THE HEART 01
Page 46
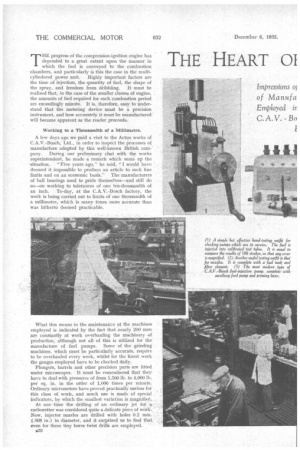
Page 47
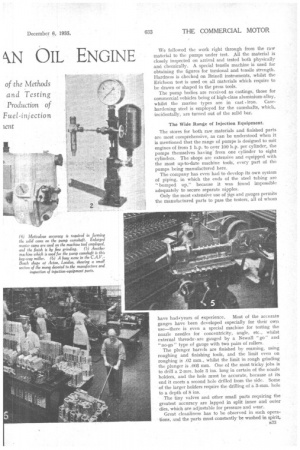
Page 48
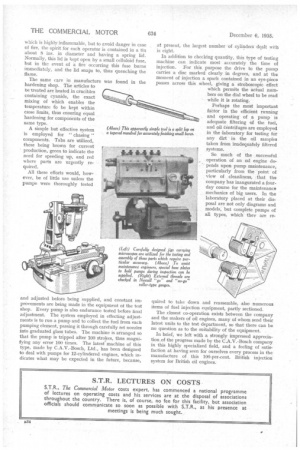
If you've noticed an error in this article please click here to report it so we can fix it.
kN OIL ENGINE THE progress of the compression-ignition engine has depended to a great extent upon the manner in which the fuel is conveyed to the combustion chambers, and particularly is this the case in the multicylindered power unit. Highly important factors are the time of injection, the quantity of fuel, the shape of the spray, and freedom from dribbling. It must be realized that, in the case of the smaller classes of engine, the amounts of fuel required for each combustion period are exceedingly minute. It is, therefore, easy to understand that the metering. device must be a precision instrument, and how accurately it must be manufactured will become apparent as the reader proceeds.
Working to a Thousandth of a Millimetre.
A few days ago we paid a visit to the Acton works of C.A.V.-Bosch, Ltd., in order to inspect the processes of manufacture adopted by this well-known British corn-. pany. During our preliminary chat with the works superintendent, he made a remark which sums up the situation. "Five years ago," he said, would have deemed it impossible to produce an article to such fine limits and on an economic basis." The manufacturers of ball bearings used to pride themselves—and still do so—on working to tolerances of one ten-thousandth of an inch. To-day, at the C.A.V.-Bosch factory, the work is being carried out to limits of one thousandth of a millimetre, which is many times more accurate than was hitherto deemed practicable.
What this means in the maintenance oi the machines employed is indicated by the fact that nearly 200 men are constantly at work overhauling the machinery of production, although not all of this is utilized for the manufacture of fuel pumps. Some of the grinding machines, which must be particularly accurate, require to be overhauled every week, whilst for the finest work the gauges employed have to be checked daily.
Plungers, barrels and other precision parts are fitted under microscopes. It must be remembered that they have to deal with pressures of from 1,500 lb. to 4,000 lb. per sq. in, in the order of 1,000 times per minute. Ordinary micrometers have proved practically useless for this class of work, and much use is made of special indicators, by which the smallest variation is magnified,.
At one time the drilling of an ordinary jet for a. carburetter was considered quite a...delicate piece of work., Now, injector nozzles are drilled with holes 0.2 mm. (.00$ in.) in diameter, and it surprised UB to find that. even for these tiny bores twist drills are employed.
142 We followed the work right through from the raw material to the pumps under test. All the material is closely inspected on arrival and tested both physically and chemically. A special tensile machine is used for obtaining the figures for torsional and tensile strength. Hardness is checked on Brinell instruments, whilst the Erichson test is used on all materials which require to be drawn or shaped in the press tools.
The pump bodies are received as castings, those for commercial vehicles being of high-class aluminium-alloy, whilst the marine types are in cast .iron. Casehardening steel is employed for the camshafts, which, incidentally, are turned out of the solid bar.
The Wide Range of Injection Equipment.
The stores for both raw materials and finished parts are most comprehensive, as can be understood when it is mentioned that the range of pumps is designed to suit engines of from 1 h.p. to over 100 h.p, per cylinder, the pumps themselves having' from one cylinder to eight cylinders. The shops are extensive and equipped with the most up-to-date• machine tools, every part of the pumps being manufactured here.
The company has even had to develop its own system of piping, in which the ends of the steel tubing are "bumped up," because it was found impossible adequately to secure separate nipples.
Only the most extensive use of jigs and gauges permits the manufactured parts to pass the testers, all of whom have hadiyears of experience. Most of the accurate gauges have been developed especially for their own use—there is even a special machine for testing the nozzle needles for concentricity, angle, etc., whilst external threads'-are gauged by a Newall "go" and "no-go" type of gauge with two pairs of rollers.
The plunger barrels are finished by reaming, using roughing and finishing tools, and the limit even on roughing is .02 mm., whilst the limit in rough grinding the plunger is .003 mm. One of the most tricky jobs is to drill a 2-mm. hole 3 ins, long in certain of the nozzle holders, and the hole must be accurate, because at its end it meets a second hole drilled from the side. Some of the larger holders require the drilling of a 3-mm. hole to a depth of _8 ins.
• The tiny valves and other small parts requiring the greatest accuracy are lapped in split inner and outer dies, which are adjustable for pressure and wear.
Great cleanliness has to be observed in such operations, and the parts must constantly be washed in spirit, 533
which is highly inflammable, but to avoid danger in case of fire, the spirit for each operator is contained in a tin about 8 ins, in diameter and having a spring lid. Normally, this lid is kept open by a small celluloid fuse, but in the event of a fire occurring this fuse burns immediately, and the lid snaps to, thus quenching the flame.
The same care in manufacture was found in the hardening shop. The articles to be treated are heated in crucibles containing cyanide, the exact mixing of which enables the temperature fo be kept within close limits, thus ensuring equal hardening for components of the same type.
A simple but effective system is employed for "chasing " components. Tabs are utilized, these. being brown for current production,green to indicate the need for speeding up, and red where parts are urgently required.
All these efforts would, however, be of little use unless the pumps were thoroughly tested
and adjusted before being supplied, and constant improvements are being made in the equipment of the test shop. Every pump is also endurance tested before final adjustment. The 'system employed in effecting adjustments is to run a pump and to collect the fuel from each pumping element, passing it through carefully set nozzles into graduated glass. tubes. The machine is arranged so that the pump is tripped after 100 strokes, thus magnifying any error 100 times. The latest' machine of this type, made by C.A.V.-Bosch, Ltd., has been designed to deal with pumps for 12-cylindered engines, which indicates what may be expected in the future, because,
at present, the largest number of cylinders dealt with is eight.
In addition to checking quantity, this type of testing machine can indicate most accurately the time of injection. For this purpose the drive to the pump carries a disc marked clearly in degrees, and at the moment of injection a spark contained in an eye-piece passes across this wheel, giving a stroboscopic effect which permits the actual numbers on the dial wheel to be read while it is rotating.
Perhaps the most important factor in the efficient running and operating of a pump • is adequate filtering of the fuel, and oil centrifuges are employed in the laboratory for testing for any dirt in the oil samples taken from inadequately filtered Systems.
So much of the successful operation of an oil engine depends upon pump maintenance, particularly from the point of view of cleanliness, that the company has inaugurated a fourday course for the maintenanc. mechanics of big users. In the laboratory placed at their disposal are not only diagrams and models; but complete pumps of all types, which they are re quired to take down and reassemble, also numerous items of fuel injection equipment, partly sectioned.
The closest co-operation exists between the company and the makers of oil engines, many of whom send their latest units to the test department, so that there can be no question as to the suitability of the equipment.
In brief, we left with a strongly impressed appreciation.of the progress made by the C.A.V.-Bosch company in this highly specialized field, and a feeling of satisfaction at having seen for ourselves every process in the manufacture of this 100-per-cent. British injection system for British oil engines.