WIDER STILL AND WIDER
Page 44
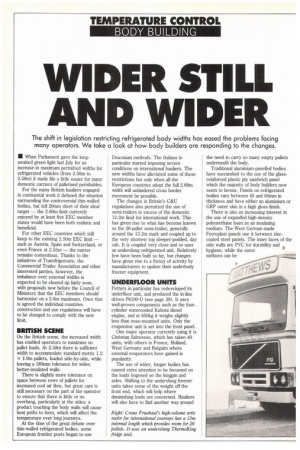
Page 45
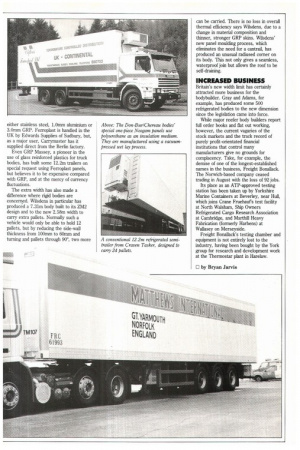
If you've noticed an error in this article please click here to report it so we can fix it.
The shift in legislation restricting refrigerated body widths has eased the problems facing many operators. We take a look at how body builders are responding to the changes.
• When Parliament gave the longawaited green light last July for an increase in maximum permitted widths for refrigerated vehicles (from 2.50m to 2.58m) it made life a little easier for many domestic carriers of palletised perishables.
For the many British hauliers engaged in continental work it defused the situation surrounding the controversial thin-walled bodies, but fell 20nun short of their ideal target — the 2.60m limit currently enjoyed by at least five EEC member states would have been both realistic and beneficial.
For other EEC countries which still keep to the existing 2.50m EEC limit — such as Austria, Spain and Switzerland, or even France at 2.55m — the matter remains contentious. Thanks to the initiatives of Transfrigoroute, the Commercial Trailer Association and other interested parties, however, the imbalance over external widths is expected to be cleared up fairly soon, with proposals now before the Council of Ministers that the EEC members should harmonise on a 2.6m maximum. Once that is agreed the individual countries construction and use regulations will have to be changed to comply with the new limit.
BRITISH SCENE
On the British scene, the increased width has enabled operators to maximise on pallet loads. At 2.58m there is sufficient width to accommodate standard metric 1.2 x 1.0m pallets, loaded side-by-side, while leaving a 180mm tolerance for wider, better-insulated walls.
There is slightly more tolerance on space between rows of pallets for increased cool air flow, but great care is still necessary on the part of the operator to ensure that there is little or no overhang, particularly at the sides: a product touching the body walls will cause heat paths to form, which will affect the temperature over long journeys.
At the time of the great debate over thin-walled refrigerated bodies, some European frontier posts began to use Draconian methods. The Italians in particular started imposing severe conditions on international hauliers. The new widths have alleviated some of these restrictions but only when all the European countries adopt the full 2.60m width will unhindered cross border movement be possible.
The changes in Britain's C&U regulations also permitted the use of semi-trailers in excess of the domestic 12.2m limit for international work. This has given rise to what has become known as the 26-pallet semi-trailer, generally around the 13.2m mark and coupled up to the very shortest top sleeper-podded, day cab. It is coupled very close and so uses an underslung refrigerated unit. Relatively few have been built so far, but changes have given rise to a frenzy of activity by manufacturers to update their underbody freezer equipment.
UNDERFLOOR UNITS
Petters in particular has redeveloped its underfloor unit, and produced the in-line driven P6100-U (see page 39). It uses well-proven components such as the four-. cylinder watercooled Kubota diesel engine, and at 650kg it weighs slightly less than nose-mounted units. Only the evaporator unit is set into the front panel.
One major operator currently using it is Christian Salvesson, which has taken 40 units, with others in France, Holland, West Germany and Belguim where external evaporators have gained in popularity.
The use of wider, longer bodies has caused extra attention to be focussed on the loads imposed on the kingpin and axles. Shifting to the underslung freezer units takes some of the weight off the front end, which will help where diminishing loads are concerned. Hauliers will also have to find another way around the need to carry so many empty pallets underneath the body.
Traditional aluminium-panelled bodies have succumbed to the use of the glassreinforced plastic ply sandwich panel which the majority of body builders now seem to favour. Panels on refrigerated bodies vary between 45 and 60nun in thickness and have either an aluminium or GRP outer skin in a high gloss finish.
There is also an increasing interest in the use of expanded high-density polyurethane foam as an insulating medium. The West German-made Ferroplast panels use it between zinccoated steel panels. The inner faces of the side walls are PVC for durability and hygiene, while the outer surfaces can be either stainless steel, 1.0mm aluminium or 3.0mm GRP. Ferroplast is handled in the UK by Edwards Supplies of Sudbury, but, as a major user, Carrymaster has it supplied direct from the Berlin factory.
Even GRP Massey, a pioneer in the use of glass reinforced plastics for truck bodies, has built some 12.2m trailers on special request using Ferroplast panels, but believes it to be expensive compared with GRP, and at the mercy of currency fluctuations.
The extra width has also made a difference where rigid bodies are concerned. Wilsdens in particular has produced a 7.31m body built to its ZM2 design and to the new 2.58m width to carry extra pallets. Normally such a vehicle would only be able to hold 12 pallets, but by reducing the side-wall thickness from 100mm to 60mm and turning and pallets through 90°, two more can be carried. There is no loss in overall thermal efficiency says Wilsdens, due to a change in material composition and thinner, stronger GRP skins. Wilsdens' new panel moulding process, which eliminates the need for a cantrail, has produced an unusual radiused corner on its body. This not only gives a seamless, waterproof join but allows the roof to be self-draining.
INCREASED BUSINESS
Britain's new width limit has certainly attracted more business for the bodybuilder. Gray and Adams, for example, has produced some 500 refrigerated bodies to the new dimension since the legislation came into force.
While major reefer body builders report full order books and flat out working, however, the current vagaries of the stock markets and the track record of purely profit-orientated financial institutions that control many manufacturers give no grounds for complacency. Take, for example, the demise of one of the longest-established names in the business, Freight Bonallack. The Norwich-based company ceased trading in August with the loss of 92 jobs.
Its place as an ATP-approved testing station has been taken up by Yorkshire Marine Containers at Beverley, near Hull, which joins Crane Fruehauf's test facility at North Walsham, Ship Owners Refrigerated Cargo Research Association at Cambridge, and Marthill Heavy Fabrication (formerly Harbens) at Wallasey on Merseyside.
Freight Bonallack's testing chamber and equipment is not entirely lost to the industry, having been bought by the York group for research and development work at the Thermostar plant in Harelaw.
0 by Bryan Jarvis