OFF-THE-PEG ON TO DELIVERIES
Page 50
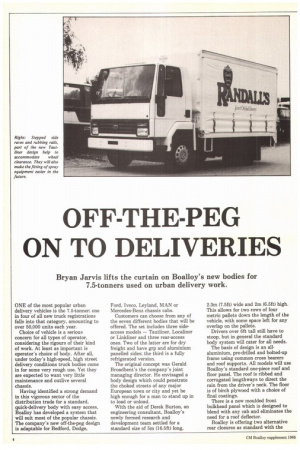
Page 51
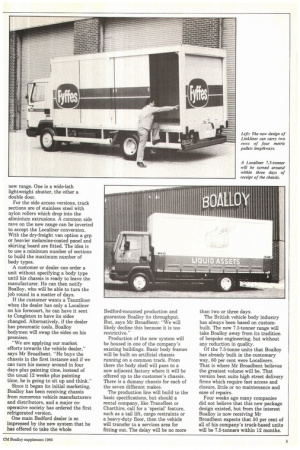
If you've noticed an error in this article please click here to report it so we can fix it.
Bryan Jarvis lifts the curtain on Boalloy's new bodies for 7.5-tonners used on urban delivery work.
ONE of the most popular urban delivery vehicles is the 7.5-tonner; one in four of all new truck registrations falls into that category, amounting to over 50,000 units each year.
Choice of vehicle is a serious concern for all types of operator, considering the rigours of their kind of work. At least as important is operator's choice of body. After all, under today's high-speed, high street delivery conditions truck bodies come in for some very rough use. Yet they are expected to want very little maintenance and outlive several chassis.
Having identified a strong demand in this vigorous sector of the distribution trade for a standard, quick-delivery body with easy access, Boalloy has developed a system that will suit most of the popular chassis. The company's new off-the-peg design is adaptable for Bedford, Dodge, Ford, Iveco, Leyland, MAN or Mercedes-Benz chassis cabs.
Customers can choose from any of the seven different bodies that will be offered. The set includes three sideaccess models — Tautliner, Localiner or Linkliner and three rear-access ones. Two of the latter are for dry freight and have grp and aluminium panelled sides; the third is a fully refrigerated version.
The original concept was Gerald Broadbent's the company's joint managing director. He envisaged a body design which could penetrate the choked streets of any major European town or city and yet be high enough for a man to stand up in to load or unload.
With the aid of Derek Burton, an engineering consultant, Boalloy's newly formed research and development team settled for a standard size of 5m (16.5ft) long, 2.3m (7.5ft) wide and 2m (6.5ft) high. This allows for two rows of four metric pallets down the length of the vehicle, with some space left for any overlap on the pallets.
Drivers over 6ft tall still have to stoop, but in general the standard body system will cater for all needs.
The basis of design is an allaluminium, pre-drilled and bolted-up frame using common cross bearers and roof supports. All models will use Boalloy's standard one-piece roof and floor panel. The roof is ribbed and corrugated lengthways to direct the rain from the driver's neck. The floor is of birch plywood with a choice of final coatings.
There is a new moulded front bulkhead panel which is designed to blend with any cab and eliminates the need for a roof deflector.
Boalloy is offering two alternative rear closures as standard with the new range. One is a wide-lath lightweight shutter, the other a double door.
For the side access versions, track sections are of stainless steel with nylon rollers which drop into the aliminium extrusions. A common side rave on the new range can be inverted to accept the Localiner conversion. With the dry-freight van option a grp or heavier melamine-coated panel and skirting board are fitted. The idea is to use a minimum number of sections to build the maximum number of body types.
A customer or dealer can order a unit without specifying a body type until his chassis is ready to leave the manufacturer. He can then notify Boalloy, who will be able to turn the job round in a matter of days.
If the customer wants a Tauntliner when the dealer has only a Localiner on his forecourt, he can have it sent to Congleton to have its sides changed. Alternatively, if the dealer has pneumatic tools, Boalloy bodymen will swap the sides on his premises.
"We are applying our market efforts towards the vehicle dealer," says Mr Broadbent. "He buys the chassis in the first instance and if we can turn his money around in four days plus painting time, instead of the usual 12 weeks plus painting time, he is going to sit up and think."
Since it began its initial marketing, Boalloy has been receiving chassis from numerous vehicle manufacturers and distributors, and a major cooperative society has ordered the first refrigerated version.
One main Bedford dealer is so impressed by the new system that he has offered to take the whole Bedford-mounted production and guarantee Boalloy its throughput. But, says Mr Broadbent: "We will likely decline this because it is too restrictive."
Production of the new system will be housed in one of the company's existing buildings. Basic body frames will be built on artificial chassis running on a common track. From there the body shell will pass to a new adjacent factory where it will be offered up to the customer's chassis. There is a dummy chassis for each of the seven different makes.
The production line will build to the basic specifications, but should a rental company, like Transfleet or Charthire, call for a 'special' feature, such as a tail lift, cargo restraints or a heavy-duty floor, then the vehicle will transfer to a services area for fitting out. The delay will be no more than two or three days.
The British vehicle body industry has always been based on custombuilt. The new 7.5-tonner range will take Boalloy away from its tradition of bespoke engineering, but without any reduction in quality.
Of the 7.5-tonne units that Boalloy has already built in the customary way, 60 per cent were Localiners. That is where Mr Broadbent believes the greatest volume will be. That version best suits high street delivery firms which require fast access and closure, little or no maintenance and ease of repairs.
Four weeks ago many companies did not believe that this new package design existed, but from the interest Boalloy is now receiving Mr Broadbent expects that 50 per cent of all of his company's truck-based units will be 7.5-tonners within 12 months.