Lightweight a must for tipper bodies
Page 72
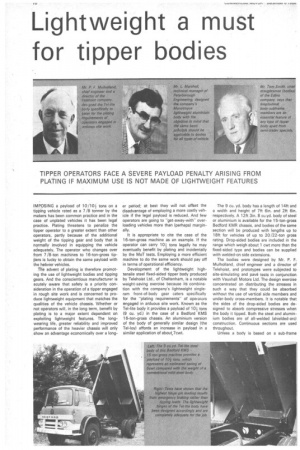
Page 73
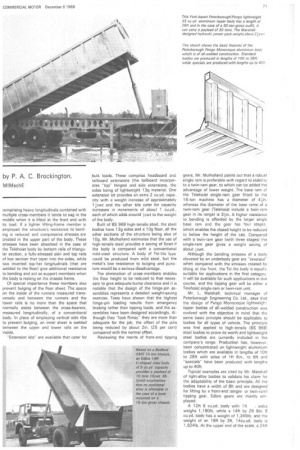
Page 74
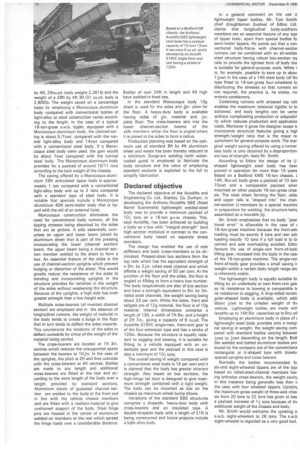
If you've noticed an error in this article please click here to report it so we can fix it.
TIPPER OPERATORS FACE A SEVERE PAYLOAD PENALTY ARISING FROM PLATING IF MAXIMUM USE IS NOT MADE OF LIGHTWEIGHT FEATURES by P. A. C. Brockington,
MIMechE
IMPOSING a payload of 10/10+ tons on a tipping vehicle rated as a 7/8 tonner by the makers has been common practice and in the case of unplated vehicles it has been legal practice. Plating threatens to penalize the tipper operator to a greater extent than other operators, partly because of the additional weight of the tipping gear and body that is normally involved in equipping the vehicle adequately. The operator who changes over from 7/8-ton machines to 16-ton-gross tippers is lucky to obtain the same payload with the hetwier vehicles.
The advent of plating is therefore promoting the use of lightweight bodies and tipping gears. And the conscientious manufacturer is acutely aware that safety is a priority consideration in the operation of a tipper engaged in rough site work and is concerned to produce lightweight equipment that matches the qualities of the vehicle chassis. Whether or not operators will, in the long term, benefit by plating is to a major extent dependent on exploiting lightweight features, The longwearing life, greater reliability and improved performance of the heavier chassis will only show an advantage economically over a long
er period; at best they will not offset the disadvantage of employing a more costly vehicle if the legal payload is reduced. And few operators are going to "get-away-with" overloading vehicles more than (perhaps) marginally.
It is appropriate to cite the case of the 16-ton-gross machine as an example. If the operator can carry 10+ tons legally he may eventually benefit by plating and incidentally by the MoT tests. Employing a more efficient machine to do the same work should pay off in terms of operational efficiency.
Development of the lightweight hightensile steel fixed-sided tipper body produced by Telehoist Ltd., of Cheltenham, is a notable weight-saving exercise because its combination with the company's lightweight singleram front-of-body gear caters specifically for the "plating requirements" of operators engaged in arduous site work. Known as the Tel-lite body it provides a payload of 104 tons (9 cu. yd.) in the case of a Bedford KMS 16-ton-gross chassis. An aluminium version of the body of generally similar design (the Tel-by) affords an increase in payload in a similar application of about7cwt. The 9 cu. yd. body has a length of 14ft and a width and height of 7ft 6in. and 2ft 6in. respectively. A 1 2ft 3in. 8 cthyd. body of steel or aluminium is available for the 15-ton-gross Bedford KM R chassis, and bodies of the same section will be produced with lengths up to 18ft for vehicles of up to 20/22-ton gross rating. Drop-sided bodies are included in the range which weigh about 1 cwt more than the fixed-sided type and bodies can be supplied with welded-on side extensions.
The bodies were designed by Mr. P. F. Mulholland, chief engineer and a director of Telehoist, and prototypes were subjected to site-simulating and pave tests in conjunction. with Vauxhall Motors Ltd. The design exercise concentrated on distributing the stresses in such a way that they could be absorbed without the use of vertical side members and under-body cross-members. It is notable that the sides of the drop-sided bodies are designed to absorb compressive stresses when the body it tipped. Both the steel and aluminium bodies are of all-welded (shielded-arc) construction. Continuous sections are used throughout.
Unless a body is based on a sub-frame 3omprising heavy longitudinals combined with multiple cross-members it tends to sag in the middle when it is lifted at the front end with its load. If a lighter lifting-frame member is employed the structure's resistance to bending is reduced and compressive stresses are created in the upper part of the body, These stresses have been absorbed in the case of the Telehoist body by bottom rails of triangular section, a fully-stressed skin and top rails of box section that taper into the sides, while two inverted top-hat longitudinals (that are welded to the floor) give additional resistance to bending and act as support members when the body is resting on the chassis frame.
Of special importance these members also prevent bulging of the floor sheet. The space on the inside of the runners measured transversely and between the runners and the lower rails is no more than the space that normally exists between the cross-bearers, measured longitudinally, of a conventional body. In place of employing vertical side ribs to prevent bulging, an inner sheet is welded between the upper and lower rails on the inside.
"Extension kits" are available that cater for
bulk loads. These comprise headboard and tailboard extensions (the tailboard incorporates "top" hinges) and side extensions, the sides being of lightweight 13g material. One extension kit provides an extra 2 cu.yd. capacity with a weight increase of approximately 1:3icwt and the other kits cater for capacity increases in increments of about 1 cu.yd., each of which adds around Icwt to the weight of the body.
Built of BS 968 high-tensile steel, the steel bodies have 13g sides and a lOg floor, all the other sections of the structure being also of 10g. Mr. Mulholland estimates that the use of high-tensile steel provides a saving of 5cwt if the body is compared with a conventional mild-steel structure. A body of Tel-lite type could be produced from mild steel, but the metal's low resistance to bulging and puncture would be a serious disadvantage.
The elimination of cross-members enables the floor height to be reduced to that necessary to give adequate bump clearance and it is notable that the design of the hinge-pin assemblies represents a detailed weight-saving exercise. Tests have shown that the highest hinge-pin loading results from emergency braking rather than tipping loads, and the assemblies have been designed accordingly. Although they "look flimsy" they are more than adequate for the job, the offset of the pins being reduced by about 2in. (25 per cent) compared with the normal offset.
Reviewing the merits of front-end tipping gears, Mr. Mulholland points out that a robust single ram is preferable with regard to stability to a twin-ram gear, to which can be added the advantage of lower weight. The base ram of the Telehoist single-ram gear fitted to the 16-ton machine has a diameter of whereas the diameter of the base rams of a twin-ram gear (Telehoist include a twin-ram
gear in its range) is A higher resistance to bending is afforded by the larger single base ram and the gear has four stages, ir-vhich enables the closed height to be reduced to below the height of the cab. Compared with a twin-ram gear (with three stages) the single-ram gear gives a weight .saving of about Icwt.
Although the bending stresses of a body elevated by an underbody gear are "reversed" when compared with the stresses created by lifting at the front. the Tel-lite body is equally suitable for applications in the first category. It will be available for such applications in due course, and the tipping gear will be either a Telehoist single-ram or twin-ram unit.
Mr. L. Marshall, technical manager of Peterborough Engineering Co. Ltd., says that the design of Pengo Monocoque lightweight tipper bodies of all-welded construction was evolved with the objective in mind that the same basic principle should be applicable to bodies for all types of vehicle. The principle was first applied to high-tensile IBS 968) steel bodies to prove its worth. and lightweight steel bodies are currently included in the company's range. Production has, however. been concentrated on lightweight aluminium bodies which are available in lengths of 10ft to 28ft with sides of 1ft 6in., to 6ft and "specials" have been produced. with lengths up to 40ft.
Typical examples are cited by Mr. Marshall of light-alloy bodies to validate his claim for the adaptability of the basic principle. All the bodies have a width of 8ft and are designed for lifting by a front-end (singleor twin-ram) tipping gear. Edbro gears are mainly employed.
A 12ft 8 cu.yd. body with 1ft . sides weighs 1,190Ib, while a 14ft by 2ft Bin. 9 cu.yd. body has a weight of 1 ,3451b, and the weight of an 18ft by 3ft, 14cu.yd. body is 1,6241b. At the upper end of the scale, a 24ft by 4ft, 26cu.yd. body weighs 2,361Ib and the weight of a 28ft by 4ft 30 /31 cu.yd. body is 2,6001b. The weight saved on a percentage basis by employing a Monocoque aluminium body compared with conventional bodies of light-alloy or steel construction varies according to the length. In the case of a typical 16-ton-gross s.w.b. tipper, equipped with a Monocoque aluminium body, the claimed saving is about 5/7cwt, compared with the normal light-alloy body and 14cwt compared with a conventional steel body. If a Monocoque steel body were used, the gain would be about 7cwt compared with the normal steel body. The Monocoque aluminium body provides for a payload of around 10/11 tons according to the kerb weight of the chassis.
The saving offered by a Monocoque aluminium 28ft articulated tipper body is approximately 1 ton compared with a conventional light-alloy body and up to 2 tons compared with a standard type of steel body. It is notable that specials include a Monocoque aluminium 40ft semi-trailer body that is tipped with the aid of an external hoist.
Monocoque construction eliminates the need for conventional body runners, all the tipping stresses being absorbed by the sides that act as girders. A side essentially comprises an upper and lower beam joined by aluminium sheet that is part of the pressing incorporating the lower (channel section) beam, the upper beam being a channel section member welded to the sheet to form a box. An essential feature of the sides is the use of channel-section uprights which prevent bulging or distortion of the sheet. This would greatly reduce the resistance of the sides to bending and incorporating uprights in the structure provides for variation in the weight of the sides without weakening the structure. Because of the uprights, a high side has even greater strength than a low-height side.
Multiple cross-bearers (of inverted channel section) are employed and in the absence of longitudinal runners, the weight of material in the body tends to create a bulge in the floor that in turn tends to deflect the sides inwards. This counteracts the tendency of the sides to deflect outwards by virtue of the weight of the material being carried.
The cross-bearers are located at lft 3in. centres which reduces the unsupported space between the bearers to 10,iin. In the case of the uprights, the pitch is 2ft and they coincide with the cross-bearers at 4ft centres. Bodies are made to any length and additional cross-bearers are fitted at the rear end according to the extra length of the body over a length provided by standard sections. Aluminium stools of gusseted channel section are welded to the body at the front end in line with the vehicle chassis members and are fitted with a resilient material to give cushioned support of the body. Steel hinge pins are housed in the centre of aluminium welded-on members at the rear which spread the hinge loads over a considerable distance. Bodies of over 24ft in length and 4ft high have welded-in fixed ties.
In the standard Monocoque body 10g sheet is used for the sides and din. plate for the floor. A heavy-duty body is available having sides of ain. material and lin. plate floor. The cross-bearers slot into the lower channel-section beams of the side members while the floor is angled where it is joined to the sides to form a radius.
Production planning was based on the optimum use of standard aft by 4ft aluminium sheet and waste has been thereby reduced to a minimum. Surge-arc welding with watercooled guns) is employed to fabricate the body structure and the value of employing standard sections is exploited to the full to simplify fabrication.
Declared objective
The declared objective of the Autolifts and Engineering Co. Ltd., Stanley, Co. Durham, in developing the Anthony/Autolifts SBS (Steel Barrel Scammells) lightweight welded-steel body was to provide a minimum payload of 10+ tons on a 16-ton g.v.w. chassis. This, says Autolifts, has been achieved by building a body as a box with "integral strength" (and high section modulus) in contrast to the conventional body based on separate stress members.
The design has enabled the use of side stiffeners and body cross-members to be eliminated. Pressed-steel box sections form the top rails which has the equivalent strength of a 5in. by 2+in. rolled steel channel and which affords a weight saving of 50 per cent. At the junction of the floor and the sides, the floor is angled at 45deg to form a heavy box number. The body lorigitudinals are also of box section and have a strength equivalent to 6in, by 3in. rolled steel channels, the weight saving being about 25 per cent. While the sides, front and tailgate are of 12g material, the floor is of lOg material. Internal dimensions comprise a length of 13ft, a width of 7ft 6in. and a height of 2ft 7in., giving a capacity of 9 cu.yd. The Autolifts S16FC single-ram, front-end gear is of the four-extension type and has a stroke of 120in. Because the structure is equally resistant to sagging and bowing, it is suitable for fitting to a vehicle equipped with an underbody gear and the payload in this case is also a minimum of 10q tons.
The overall saving in weight compared with a conventional steel body is 19 per cent and it is claimed that the body has greater inherent strength. Also based on box sections, the high-hinge tail door is designed to give maximum strength combined with a light weight. The body can be mounted as low on the chassis as maximum wheel bump allows.
Variations of the standard SBS structures comprise a dropside, heavy-duty body with cross-bearers and an insulated type. A double-dropside body with a length of 21 ft is being constructed and future projects include a light-alloy body. In a general comment on the use o lightweight tipper bodies, Mr. Tom Smith chief draughtsman (bodies} of Edbro Ltd. claims that longitudinal body-subframe members are an essential feature of any type of tipper body, apart from special bodies to semi-trailer tippers. He points out that a con ventional body-frame with channel-sectior runners can be combined with an all-weldec steel structure having robust box-section tot rails to provide the lightest form of body tha is suitable for general-purpose work. While i is, for example, possible to save up to abou licwt in the case of a 14ft steel body (of the type fitted to 16-ton-gross four-wheelers) b? distributing the stresses so that runners are not required, the practice is, he states, no entirely satisfactory.
Combining runners with stressed top rail: enables the maximum torsional rigidity to be achieved, and body lengths can be varlet without complicating production or adaptabil ity which reduces production and applicatior costs. Moreover it gives the designer scope te incorporate structural features giving a higt strength /weight ratio that is the major re quirement for general-purpose work. The mar gine] weight saving offered by using a runner less body is only obtained by a disproportion ate loss of strength, feels Mr. Smith.
According to Edbro the design of its U• shaped lightweight steel body has beer proved in operation for more than 15 years Based on a Bedford KMS 16-ton chassis, 14ft, 9cu.yd. body gives a payload of 10 ton! lOcwt and a comparable payload wher mounted on other popular 16-ton-gross chas. sis. The steel sheet forming the floor, side: and upper rails is "shaped into" the chan. nel-section U-members by a special machinf in preparation for welding, the structure beinc assembled on a movable jig.
Mr. Smith emphasizes that no body "posi tional error" is allowable in the case of 16-ton-gross machine because the front-axle loading must be exactly 6 tons and rear axle loading exactly 10 tons if a full load is to be carried and axle overloading avoided. Edbre favours the use of single-ram front-of-bod? lifting gear, recessed into the body in the case of the 16-ton-gross machine. The single-ran front-of-body gear provides a small saving it weight within a certain body length range ant is inherently stable.
The lightweight body is equally suitable fo lifting by an underbody or twin front-ram gea as its resistance to bowing is comparable ti its resistance to sagging. A drop-sided rectan gular-shaped body is available, which add: about Icwt to the unladen weight of the vehicle. Lightweight bodies are made wit] lengths up to 14ft 6in. capacities up to 9cu.yd
Employing an aluminium body in place of E lightweight steel body provides only a margi. nal saving in weight, the weight saving corn, pared with standard bodies varying betweer +cwt to icwt depending on the length. Botf the welded and bolted aluminium bodies pro duced by the company are of the conventiona rectangular or U-shaped type with closely spaced uprights and cross bearers.
Normally the bodies recommended fo six-and eight-wheeled tippers are of the type based on rolled-steel-channel members hay ing 'orthodox cross-bearers, the weight savint in this instance being 9enerally less than the case with four wheeled tippers. Upratint the maximum gross weight of three-axle chas sis from 20 tons to 22 tons has given at bes a payload increase of 11tons because of the additional weight of the chassis and body.
Mr. Smith would welcome the uprating o s.w.b. eight-wheelers to 26 tons. The s.w.b eight-wheeler is regarded as a very good tool.