LAYING DOWN THE LOAD
Page 67
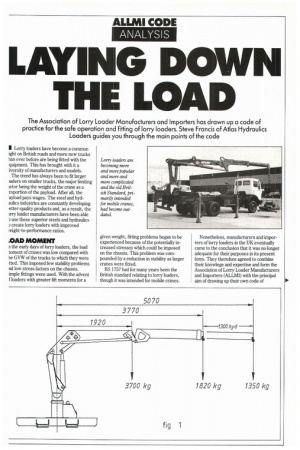
Page 68
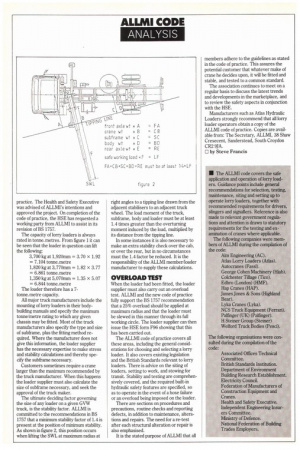
If you've noticed an error in this article please click here to report it so we can fix it.
The Association of Lorry Loader Manufacturers and Importers has drawn up a code of practice for the safe operation and fitting of lorry loaders. Steve Francis of Atlas Hydraulics Loaders guides you through the main points of the code
1 Lorry loaders have become a common ight on British roads and more new trucks han ever before are being fitted with the quipment. This has brought with it a iversity of manufacturers and models. The trend has always been to fit larger )aders on smaller trucks, the major limiting ictor being the weight of the crane as a roportion of the payload. After all, the ayload pays wages. The steel and hydaulics industries are constantly developing etter-quality products and, as a result, the wry loader manufacturers have been able ) use these superior steels and hydraulics ) create lorry loaders with improved 'eight-to-performance ratios.
,OACI MOMENT
a the early days of lorry loaders, the load aoment of cranes was low compared with ae GVW of the trucks to which they were tted. This imposed few stability problems nd low stress factors on the chassis. Imple fittings were used. With the advent f loaders with greater lift moments for a given weight, fitting problems began to be experienced because of the potentially increased stresses which could be imposed on the chassis. This problem was compounded by a reduction in stability as larger cranes were fitted.
BS 1757 had for many years been the British standard relating to lorry loaders, though it was intended for mobile cranes. Nonetheless, manufacturers and importers of lorry loaders in the UK eventually came to the conclusion that it was no longer adequate for their purposes in its present form. They therefore agreed to combine their knowlege and expertise and form the Association of Lorry Loader Manufacturers and Importers (ALLM1) with the principal aim of drawing up their own code of practice. The Health and Safety Executive was advised of ALLMI's intentions and approved the project. On completion of the code of practice, the HSE has requested a working party from ALLMI to assist in its revision of BS 1757.
The capacity of lorry loaders is always rated in tonne.metres. From figure 1 it can be seen that the loader in question can lift the following: 3, 700 kg at 1,920mm = 3.70 x 1.92 = 7.104 tonne. metre 1,820 kg at 3,770mm = 1.82 x 3.77 = 6.861 tonne. metre 1,350 kg at 5,070mm = 1.35 x 5.07 = 6.844 tonne. metre The loader therefore has a 7 tonne. metre capacity.
All major truck manufacturers include the mounting of lorry loaders in their bodybuilding manuals and specify the maximum tonne/metre rating to which any given chassis may be fitted. Most of the truck manufacturers also specify the type and size of subframe, plus the fitting method required. Where the manufacturer does not give this information, the loader supplier has the necessary expertise to make stress and stability calculations and thereby specify the subframe necessary.
Customers sometimes require a crane larger than the maximum recommended by the truck manufacturer. When this happens the loader supplier must also calculate the size of subframe necessary, and seek the approval of the truck maker.
The ultimate deciding factor governing the size of any loader on a given GVW truck, is the stability factor. ALLMI is committed to the recommendations in BS 1757 that a minimum stability factor of 1.4 is present at the position of minimum stability. As shown in figure 2, this position occurs when lifting the SWL at maximum radius at right angles to a tipping line drawn from the adjacent stabilisers to an adjacent truck wheel. The load moment of the truck, subframe, body and loader must be at least 1.4 times greater than the overturning moment induced by the load, multiplied by its distance from the tipping line.
In some instances it is also necessary to make an extra stability check over the cab, or over the rear, but in no circumstances must the 1.4 factor be reduced. It is the responsibility of the ALLMI member/loader manufacturer to supply these calculations.
OVERLOAD TEST
When the loader had been fitted, the loader supplier must also carry out an overload test. ALLMI and the new code of practice fully support the BS 1757 recommendation that a 25% overload should be applied at maximum radius and that the loader must be slewed in this manner through its full working circle. The loader supplier can then issue the HSE form F96 showing that this has been carried out.
The ALLMI code of practice covers all these areas, including the general considerations for choosing and selecting a lorry loader. It also covers existing legislation and the British Standards relevant to lorry loaders. There is advice on the siting of loaders, setting to work, and stowing for transit. Stability and testing are comprehensively covered, and the required built-in hydraulic safety features are specified, so as to operate in the event of a hose failure or an overload being imposed on the loader.
There are sections on procedures and precautions, routine checks and reporting defects, in addition to maintenance, alterations and repairs. The need for a re-test after each structural alteration or repair is also emphasised.
It is the stated purpose of ALLMI that all members adhere to the guidelines as stated in the code of practice. This assures the potential customer that whatever make of crane he decides upon, it will be fitted and stable, and tested to a common standard.
The association continues to meet on a regular basis to discuss the latest trends and developments in the marketplace, and to review the safety aspects in conjunction with the HSE.
Manufacturers such as Atlas Hydraulic Loaders strongly recommend that all lorry loader operators obtain a copy of the ALLMI code of practice. Copies are available from: The Secretary, ALLMI, 38 Shaw Cresecent, Sanderstead, South Croydon CR2 9JA.
0 by Steve Francis