The ifs and buts of better braking
Page 51
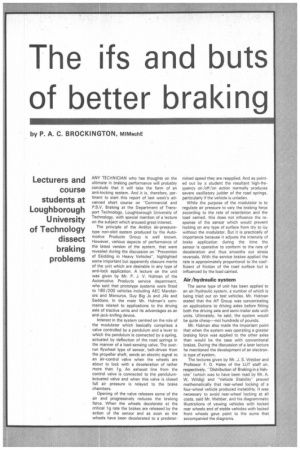
Page 52
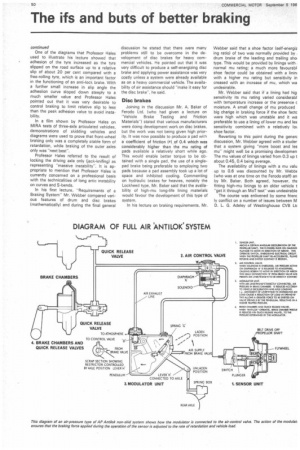
Page 53
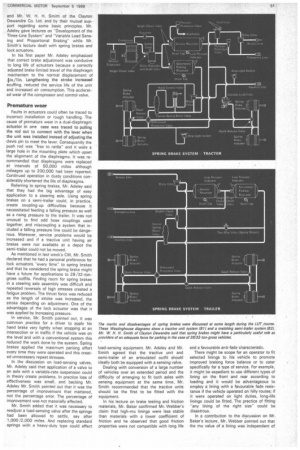
Page 54
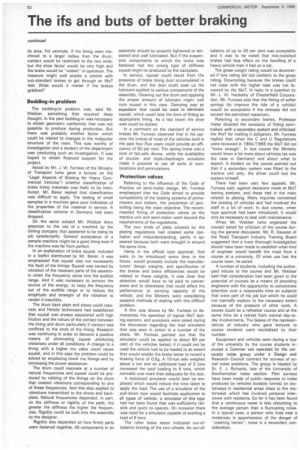
If you've noticed an error in this article please click here to report it so we can fix it.
by P. A. C. BROCK1NGTON, MIMechE
Lecturers and course students at Loughborough University of Technology dissect braking problems
ANY TECHNICIAN who has thoughts on the ultimate in braking performance will probably conclude that it will take the form of an anti-locking system. And it is, therefore, pertinent to start this report of last week's advanced short course on "Commercial and P.S.V. Braking at the Department of Transport Technology, Loughborough University of Technology, with special mention of a lecture on the subject which aroused great interest.
The principle of the Antilok air-pressuretype non-skid system produced by the Automotive Products Group is well known. However, various aspects of performance of the latest version of the system, that were revealed during the discussion on "Prevention of Skidding in Heavy Vehicles", highlighted some important but apparently obscure merits of the unit which are desirable in any type of anti-lock application, A lecture on the unit was given by Mr. P. J. V. Holman of the Automotive Products service department, who said that prototype systems were fitted to 180/200 vehicles including AEC Mandators and Mercurys, Guy Big Js and J4s and Seddons. In the main Mr. Holman's comments related to applications to the driving axle of tractive units and its advantages as an anti-jack-knifing device.
Interest in the system centred on the role of the modulator which basically comprises a valve controlled by a pendulum and a lever to which the pendulum is connected by a spring, actuated by deflection of the road springs in the manner of a load-sensing valve. The overrun flywheel type of sensor, belt-driven from the propeller shaft, sends an electric signal to an air-control valve when the wheels are about to lock with a deceleration of rather more than 1g. An exhaust line from the control valve is connected to the pendulumactuated valve and when this valve is closed full air pressure is relayed to the brake chambers.
Opening of the valve releases some of the air and progressively reduces the braking force. When the wheels decelerate at the critical 1g rate the brakes are released by the action of the sensor and as soon as the wheels have been decelerated to a predeter
mined speed they are reapplied. And as pointed out by a student the resultant high-frequency on /off /on action normally produces severe oscillatory judder of the road springs. particularly if the vehicle is unladen.
While the purpose of the modulator is to regulate air pressure to vary the braking force according to the rate of retardation and the load carried, this does not influence the response of the sensor which would prevent locking on any type of surface from dry to icy without the modulator. But it is practically of importance because it adjusts the intensity of brake application during the time the sensor is operative to conform to the rate of deceleration and thus smooths out stress reversals. With the service brakes applied the rate is approximately proportional to the coefficient of friction of the road surface hut is influenced by the load carried.
Air/hydraulic system
The same type of unit has been applied to an air /hydraulic system, a number of which is being tried out on test vehicles. Mr. Holman stated that the AP Group was concentrating on applications to driving axles before fitting both the driving axle and semi-trailer axle with units. Ultimately, he said, the system would be quite cheap—not hundreds of pounds.
Mr. Holman also made the important point that when the system was operating a greater braking force was applied to the other axles than would be the case with conventional brakes. During the discussion of a later lecture he mentioned the development of an electronic type of system.
The lectures given by Mr. J. S. Webber and Professor F. D. Hales of the LUT staff on, respectively, "Distribution of Braking in a Vehicle" (which was to have been read by Mr. A. W. Wildig) and "Vehicle Stabilityproved mathematically that rear-wheel locking of a four-wheel vehicle produced instability. It was necessary to avoid rear-wheel locking at all costs, said Mr. Webber, and his diagrammatic illustrations of yawing vehicles with locked rear wheels and of stable vehicles with locked front wheels gave point to the sums that accompanied the diagrams.
One of the diagrams that Professor Hales used to illustrate his lecture showed that adhesion of the tyre increased as the tyre slipped on the road surface up to a relative slip of about 20 per cent compared with a free-rolling tyre, which is an important factor in the functioning of an anti-lock brake. With a further small increase in slip angle the adhesiion curve sloped down steeply to a much smaller value and Professor Hales pointed out that it was very desirable to control braking to limit relative slip to less than the peak adhesion value to avoid instability.
In a film shown by Professor Hales on MIRA tests of three-axle articulated vehicles, demonstrations of skidding vehicles and diagrams Were used to prove that front-wheel braking only was a completely stable form of retardation, while braking of the outer axles only was "next best".
Professor Hales referred to the result of locking the driving axle only (jack-knifing) as representing "massive instability". It is appropriate to mention that Professor Hales is currently concerned on a professional basis with the technicalities of long artic instability on curves and S-bends.
In his first lecture, "Requirements of a Braking System" Mr. Webber compared various features of drum and disc brakes (mathematically] and during the final general discussion he stated that there were many problems still to be overcome in the development of disc brakes for heavy commercial vehicles. He pointed out that it was very difficult to produce a self-energizing disc brake and applying power assistance was very costly unless a system were already available as on a heavy commercial vehicle. The availability of air assistance should "make it easy for the disc brake", he said.
Disc brakes
Joining in the discussion Mr. A. Baker of Ferodo Ltd. (who had given a lecture on "Vehicle Brake Testing and Friction Materials") stated that various manufacturers were doing development work on disc brakes, but the work was not being given high priority. It was now possible to produce a pad with a coefficient of friction (u)of 0.4 which was considerably higher than the mu rating of pads available a relatively short while ago. This would enable better torque to be ob tamed with a single pad, the use of a singlepad brake being preferable to employing two pads because a pad assembly took up a lot of space and inhibited cooling. Commenting on hydraulic brakes for heavies, notably the Lockheed type, Mr. Baker said that the availability of high-mu long-life lining materials would favour the development of this type of system.
In his lecture on braking requirements, Mr.
Webber said that a shoe factor (self-energiz ing ratio) of two was normally provided by drum brake of the leading and trailing ship, type. This would be provided by linings with normal mu rating; a much more favourabl shoe factor could be obtained with a
with a higher mu rating but sensitivity in creased with an increase of mu, which wa undesirable.
Mr. Webber said that if a lining had hig sensitivity its mu rating varied considerabl with temperature increase or the presence c moisture. A small change of mu produced big change in braking force if the shoe factc were high which was unstable and it wa preferable to use a lining of lower mu and lea sensitivity combined with a relatively lo+, shoe factor.
Reverting to this point during the gener discussion, Mr. Webber agreed with a studer that a system giving -more boost and les mu" might well be a promising developmen The mu values of linings varied from 0.3 up t about 0.45, 0.4 being average.
The availability of linings with a mu valu up to 0.6 was discounted by Mr. Webb( (who was at one time on the Ferodo staff) an by Mr. Baker. Both agreed, however, tht fitting high-mu linings to an older vehicle t "get it through an MoT test" was undesirable The course was enlivened by some frienc ly conflict on a number of issues between M D. L. G. Adeley of Westinghouse CVB Lt< and Mr. W. H. H. Smith of the Clayton Dewandre Co. Ltd. and by their mutual support regarding some basic principles. Mr. Adeley gave lectures on "Development of the Three-Line System" and "Variable Load Sensing and Proportional Braking" while Mr. Smith's lecture dealt with spring brakes and lock actuators.
In his first paper Mr. Adeley emphasized that correct brake adjustment was conducive to long life of actuators because a correctly adjusted brake limited travel of the diaphragm mechanism to the normal displacement of lin./1 in. Lengthening the stroke increased scuffing, reduced the service life of the unit and increased air consumption. This acclerated wear of the compressor and control valve.
Premature wear
Faults in actuators could often be traced to incorrect installation or rough handling. The cause of premature wear in a dual-diaphragm actuator in one case was traced to pulling the rod out to connect with the lever when the unit was installed instead of adjusting the clevis pin to meet the lever. Consequently the push rod was "free to rattle" and it wore a large hole in the mounting plate which upset the alignment of the diaphragms. It was recommended that diaphragms were replaced at intervals of 50,000 miles although mileages up to 200,000 had been reported. Continued operation in dusty conditions considerably shortened the life of diaphragms.
Referring to spring brakes, Mr. Adeley said that they had the big advantage of easy application to a steering axle. Using spring brakes on a semi-trailer could, in practice, create coupling-up difficulties because it necessitated feeding a falling pressure as well as a rising pressure to the trailer. It was not unusual to find odd hose couplings used together, and miscoupling a system that included a falling pressure line could be dangerous. Moreover, service problems would be increased and if a tractive unit having air brakes were not available at a depot the semi-trailer could not be moved.
As mentioned in last week's CM, Mr. Smith declared that he had a personal preference for lock actuators "every time" to spring brakes and that he considered the spring brake might have a future for applications to 28 /32-tongross outfits. Finding room for spring brakes in a steering axle assembly was difficult and repeated reversals of high stresses created a fatigue problem. The thrust force was reduced as the length of stroke was increased, the stroke depending on adjustment. One of the advantages of the lock actuator was that it was applied by increasing pressure.
In service, Mr. Smith pointed out, it was common practice for a driver to apply his hand brake very lightly when stopping at an intersection or in traffic if the vehicle was on the level and with a conventional system this reduced the work done by the system. Spring brakes applied the maximum parking effort every time they were operated and this created unnecessary repeat stresses.
In the discussion on load-sensing valves, Mr. Adeley said that application of a valve to an axle with a variable-rate suspension could in theory create problems. In practice loss of effectiveness was small, and backing Mr.
Adeley Mr. Smith pointed out that it was the percentage of improvement that mattered, not the percentage error. The percentage of improvement was not materially affected.
Mr. Smith added that it was necessary to readjust a load-sensing valve after the springs had been allowed to settle, say after 1,000 /2,000 miles, And replacing standard springs with a heavy-duty type could affect load-sensing equipment. Mr. Adeley and Mr. Smith agreed that the tractive unit and semi-trailer of an articulated outfit should ideally both be equipped with a sensing valve.
Dealing with conversion of a large number of vehicles over an extended period and the difficulty of arranging to fit both axles with sensing equipment at the same time, Mr. Smith recommended that the tractive units should be the first to be fitted with the equipment.
In his lecture on brake testing and friction materials, Mr. Baker confirmed Mr. Webber's claim that high-mu linings were less stable than materials with a lower coefficient of friction and he observed that good friction properties were not compatible with long life and a favourable anti-fade characteristic.
There might be scope for an operator to fit selected linings to his vehicle to promote improved braking force balance or to cater specifically for a type of service. For example, it might be expedient to use different types of lining on the front and rear according to loading and it would be advantageous to employ a lining with a favourable fade resistance if the vehicle operated on hilly routes; if it were operated on light duties, long-life linings could be fitted. The practice of fitting "any lining of the right size" could be disastrous.
In a contribution to the discussion on Mr. Baker's lecture, Mr. Webber pointed out that the mu value of a lining was independent of
its area. For example, if the lining were machined to a larger radius than the drum, contact would be restricted to the two ends; but the shoe factor would be very high and the brake would be -violent" in operation. The measure might well enable a vehicle with sub-standard brakes to get through an MoT test. What would it matter if the brakes grabbed?
Bedding-in problem
The bedding-in problem was, said Mr. Webber, something that required deep thought. In the past bedding-in was necessary to obtain geometric conformity that was not possible to produce during production. But there was probably another factor which could be related to changes in the molecular structure of the resin. This was worthy of investigation and a student of the department was conductng such an investigation. It was hoped to obtain financial support for the project.
Asked by Mr. J. W. Furness of the Ministry of Transport (who gave a lecture on the "Legal Aspects of Braking for Heavy Commercial Vehicles") whether classification of brake lining materials was likely to be introduced, Mr. Baker replied that classification was difficult to apply. The testing of small samples in a machine gave poor indication of the properties of the material in service. A classification scheme in Germany had been dropped.
On the same subject Mr. Webber drew attention to the use of a machine by the Girling company that appeared to be doing its job satisfactorily. General acceptance of a sample machine might be a good thing even if the machine was far from perfect.
In an explanation of brake squeal, included in a leaflet distributed by Mr. Baker, it was emphasized that squeal was not necessarily the fault of the linings. Squeal was caused by vibration of the resonant parts of the assembly when the frequency came into the audible range. And it was necessary to remove the source of the energy, to keep the frequency out of the audible range or to reduce the amplitude and strength of the vibration to render it inaudible.
The drum back plate and shoes could resonate and Ferodo technicians had established that squeal was always associated with high friction and the nature of the contact between the lining and drum particularly if contact was confined to the ends of the lining. Research was continuing in order to discover a positive means of eliminating squeal producing vibrations under all conditions. A change to a lining with a higher mu value could cause squeal, and in this case the problem could be solved by employing lower mu linings and by increasing the power assistance.
The drum could resonate at a number of natural frequencies and squeal could be pro duced by rubbing of the linings on the drum that created vibrations corresponding to one of these frequencies. And this also applied to vibrations transmitted to the shoes and back plate. Natural frequencies depended, in part, on the stiffness or rigidity of the pads, the greater the stiffness the higher the frequencies. Rigidity could be built into the assembly by the designer.
Rigidity also depended on how firmly parts were fastened together. All components in an assembly should be properly tightened or tensioned and well lubricated. But if the suspension components to which the brake was fastened had the wrong type of stiffness squeal might be produced by the backplate.
In service, squeal could result from the presence of brake lining dust accumulated in the drum, and the dust could soak up the lubricant applied to various components of the assembly. Cleaning out the drum and applying the proper amount of lubricant might well cure squeal in this case. Damping was an expedient that could be used to eliminate squeal, which could take the form of fitting an appropriate lining. As a last resort the shoe web could be slotted.
In a comment on the standard of service brakes Mr. Furness observed that in his opinion the brakes of most of the vehicles built in the past four/five years could provide an efficiency of 50 per cent. The spring brake was a kind of fail-safe device, while the availability of doubleand triple-diaphragm actuators made it possible to use all sorts of combinations and permutations.
Protection valves
Referring to the influence of the Code of Practice on semi-trailer design, Mr. Furness emphasized that the Code aimed to provide compatibility of the braking systems of primemovers and trailers, the prevention of jackknifing being the main objective. The recommended fitting of protection valves on .the tractive unit and semi-trailer went beyond the requirements of the regulations.
The two kinds of plate covered by the plating regulations had created some confusion and misunderstanding, partly it appeared because both were brought in around the same time.
Items in the official type approval, that were to be introduced some time in the future, would probably include the manufacturers' design weights, and specification of the brakes and brake efficiencies would be related to these weights. It was clear that attention would have to be paid to conversions and to alterations that could affect the performance or carrying capacity of the vehicle, and the Ministry were considering possible methods of dealing with this difficult problem.
A film was shown by Mr. Furness to demonstrate the operation of typical MoT testing stations, and questions were asked during the discussion regarding the load simulator that was seen in action in a number of the shots. Mr. Furness pointed out that the simulator could be applied to about 80 per cent of the vehicles tested; if it could not be used the vehicle had to be loaded to an extent that would enable the brake tester to record a braking force of 0.5g. A 10-ton axle weighed about a ton and an additional load of 5 tons increased the total loading to 6 tons, which normally was more than adequate for the test.
A motorized simulator would later be employed which would reduce the time taken to apply the load. The use of a simulator of the pull-down type would facilitate application to all types of vehicle: a simulator of this type had not been found that was sufficiently reliable and quick to operate. On occasion there was need for a simulator capable of exerting a load of 6 tons.
The roller brake tester indicated out-ofbalance braking of the two wheels. An out-of
balance of up to 30 per cent was acceptable and it was to be noted that mis-matched brakes had less effect on the handling of a heavy vehicle than it had on a car.
The gross weight rating would be downrated if tyre rating did not conform to the gross rating. Downrating because the brakes could not cope with the higher load was not favoured by the MoT. In reply to a question by Mr. L. W. Hackerby of Chesterfield Corporation, Mr. Furness said that the fitting of softer springs (to improve the ride of a vehicle) would be acceptable if the stresses did not exceed the permitted maximum.
Referring to secondary brakes, Professor Hales doubted the necessity of fitting semitrailers with a secondary system and criticized the MoT for making it obligatory. Mr. Furness replied that when the C and U Regulations were reviewed in 1964/1965 the MoT did not "know enough". In due course the Ministry would know a lot more about vehicles (as was the case in Germany) and about what to expect. A student on the course pointed out that if a secondary system was fitted to the tractive unit only, the driver could test the system himself.
There had been very few appeals, Mr. Furness said, against decisions made at MoT testing stations, and these had in the main related to plating. Many inquiries concerned the braking of vehicles and had involved the staff in a lot of work. In due .course, when type approval had been introduced, it would only be necessary to deal with maintenance.
When Mr. Webber (who organized the course) asked for criticism of the course during the general discussion, Mr. R. Dawson of the Road Transport Industry Training Board suggested that a more thorough investigation should have been made to establish what kind of engineer would benefit the most from a course at a university. Of what use has the course been, he asked.
A number of students, including the author, paid tribute to the course and Mr. Webber said that consideration had been given to the potential of courses as a means of providing engineers with the opportunity to concentrate attention over a reasonable time on subjects that were part of his job but which he could not normally explore to the necessary extent because of the pressure of other work. A course could be a refresher course and at the same time be a retreat from normal day-today involvements. The biases of the representatives of industry who gave lectures to course students were neutralized by their number.
Equipment and vehicles seen during a tour of the university by the course students included a Commer van operated by the university noise group under a Design and Research Council contract for surveys of social noise problems. The group is headed by Dr. E. J. Richards, late of the University of Southampton noise section. Pilot surveys have been made of public response to noise produced by vehicles (notably lorries) on motorways in residential areas close to the motorways which has involved personal interviews with residents. So far it has been found that a continuous noise is less disturbing to the average person than a fluctuating noise. In a typical case, a person who lives near a motorway is apprehensive of the danger of -crashing lorries"; noise is a secondary consideration.