RK
Page 62
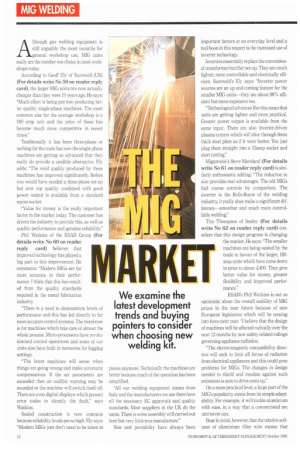
Page 63
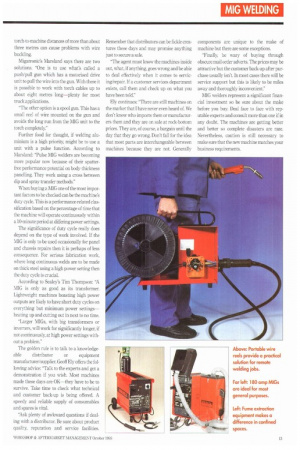
If you've noticed an error in this article please click here to report it so we can fix it.
We examine the latest development trends and buying pointers to consider when choosin9 new welding kit.
Although gas welding equipment is still arguably the most versatile for general workshop use, MIG units really are the number one choice in most workshops today.
According to Geoff Ely of Sureweld (UK) (For details write No 59 on reader reply card), the larger MIG units are now actually cheaper than they were 10 years ago. He says: "Much effort is being put into producing better quality single-phase machines. The most common size for the average workshop is a 180 amp unit and the price of these has become much more competitive in recent times."
Traditionally it has been three-phase or nothing for the trade but now the single-phase machines are getting so advanced that they really do provide a credible alternative. Ely adds: "The weld quality produced by these machines has improved significantly. Before you would have needed a three-phase set-up but now top quality combined with good power output is available from a standard mains socket.
"Value for money is the really important factor in the market today. The customer has driven the industry to provide this, as well as quality performance and genuine reliability."
Phil Watkins of the ESAB Group (For details write No 60 on reader reply card) believes that improved technology has played a big part in this improvement, He comments: "Modern MIGs are far more accurate in their performance. I think that this has resulted from the quality standards required in the metal fabrication industry.
"There is a need to demonstrate levels of performance and this has led directly to far more accurate control systems. The trend now is for machines which take care of almost the whole process. Micro-processors have revolutionised control operations and some of our units also have built in memories for logging settings.
"The latest machines will sense when things are going wrong and make automatic compensations. If the set parameters are exceeded then an audible warning may be sounded or the machine will switch itself off. There are even digital displays which present error codes to identify the fault," says Watkins.
Sealed construction is now common because reliability levels are so high. Ely says: "Modern 11/11Gs just don't need to be taken to pieces anymore. Technically the machines are better because much of the operation has been simplified.
All our welding equipment comes from Italy and the manufacturers we use there have all the necessary EC approvals and quality standards. Most suppliers in the UK do the same. There is some assembly still carried out here but very little true manufacture."
Size and portability have always been important factors at an everyday level and a real boon in this respect is the increased use of inverter technology.
Inverters essentially replace the conventional transformer/rectifier set-up. They are much lighter, more controllable and electrically efficient. Sureweld's Ely says: "Inverter power sources are an up and coming feature for the smaller MIG units—they are about 98% efficient but more expensive too.
"Technological advances like this mean that units are getting lighter and more practical. Greater power output is available from the same input. There are also inverter-driven plasma cutters which will slice through 6mm thick steel plate as if it were butter. You just plug them straight into a 13amp socket and start cutting," Migatronic's Steve Marsland (For details write No 61 on reader reply card) is similarly enthusiastic adding: "The reduction in size provides real advantages. The old MIGs had coarse controls by comparison. The inverter is the Rolls-Royce of the welding industry, it really does make a significant difference—smoother and much more controllable welding."
Tim Thompson of Sealey (For details write No 62 on reader reply card) considers that this design progress is changing the market. He says: "The smaller machines are being ousted by the trade in favour of the larger, 180amp units which have come down in price to about £400. They give better value for money, greater flexibility and improved performance."
ESAB's Phil Watkins is not so optimistic about the overall stability of MIG prices in the near future because of new European legislation which will be coming into force next year. "I believe that the design of machines will be affected radically over the next 12 months by new safety-related rulings governing appliance radiation.
The electro-magnetic compatibility directive will seek to limit all forms of radiation from electrical appliances and this could pose problems for MIGs. The changes in design needed to shield and insulate against such emissions is sure to drive costs up."
On a more practical level, a large part of the MIG's popularity stems from its simple adaptability. For example, it will tackle aluminium with ease, in a way that a conventional arc unit never can.
Bear in mind, however, that the relative softness of aluminium filler wire means that torch-to-machine distances of more than about three metres can cause problems with wire buckling.
Migatronic's Marsland says there are two solutions. "One is to use what's called a push/pull gun which has a motorised drive unit to pull the wire into the gun. With these it is possible to work with torch cables up to about eight metres long—plenty for most truck applications.
"The other option is a spool gun. This has a small reel of wire mounted on the gun and avoids the long run from the MIG unit to the torch completely."
Further food for thought, if welding aluminium is a high priority, might be to use a unit with a pulse function. According to Marsland: "Pulse MIG welders are becoming more popular now because of their spatterfree performance potential on body-thickness panelling. They work using a cross bet-ween dip and spray transfer methods."
When buying a MIG one of the most important factors to be checked can be the machine's duty cycle. This is a performance-related classification based on the percentage of time that the machine will operate continuously within a 10-minute period at differing power settings.
The significance of duty cycle really does depend on the type of work involved. If the MIG is only to be used occasionally for panel and chassis repairs then it is perhaps of less consequence. For serious fabrication work, where long continuous welds are to be made on thick steel using a high power setting then the duty cycle is cruciaL According to Sealev's Tim Thompson: "A MIG is only as good as its transformer. Lightweight machines boasting high power outputs are likely to have short duty cycles on everything but minimum power settings– heating up and cutting out in next to no timr.
"Larger MIGs, with big transformers or inverters, will work for significantly longer, if not continuously, at high power settings without a problem."
The golden rule is to talk to a knowledge able distributor or equipment manufacturer/supplier. Geoff Ely offers the following advice: "Talk to the experts and get a demonstration if you wish. Most machines made these days are OK—they have to be to survive. Take time to check what technical and customer back-up is being offered. A speedy and reliable supply of consumables and spares is vital.
"Ask plenty of awkward questions if dealing with a distributor. Be sure about product quality, reputation and service facilities. Remember that distributors can be fickle creatures these days and may promise anything just to secure a sale.
The agent must know the machines inside out, what, if anything, goes wrong and be able to deal effectively when it comes to servicing/repair. If a customer services department exists, call them and check up on what you have been told."
Ely continues: "There are still machines on the market that I have never even heard of. We don't know who imports them or manufacturers them and they are on sale at rock-bottom prices. They are, of course, a bargain until the day that they go wrong. Don't fall for the idea that most parts are interchangeable between machines because they are not. Generally components are unique to the make of machine but there are some exceptions.
"Finally, be wary of buying through obscure mail order adverts. The prices may be attractive but the customer back-up after purchase usually isn't. In most cases there will be service support but this is likely to be miles away and thoroughly inconvenient."
MIG welders represent a significant financial investment so be sure about the make before you buy. Deal face to face with reputable experts and consult more than one if in any doubt. The machines are getting better and better so complete disasters are rare. Nevertheless, caution is still necessary to make sure that the new machine matches your business requirements.