'Overkill': an all to familiar pattern...
Page 17
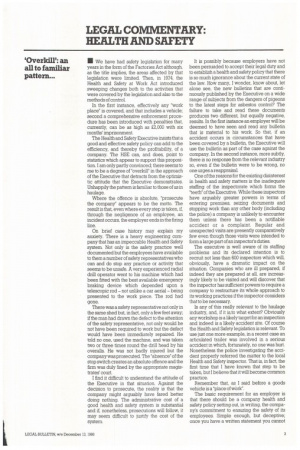
Page 18

If you've noticed an error in this article please click here to report it so we can fix it.
• We have had safety legislation for many years in the form of the Factories Act although, as the title implies, the areas affected by that legislation were limited. Then, in 1974, the Health and Safety at Work Act introduced sweeping changes both to the activities that were covered by the legislation and also to the methods of control.
In the first instance, effectively any "work place" is covered, and that includes a vehicle; second a comprehensive enforcement procedure has been introduced with penalties that, currently, can be as high as £2,000 with six months' imprisonment, The Health and Safety Executive insists that a good and effective safety policy can add to the efficiency, and thereby the profitability, of a company. The HSE can, and does, point to statistics which appear to support this proposition. I am only partly convinced; there seems to me to be a degree of "overkill" in the approach of the Executive that detracts from the optimistic attitude that the Executive demonstrates. Unhappily the pattern is familiar to those of us in haulage.
Where the offence is absolute, "prosecute the company" appears to be the motto. The result is that even where every step is taken, if, through the negligence of an employee, an incident occurs, the employer ends in the firing line.
On brief case history may explain my anxiety. There is a heavy engineering company that has an impeccable Health and Safety system. Not only is the safety practice well documented but the employees have available to them a number of safety representatives who can and do stop any practice or activity that seems to be unsafe. A very experienced radial drill operator went to his machine which had been fitted with the best available emergency braking device which depended upon a telescopic rod not unlike a car aerial being presented to the work piece, The rod had gone.
There was a safety representative not only in the same shed but, in fact, only a few feet away; if the man had drawn the defect to the attention of the safety representative, not only would he not have been required to work but the defect would have been immediately repaired. He told no one, used the machine, and was taken two or three times round the drill head by his overalls. He was not badly injured but the company was prosecuted. The 'absence" of the stop switch creates an absolute offence and the firm was duly fined by the appropriate magistrates' court.
I find it difficult to understand the attitude of the Executive in that situation. Against the decision to prosecute, the reality is that the company might arguably have fared better doing nothing. The administrative cost of a good health and safety system is substantial and if, nonetheless, prosecutions will follow, it may seem difficult to justify the cost of the system, It is possibly because employers have not been persuaded to accept their legal duty and to establish a health and safety policy that there is so much ignorance about the current state of the law. How many, I wonder, know about, let alone see, the new bulletins that are continuously published by the Executive on a wide range of subjects from the dangers of pigeons to the latest steps for asbestos control? The failure to take and read these documents produces two different, but equally negative, results. In the first instance an employer will be deemed to have seen and read any bulletin that is material to his work. So that, if an accident occurs in circumstances that have been covered by a bulletin, the Executive will use the bulletin as part of the case against the company. In the second instance, more subtly, there is no response from the relevant industry so, even if the bulletin were to be wrong, no one urges a reappraisal.
One of the reasons for the existing disinterest in health and safety matters is the inadequate staffing of the inspectorate which forms the "teeth" of the Executive. While these inspectors have arguably greater powers in terms of entering premises, seizing documents and stopping work than any other body (including the police) a company is unlikely to encounter them unless there has been a notifiable accident or a complaint. Regular and unexpected visits are presently comparatively few even though those visits were intended to form a large part of an inspector's duties.
The executive is well aware of its staffing problems and its declared intention is to recruit not less than 600 inspectors which will, obviously, have a dramatic impact on the situation Companies who are ill prepared, if indeed they are prepared at all, are increasingly likely to be visited and will discover that the inspector has sufficient powers to require a company to restructure its whole approach to its working practices if the inspector considers that to be necessary.
Is any of this really relevant to the haulage industry, and, if it is,to what extent? Obviously any workshop is a likely target for an inspection and indeed is a likely accident site. Of course the Health and Safety legislation is relevant To use just one more example, in a recent case an articulated trailer was involved in a serious accident in which, fortunately, no one was hurt. Nonetheless the police investigating the accident properly referred the matter to the local Health and Safety inspector. That is, in fact, the first time that I have known that step to be taken, but I believe that it will become common practice.
Remember that, as I said before a goods vehicle is a "place of work".
The basic requirement for an employer is that there should be a company health and safety policy setting out, in writing, the company's commitment to ensuring the safety of its employees. Simple enough, but deceptive; once you have a written statement you cannot deny your knowledge of the extent of your responsibility. In my view, if you have determined to issue a policy or indeed been directed to issue one then you must go further and supplement the policy by additional documentation that is appropriate to the needs of your company. At the very least you should have a Health and Safety handbook to be handed to employees giving both general and specific advice about safety practice in the context of their employment.
Finally, to repeat a second point, I suspect that my views will be unwelcome if only because of the cost of the exercise. Nonetheless, health and safety is here to stay and if you have not thought about it you should start now. by Jonathan Lawton