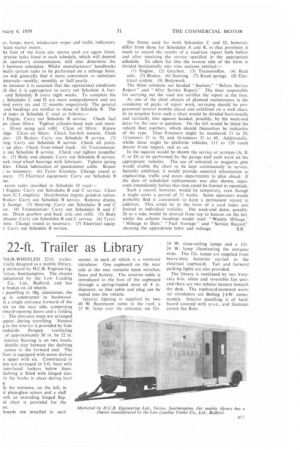
If you've noticed an error in this article please click here to report it so we can fix it.
Employing a System of Routine Repairs Evens the Flow of Work and Permits the Economic Use of Garage Equipment and Skilled Labour
IDISCUSSED some aspects of maintenance policy on January 23. Whilst efficient repair facilities directly under the operator's control should provide maximum convenience, there are occasions when it is more economic to contract work out arid allow the operator more time to concentrate on his main activity.
Full employment and the resulting high cost of labour make it more than ever essential that any staff engaged should be fully employed and that skilled men should not be given work which could be done by semi-skilled or unskilled workers. Neither of these objectives is likely to be achieved without a carefully planned repair schedule appropriate to each operator's circumstances, which, in turn, implies acceptance of the principle of preventive maintenance.
The alternative of undertaking repairs only when absolutely necessary would inevitably result in uneconomic ebbs and flows of work passing through the repair shops. In theory it could be claimed that such a policy gives the maximum possible mileage at the lowest maintenance cost. Any such advantage, however, would be more than offset in practice by the inability, because of unreliable vehicles, to guarantee traffic commitments.
Formulating a Programme
Where an operator has given careful consideration to both the advantages and responsibilities of having maintenance facilities within his own organization, and has decided to provide them, the problem of formulating a service and repair programme arises. In the absence of sufficient previous experience the manufacturer's handbook is commonly used as a basis on which to build up a maintenance programme. Where a mixed fleet is operated a practical compromise should normally be possible between the various recommendations of manufacturers.
As an indication of such a scheme 1 will outline the detailed tasks of four related schedules of vehicle maintenance. The interval at which these schedules are performed, as well as the precise tasks to be included, can be satisfactorily determined only by individual operators. Variations could result from the types of vehicle employed, geographical and traffic characteristics, replacement policy, and, of course, the standard and extent of maintenance staff and facilities.
At the outset it is essential that every task, however simple and routine, should be recorded when completed Not to do so inevitably results in omission sooner or later. To reduce the time taken in noting the more repetitive jobs, their completion can be indicated by a tick on a suitably prescribed form.
Foolscap (approximately 13 in. by 8 in.) would be a convenient size for such a form. As it is intended for internal use no space need be wasted by including the company's full title. Initials and a reference number to facilitate re-ordering of stationery are sufficient.
The form could be headed "Vehicle Maintenance Schedule A," with provision for insertion of the vehicle number in the right top corner and mileometer reading immediately beneath.
There are differing opinions whether drivers should be entrusted with some maintenance. Where this does apply, the driver's name, together with the date, could be entered on the left.
The main section of the form is divided vertically into three, headed "Service," "Completed' and "Defects," and horizontally into 10 sections—the number of tasks to be performed. In this instance these read as follows:—
(I) Lubricate all points detailed on driver's lubrication chart. (2) Wash vehicle and polish. Clean interior of cab. (3) Check road-wheel nuts. Check for loose bolts on wings, body, etc. (4) Tyres: Check for wear and cuts, remove flints, check pressures, including spare. (5) Report on engine. (6) Report on brakes. (7) Report on steering. (8) Report on transmission. (9) Report on charging rate, starter, lamps, horn, windscreen wiper and traffic indicators. (10) Check and top-up brake-fluid level.
The Defects Column
Alongside these in the column headed " Completed " will be inserted a tick, or the initials of the man doing the job. As this schedule is normally intended as routine service, defects are noted in the third column. Beneath, the fitter (or driver where applicable) certifies that these services have been carried out, and finally the spares used are listed.
Schedule B is similarly headed, but with provision to enter the dates started and completed. The three headings read "Service," "Fitter's Initials" and "Remarks." Details of the services are:—
(I) Engine: Check for oil locks, fuel locks, check and clean plugs. Check valve and tappet clearances and distributor leads. Clean and adjust points. Adjust clutch-pedal travel. Lubricate water pump. (2) Brakes: Test and adjust. (3) Steering: Test. Check for slack bolts. (4) Transmission: Top-up gearbox and back axle. Grease hubs. (5) Body and chassis: Examine springs and U-bolts. Tighten all nuts, bolts and road-spring clips. Tighten screws on doors, hinges and bonnet fastenings. (6) Tyres: Examine and change round as necessary. (7) Electrical equipment: Check dynamo.
cr, lamps, horn, windscreen wiper and traffic indicators. -icate starter motoi.
he foot of the form any spares used are again listed. precise tasks listed in each schedule, which will depend eh operator's circumstances, will also determine the I between schedules. Whilst manufacturers' handbooks )ecify certain tasks to be performed on a mileage basis. 3rs will generally find it more convenient to substitute intervals—weekly, monthly or half-yearly.
is instance it is assumed that the operational conditions eh that it is appropriate to carry out Schedule A fort' and Schedule B every eight weeks. To complete the Schedules C and D are more comprehensive and are ned every six and 12 months respectively The general and headings are similiar to those of Schedule B. The tasks in Schedule C read as follows:—
) Engine. Carry out Schedule B service. Check fuel ps, clean filters. Tighten cylinder-head nuts and mania. Drain sump and refill. Clean oil filters. Renew .idge. Clean air filters. Check fan-belt tension. Flush ator. (2) Brakes: Carry out Schedule B service. (3) ring: Carry out Schedule B service. Check all joints. : up play. Check front-wheel track. (4) Transmission: y out Schedule B service. Check and tighten propeller ts. (5) Body and chassis: Carry out Schedule B service. )ack road-wheel bearings with lubricant. Tighten spring kles. Check lubrication of speedometer cable. Repair
as necessary. (6) Tyres: Examine. Change round as ssary. (7) Electrical equipment: Carry out Schedule B ice.
seven tasks specified in Schedule D read:— ) Engine: Carry out Schedules B and C service. Clean :tors (C.I. engines). Decarbonize engine, grind-in valves. Brakes: Carry out Schedule B service. Remove drums, k facings. (3) Steering: Carry out Schedules B and C ice. (4) Transmission: Carry out Schedules B and C ice. Drain gearbox and back axle and refill. (5) Body chassis: Carry out Schedules B and C service. (6) Tyres: nine. Change round as necessary. (7) Electrical equipt: Carry out Schedule B service.
The forms used for both Schedules C and D, however, differ from those for Schedules A and B, in that provision is made to record the results of a road-test report both before and after receiving the service specified in the appropriate schedule. To allow for this the reverse side of the form is divided horizontally into nine sections entitled:—
(I) Engine. (2) Gearbox. (3) Transmission. (4) Back axle. (5) Brakes. (6) Steering. (7) Road springs. (8) Electrical system. (9) Bodywork.
The three columns are headed "Section," " Before Service Report and " After Service Report." The titter responsible for carrying out the road test certifies the report at the foot.
As one of the chief objects of planned maintenance is the avoidance of peaks of repair work, servicing should be programmed several months ahead and exhibited on a wall chart. In its simplest form such a chart would be divided horizontally and vertically into squares headed, possibly, by the week-end dates for the year in question. On the left would be listed the vehicle fleet numbers, which should themselves be indicative of the type. Thus 8-tonners might be numbered 11 to 20. 12-tonners 21 to 30, and 16-tonners 31 to 40. Additionally. whilst these might be platform vehicles, 111 to 120 could denote 8-ton tippers, and so on.
In the squares would be shown the service, or services (A, B. C or D) to be performed by the garage staff each week on the appropriate vehicles. The use of coloured or magnetic pins would enable the chart to be kept continuously in service. Suitably exhibited, it would provide essential information to engineering, traffic and stores departments to plan ahead. If the date of scheduled replacements was also shown, repair costs immediately before that date could be limited to essentials.
Such a record, however, would be temporary, even though it might cover a period of 52 weeks. Some operators would probably find it convenient to keep a permanent record in addition. This could be in the form of a card index and limited to individual vehicles. The week-end dates, possibl 26 to a side, would be entered from top to bottom on the left. whilst the column headings would read: "Weekly Mileage." Mileage to Date." "Fuel Average" and "Service Record."
showing the appropriate letter and mileage. S.B.