Forklifts with a twist
Page 42
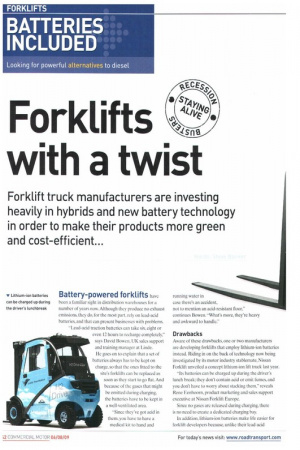
Page 43
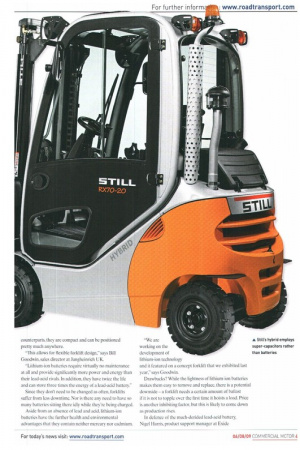
Page 44
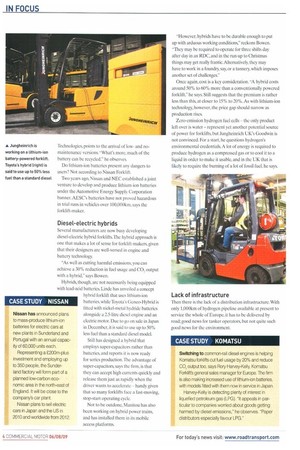
Page 45
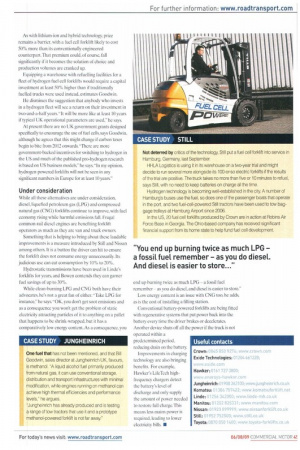
If you've noticed an error in this article please click here to report it so we can fix it.
Forklift truck manufacturers are investing heavily in hybrids and new battery technology in order to make their products more green and cost-efficient...
Battery-powered forklifts have been a familiar sight in distribution warehouses for a number of years now. Although they produce no exhaust emissions, they do, for the most part, rely on lead-acid batteries, and that can present businesses with problems.
"Lead-acid traction batteries can take six, eight or even 12 hours to recharge completely," says David Bowen, UK sales support and training manager at Linde. He goes on to explain that a set of batteries always has to be kept on charge, so that the ones fitted to the site's forklifts can be replaced as soon as they start to go flat. And because of the gases that might be emitted during charging, the batteries have to be kept in a well-ventilated area.
"Since they've got acid in them, you have to have a medical kit to hand and running water in case there's an accident, not to mention an acid-resistant floor," continues Bowen. "What's more, they're heavy and awkward to handle."
Drawbacks
Aware of these drawbacks, one or two manufacturers are developing forklifts that employ lithium-ion batteries instead. Riding in on the back of technology now being investigated by its motor industry stablemate. Nissan Forklift unveiled a concept lithium-ion lift truck last year.
"its batteries can he charged up during the driver's lunch break; they don't contain acid or emit fumes, and you don't have to worry about stacking them," reveals Rene Fen boom, product marketing and sales support executive at Nissan Forklift Europe.
Since no gases are released during charging, there is no need to create a dedicated charging bay.
in addition, lithium-ion batteries make life easier for forklift developers because, unlike their lead-acid counterparts, they are compact and can be positioned pretty much anywhere.
"This allows for flexible forklift design," says Bill Goodwin, sales director at Jungheinrich UK.
"Lithium-ion batteries require virtually no maintenance at all and provide significantly more power and energy than their lead-acid rivals. In addition, they have twice the life and can store three times the energy of a lead-acid battery."
Since they don't need to be changed as often, forklifts suffer from less downtime. Nor is there any need to have so many batteries sitting there idly while they're being charged.
Aside from an absence of lead and acid, lithium-ion batteries have the further health and environmental advantages that they contain neither mercury nor cadmium. "We are working on the development of lithium-ion technology and it featured on a concept forklift that we exhibited last year," says Goodwin.
Drawbacks? While the lightness of lithium-ion batteries makes them easy to remove and replace. there is a potential downside — a forklift needs a certain amount of ballast if it is not to topple over the first time it hoists a load. Price is another inhibiting factor, but this is likely to come down as production rises.
In defence of the much-derided lead-acid battery, Nigel Harris, product support manager at Exide Technologies, points to the arrival of lowand nomaintenance versions. "What's more, much of the battery can be recycled," he observes.
Do lithium-ion batteries present any dangers to users? Not according to Nissan Forklift.
Two years ago, Nissan and NEC established a joint venture to develop and produce lithium-ion batteries under the Automotive Energy Supply Corporation banner. AESC's batteries have not proved hazardous in trial runs in vehicles over 100,000km, says the forklift-maker.
Diesel-electric hybrids
Several manufacturers are now busy developing diesel-electric hybrid forklifts. The hybrid approach is one that makes a lot of sense for forklift-makers, given that their designers are well-versed in engine and battery technology.
"As well as cutting harmful emissions, you can achieve a 30% reduction in fuel usage and CO, output with a hybrid," says Bowen.
Hybrids, though, are not necessarily being equipped with lead-acid batteries. Linde has unveiled a concept hybrid forklift that uses lithium-ion batteries, while Toyota's Geneo-Hybrid is fitted with nickel-metal hydride batteries alongside a 2.5-litre diesel engine and an electric motor. Due to go on sale in Japan in December, it is said to use up 10 50% less fuel than a standard diesel model.
NISSAN
Still has designed a hybrid that employs super-capacitors rather than batteries, and reports it is now ready for series production. The advantage of super-capacitors, says the firm, is that they can accept high currents quickly and release them just as rapidly when the driver wants to accelerate handy given that so many forklifts face a fast-moving, stop-start operating cycle.
Not to be outdone, Manitou has also been working on hybrid power trains, and has installed them in its mobile access platforms.
-However, hybrids have to be durable enough to put up with arduous working conditions," reckons Bowen. "They may be required to operate for three shifts day after day in an RDC, and in the run-up to Christmas things may get really frantic. Alternatively they may have to work in a foundry, say, or a tannery, which imposes another set of challenges."
Once again, cost is a key consideration. "A hybrid costs around 50% to 60% more than a conventionally powered forklift," he says. Still suggests that the premium is rather less than this, at closer to 15% to 20%. As with lithium-ion technology, however, the price gap should narrow as production rises.
Zero-emission hydrogen fuel cells the only product left over is water represent yet another potential source of power for forklifts, but Jungheinrich UK's Goodwin is not convinced. For a start, he questions hydrogen's environmental credentials. A lot of energy is required to produce hydrogen as a compressed gas or to cool it to a liquid in order to make it usable, and in the UK that is likely to require the burning of a lot of fossil fuel, he says.
Lack of infrastructure
Then there is the lack of a distribution infrastructure. With only 1,000km of hydrogen pipeline available at present to service the whole of Europe, it has to be delivered by road; good news for tanker operators, but not quite such good news for the environment.
As with lithium-ion and hybrid technology-, price remains a barrier, with a fuel cell forklift likely to cost 50% more than its conventionally engineered counterpart. That premium could, of course, fall significantly if it becomes the solution of choice and production volumes are cranked up.
Equipping a warehouse with refuelling facilities for a fleet of hydrogen fuel cell forklifts would require a capital investment at least 50% higher than if traditionally fuelled trucks were used instead, estimates Goodwin.
I le dismisses the suggestion that anybody who invests in a hydrogen fleet will see a return on their investment in two-and-a-half years. It will be more like at least 10 years if typical UK operational parameters are used," he says.
At present there are no UK government grants designed specifically to encourage the use of fuel cells, says Goodwin, although he agrees that this might change if carbon taxes begin to bite from 2012 onwards. "There are more government-backed incentives for switching to hydrogen in the US and much of the published pro-hydrogen research is based on US business models," he says. "in my opinion, hydrogen-powered forklifts will not he seen in any significant numbers in Europe for at least 10 years."
Under consideration
While all these alternatives are under consideration, diesel, liquefied petroleum gas (LPG) and compressed natural gas (CNC.I) forklifts continue to improve, with fuel economy rising while harmful emissions fall. Frugal common-rail diesel engines are benefiting forklift operators as much as they are van and truck owners.
Something that is helping to bring about these laudable improvements is a measure introduced by Still and Nissan among others. It is a button the driver can hit to ensure the forklift does not consume energy unnecessarily. Its judicious use can cut consumption by 10% to 20%.
Hydrostatic transmissions have been used in Linde's forklifts for years, and Bowen contends they can garner fuel savings of up to 30%.
While clean-burning LPG and CNG both have their advocates, he's not a great fan of either. -Take LPG for instance," he says. "OK, you don't get soot emissions and as a consequence you won't get the problem of static electricity attracting particles of it to anything on a pallet that happens to be shrink-wrapped, but it has a comparatively low energy content. As a consequence, you
_ end up burning twice as much LPG —a fossil fuel remember — as you do diesel, and diesel is easier to store."
Low energy content is an issue with CNC too, he adds, as is the cost of installing a filling station.
Conventional battery-powered forklifts are being fitted with regenerative systems that put power back into the battery every time the driver brakes or decelerates Another device shuts off all the power if the truck is not operated within a predetermined period, reducing drain on the battery.
Improvements in charging technology are also bringing benefits. For example, Hawker's LifeTech highfrequency chargers detect the battery's level of discharge and only supply the amount of power needed to restore full charge. This means less mains power is required, leading to lower electricity bills. •