Brake systems for the future
Page 31
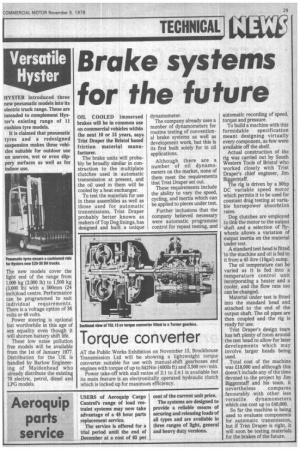
If you've noticed an error in this article please click here to report it so we can fix it.
OIL COOLED immersed brakes will be in common use on commercial vehicles within the next 10 or 15 years, says Trist Draper the Bristol based friction material manufacturer.
The brake units will probably be broadly similar in construction to the multiplate clutches used in automatic transmission at present, and the oil used in them will be cooled by a heat exchanger.
To test the materials for use in these assemblies as well as those used for automatic transmissions, Trist Draper probably better known as makers of Top Dog linings, has designed and built a unique dynamometer.
The company already uses a number of dynamometers for routine testing of conventional brake systems as well as development work, but this is its first built solely for in oil applications.
Although there are a number of oil dynamometers on the market, none of them meet the requirements that Trist Draper set out.
These requirements include the ability to vary the speed, cycling, and inertia which can be applied to pieces under test.
Further inclusions that the company believed necessary were automatic programme control for repeat testing, and automatic recording of speed, torque and pressure.
To build a machine with this formidable specification meant designing virtually every component, as few were available off the shelf.
Actual construction of the rig was carried out by South Western Tools of Bristol who worked closely with Trist Draper's chief engineer, Jim Biggerstaff.
The rig is driven by a 50hp DC variable speed motor which permits it to be used for constant drag testing at variable horsepower absorbtion rates.
Dog clutches are employed to link the motor to the output shaft and a selection of flywheels allows a variation of output inertia on the material under test.
A standard test head is fitted to the machine and oil is fed to it from a 45 litre (10gal) sump.
The oil temperature can be varied as it is fed into a temperature control unit incorporating a heater and a cooler, and the flow rate too can be changed.
Material under test is fitted into the standard head and attached to the end of the output shaft. The oil pipes are then coupled and the rig is ready for use.
Trist Draper's design team has left plenty of room around the test head to allow for later developments which may involve larger heads being used.
Total cost of the machine was £18,000 and although this doesn't include any of the time devoted to the project by Jim Biggerstaff and his team, it nevertheless compares favourably with other less versatile dynamometers which can cost up to E40,000.
So far the machine is being used to evaluate components for automatic transmission, but if Trist Draper is right, it will soon be testing materials for the brakes of the future.