road and
Page 66
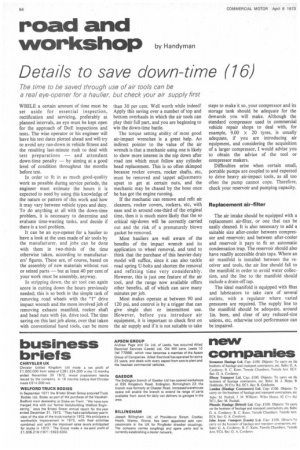
If you've noticed an error in this article please click here to report it so we can fix it.
workshop by Handyman
Details to save down-time (16)
The time to be saved through use of air tools can be a real eye-opener for a haulier, but check your air supply first
WHILE a certain amount of time must be set aside for essential inspection, rectification and servicing, preferably at planned intervals, an eye must be kept open for the approach of DoE inspections and tests. The wise operator or his engineer will have his test dates plotted ahead and will try to avoid any run-down in vehicle fitness and the resulting last-minute rush to deal with test preparations — and attendant down-time penalty — by aiming at a good level of condition throughout the months before test.
In order to fit in as much good-quality work as possible during service periods, the engineer must estimate the hours it is expected to need by using this knowledge of the nature or pattern of this work and how it may vary between vehicle types and duty. To do anything at all with the down-time problem, it is necessary to determine and evaluate time-wasting tasks, and decide if there is a tool problem.
It can be an eye-opener for a haulier to have a look at the uses made of air tools by the manufacturer, and jobs can he done with them in two-thirds of the time otherwise taken, according to manufacturers' figures. These are, of course, based on the assembly of new materials without rust or seized parts — but at least 40 per cent of your work must be assembly, anyway.
In stripping down; the air tool can again score in cutting down the hours previously needed; this is so both in the simple task of removing road wheels with the "I" drive impact wrench and the more involved job of removing exhaust manifold, rocker shaft and head nuts with +in. drive tool. The time saving on this last job alone, over that taken with conventional hand tools, can be more than 30 per cent. Well worth while indeed! Apply this saving over a number of top and bottom overhauls in which the air tools can play their full part, and you are beginning to win the down-time battle.
The torque setting ability Of most good air-impact wrenches is a great help. An indirect pointer to the value of the air wrench is that a mechanic using one is likely to show more interest in the nip down after road test which must follow any cylinder head replacement, This is so often skimped because rocker covers, rocker shafts, etc, must be removed and tappet adjustments upset to get at certain nuts, and the mechanic may be chased by the boss once he has got the engine running.
If the mechanic can remove and refit air cleaners, rocker covers, rockers, etc, with ease and in around one-third of the original time, then it is much more likely that the so critical nip-down will be correctly carried out and the risk of a prematurely blown gasket be removed.
Most hauliers are well aware of the benefits of the impact wrench and its application to wheel removal, and tend to think that the purchase of this heavier-duty model will suffice, since it can also tackle road spring U-bolts and shorten the removal and refitting time very considerably. However, this is just one feature of the air tool, and the range now available offers other benefits, all of which can save many minutes per job.
Most makes operate at between 90 and 120 psi, and control is by a trigger that can give single shot or intermittent use However, before you introduce air equipment, it is important to check first on the air supply and if it is not suitable to take steps to make it so, your compressor and its storage tank should be adequate for the demands you will make. Although the standard compressor used in commercial vehicle repair shops to deal with, for example, 9.00 X 20 tyres, is usually adequate, if you are introducing air equipment, and considering the acquisition of a larger compressor, I would advise you to obtain the advice of the tool or compressor makers.
Difficulties arise when certain small, portable pumps are coupled to and expected to drive heavy air-impact tools, as all too often the pump cannot cope. Therefore, check your reservoir and pumping capacity.
Replacement air–filter The air intake should be equipped with a replacement air-filter, or one that can be easily cleaned. It is also necessary to add a suitable size after-cooler between compressor and reservoir; and between after-cooler and reservoir it pays to fit an automatic condensation trap. The reservoir should also have readily accessible drain taps. Where an air manifold is installed between the receiver and tools, the air line should fall to the manifold in order to avoid water collection, and the line to the manifold should include a drain-off tap.
The ideal manifold is equipped with filter and lubricators to take care of several outlets, with a regulator where varied pressures are required. The supply line to the manifold should be adequate, around lin. bore, and clear of any reduced-size unions, etc, otherwise tool performance can be impaired.