Ingenuity OVE
Page 50
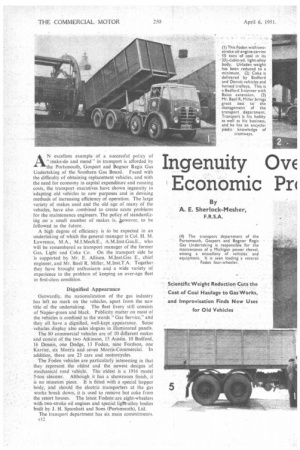
Page 51
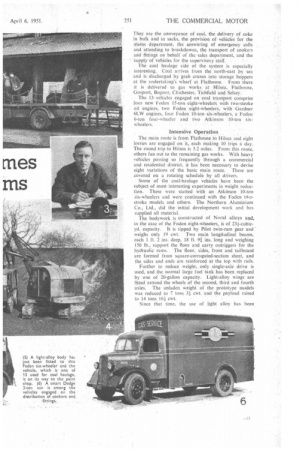
Page 52
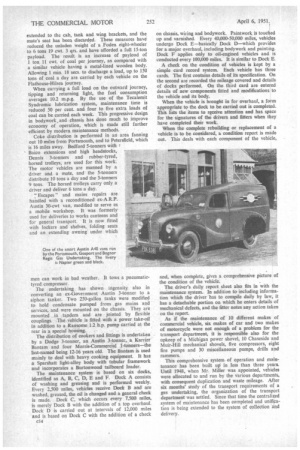
If you've noticed an error in this article please click here to report it so we can fix it.
mes Economic Pri ms
By A. E. Sherlock-Mesher, F.R.S.A. AN excellent example of a successful policy of "make-do and mend" in transport is afforded by the Portsmouth, Gosport and Bognor Regis Gas Undertaking of the Southern Gas Board. Faced with the difficulty of obtaining replacement vehicles, and with the need for economy in capital expenditure and running costs, the transport executives have shown ingenuity in adapting old vehicles to new purposes and in devising methods of increasing efficiency of operation. The large variety of makes used and the old age of many of the vehicles, have also combined to create acute problems for the maintenance engineers. The policy of standardizing on a small number of makes is, however, to be followed in the future.
A high degree of efficiency is to be expected in an undertaking of which the general manager is Col. H. M, Lawrence, M.A., M.I.Mech.E., A.M.Inst.Gas.E., who will be remembered as transport manager of the former Gas, Light and Coke Co. On the transport side he is supported by Mr. E. Allison, Minst.Gas E., chief engineer, and Mr. Basil R. Miller, Minst.T.A. Together they have brought enthusiasm and a wide variety of experience to the problem of keeping an over-age fleet in first-class condition.
Dignified Appearance
Outwardly, the nationalization of the gas industry has left no mark on the vehicles, apart from the new title of the undertaking. The fleet livery still consists of Napier-green and black. Publicity matter on most of the vehicles is confined to the words "Gas Service," and they all have .a dignified, well-kept appearance. Some vehicks display also sales slogans in illuminated panels. The 80 commercial vehicles are of 10 different makes and consist of the two Atkinson, 15 Austin, 10 Bedford, 16 Dennis, one Dodge, 13 Foden, nine Fordson, one Karrier, six Morris andseven Morris-Commercial. In addition, there are 23 cars and motorcycles.
The Foden vehicles are particularly interesting in that they represent the oldest and the newest designs of mechanical road vehicle. The oldest is a 1916 model 5-ton steamer. Although it has a showroom finish, it is no museum piece. It is fitted with a special hopper body, and should_ the electric transporters at the gas works break down, it is. used to remove hot coke from the retort houses. The latest Fodens are eight-wheelers with two-stroke oil engines and special liglit-alloy bodies built by J. H. Sparshatt and Sons (Portsmouth), Ltd,
The transport department has six main commitments.
el 2
They arc the conveyance of coal, the delivery of coke in bulk and in sacks, the provision of vehicles for the Mains department, the answering of emergency calls and attending. to breakdowns, the transport of cookers arid fitting§ on behalf of the sales department, and the Supply of Vehicles for the supervisory Stall.
The coal haulage side of the system is especially interesting. Coal arrives from the north-east by sea and is discharged by grab cranes into storage hoppers at the undertaking's wharf at Flathouse. From there it is delivered to gas Works at Hilsea, Flathouse, Gosport, Bognor, Chichester, Tichficld and..Selsey.
The 13-vehicles engaged on coal transport eomprise four new Foden I5-ton. eight-wheelers with two-stroke oil engines, two Foden eight-wheelers, with: Gardner 6LW engines, four Foden 10-ton six-wheelers, a Foden 6-ton four-wheeler and two Atkinson 10-ton sixWheelers.
Intensive Operation The main route is from Flathouse to Hilsea and eight lorries are engaged on it, each making 10 trips a day. The round trip to Hilsea is 5.2 miles. From this route, others fan out to the remaining gas works. With heavy vehicles passing so frequently through a commercial and residential district, it has been necessary to devise eight variations of the basic main route. These are covered on a rotating schedule by all drivers.
Some of the coal-haulage vehicles have been the subject of most interesting experiments in weight reduction. These were started with an Atkinson 10-ton six-wheelers and were continued with the Foden tAiostroke models and others. The Northern Aluminium Co., Ltd., did the initial development work and has supplied all material.
The bodywork is constructed of Noral alloys and, in the case of the Foden eight-wheelers, is of 231-cubicyd. capacity. 11 is tipped by Pilot twin-ram gear and weighs only 19 cwt. Two main longitudinal beams. each 1 ft. 2 ins. deep, 18 ft. 9.1 ins, long and weighing 150 lb., support the floor and carry outriggers for the hydraulic rams. The floor, sides, front and tailboard are formed from square-corrugated-section sheet, and the sides and ends are reinforced at the top with rails.
Further to reduce weight,, only single-axle drive is used, and the normal large fuel tank has been replaced by one of 20-gallon capacity. Light-alloy wings are fisted around the wheels of the second, third and fourth axles. The unladen weight of the prototype models was reduced to 7 tons 31 cwt. and the payload raised to 14 tons 161 cwt.
Since that time, the use of light alloy has been
extended to the cab, tank and wing brackets, and the mate's seat has been discarded. These measures have reduced the unladen weight of a Foden eight-wheeler to 6 tons 19 cwt. 3 qrs. and have afforded a full 15-ton payload. The result is an increase of payload of 1 ton 11 cwt. of coal per journey, as compared with a similar vehicle having a metal-lined wooden body.
Allowing 1 min. 18 secs. to discharge a load, up to 150 tons of coal a day are carried by each vehicle on the Flathouse-Hilsea journey.
When carrying a full load on the outward journey, tipping and returning light, the fuel consumption averages 10.2 m.p.g. By the use of the Tecalemit Syndrornic lubrication system, maintenance time is reduced 50 per cent. and four to five extra loads of coal can be carried each week. This progressive design in bodywork, and chassis has done much to improve economy of operation, which is made still further efficient by modern maintenance methods.
Coke distribution is performed in an area fanning out 10 miles from Portsmouth, and to Petersfield, which is 16 miles away. Bedford 5-tonners with Baico extensions and high headstocks, Dennis 3-tanners and rubber-tyred, horsed trolleys, are used for this work.
The motor vehicles are manned by a driver and a mate, and the 5-tonners distribute 10 tons a day and the 3-tonners 9 tons. The horsed trolleys carry only a driver and deliver 6 tons a day.
" Escapes " and mains repairs are handled with a reconditioned ex-A.R.P.
Austin 30-cwt van, modified to serve as a mobile workshop. It was formerly used for deliveries to works canteens and for general transport. It is now fitted with lockers and shelves, folding seats and an extending awning under which men can work in bad weather. It tows a pneumatictyred compressor.
The undertaking has shown ingenuity also in converting an ex-Government Austin 3-tonner to a siphon tanker. Two 250-gallon tanks were modified to hold condensate pumped from . gas mains and services, and were mounted on the chassis. They are mounted in tandem and are jointed by flexible couplings. The vehicle is fitted with a power take-off in addition to a Ransome 1.2 h.p. pump carried at the rear in a special housing.
The distribution of cookers and fittings is undertaken by a Dodge 3-tonner, an Austin 3-tonner, a Karrier Bantam and four Morris-Commercial 1-toners—the last-named being 12-16 years old. The Bantam is used in.iinly to deal with heavy cooking equipment. It has a Sparshatt light-alloy body with tubular framework and incorporates a Burtonwood tailboard loader,
The maintenance system is based on six docks, identified as A, B, C, D, E and F. Dock A consists of washing and greasing and is performed weekly. Every 2,500 miles, vehicles receive Dock B and are washed, greased, the oil is changed and a general check is made. Dock C, which occurs every 7,500 miles, is merely Dock B with the addition of a top overhaul. Dock D is carried out at intervals of 12,000 miles and is based on Dock C with the addition of a check
c14 on chassis, wiring and bodywork. Paintwork is touched up and varnished. Every 40,000-50,000 miles, vehicles undergo Dock E—basically Dock D—which provides for a major overhaul, including bodywork and painting. Dock F applies only to oil-engined vehicles and is conducted every 100,000 miles. It is similar to Dock E.
A check on the condition of vehicles is kept by a simple card record system. Each vehicle has three cards. The first contains details of its specification. On the second are recorded the mileage covered and details of docks performed. On the third card are entered details of new components fitted and modifications to the vehicle and its body.
When the vehicle is brought in for overhaul, a form appropriate to the dock to be carried out is completed. This lists the items to receive attention and has space for the signatures of the drivers and fitters when they have completed their work.
When the complete rebuilding or replacement of a vehicle is to be considered, a condition report is made out. This deals with each component of the vehicle, and, when complete, gives a comprehensive picture of the condition of the vehicle.
The driver's daily report sheet also fits in with the maintenance system. In addition to including information which the driver has to compile daily by law, it has a detachable portion on which he enters details of mechanical defects, and the fitter notes any action taken on the report.
As if the maintenance of 10 different makes of commercial vehicle, six makes of car and two makes of motorcycle were not enough of a problem for the transport department, it is responsible also for the upkeep of a Michigan power shovel, 10 Chaseside and Muir-Hill mechanical shovels, five compressors, eight fire pumps and 30 miscellaneous pumps, drills and ram mers.
This comprehensive system of operation and maintenance has been built tip in less than three years. Until 1948, when Mr. Miller was appointed, vehicles were allocated to and run by the various departments, with consequent duplication and waste mileage. After six months' study of the transport requirements of a gas undertaking, the organization of the transport department was settled. Since that time the centralized system of maintenance has been completed and unification is being extended to the system of collection and delivery.