TECHNITOPICS
Page 57
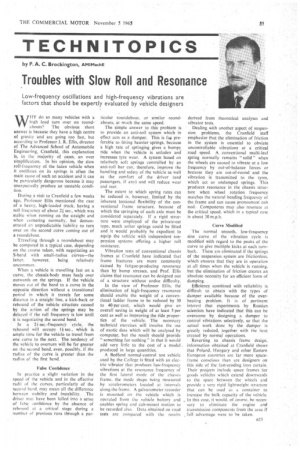
If you've noticed an error in this article please click here to report it so we can fix it.
by P. A. C. Brockington, AM IMechE
Troubles with Slow Roll and Resonance
Low-frequency oscillations and high-frequency vibrations are factors that should be expertly evaluated by vehicle designers
WHY do so many vehicles with a high load turn over on roundabouts? The obvious short answer is because they have a high centre of gravity and are going too fast, but according to Professor J. R. Ellis, director of The Advanced School of Automobile Engineering, Cranfield, this explanation is, in the majority of eases, an over simplification. In his opinion, the slow roll-frequency of the laden vehicle when it oscillates on its springs is often the main cause of such an accident and it can be particularly dangerous because it may unexpectedly produce an unstable condition.
During a visit to Cranfield a few weeks ago, Professor Ellis mentioned the case of a heavy, high-loaded truck, having a roll frequency of about 2.1 sec., which was stable when running on the straight and when cornering normally, but demonstrated an unpredictable liability to turn over on he second curve coming out of a roundabout.
Travelling through a roundabout may be compared in a typical case, depending on the course taken, with negotiating an S-bend with small-radius curves—the latter. however, being relatively uncommon.
When a vehicle is travelling fast on a curve, the chassis-body mass heels over outwards on the springs. If the vehicle moves out of the bend to a curve in the opposite direction without a transitional period in which it travels for some distance in a straight line, a kick-back or rebound of the vehicle structure caused by the action of the springs may be delayed if the roll frequency is low Until it is negotiating the second bend. . . In a 24: sec.-frequency cycle, the rebound will occupy. 11sec., which is ample time for the vehicle to travel from one curve to the next. The tendency of the vehicle to overturn will-be far greater on the second bend, even, possibly, if the radius of the Curve is greater than the radius of the first bend.
False Confidence
In practice a slight variation in the speed of the vehicle and in the effective radii of the curves, particularly of the second bend. may mean all the difference between stability and instability. The driver may have been lulled into a sense of false confidence by the absence of rebound at a critical stage during a number of previous runs through a par
ticular roundabout, or similar roundabouts, at much the same speed.
The simple answer to this problem is to provide an anti-roll system which in effect acts as a damper. This is fa s preferable to fitting heavier springs, because a high rate of springing gives a bumpy ride when the vehicle is unladen and increases tyre wear. A system based on relatively soft springs controlled by an anti-roll bar can, therefore, improve the handling and safety of. the vehicle as well as the comfort of the driver (and passengers, if any) and will reduce wear and tear.
The extent to which spring rates can be reduced is, however, limited by the inherent torsional flexibility of the conventional frame structure, because of which the springing of each axle must be considered separately. If a rigid structure were employed of the private-car type, much softer springs could be fitted and it would probably be expedient to equip the vehicle with independent suspension systems offering a higher roll resistance.
Vibration tests of conventional chassis frames at Cranfield have indicated that frame fractures are more commonly caused by fatigue-producing resonance than by bump stresses, and Prof. Ellis claims that resonance can he designed out of a structure without undue difficulty.
In the view of Professor Ellis, the elimination of high-frequency resonance should enable the weight of a conventional ladder frame to be reduced by 30 to 40 per cent, which would give an overall saving in weight of at least 5 per cent as well as improving the ride properties of the vehicle. The necessary technical exercises , will involve the use of exotic data which will be analysed by computer, but the result should provide "something for nothing ' in that it would add -very little to the cost of a model . produced in large quantities.
A Bedford normal-control test vehicle used by the College is fitted with an electric vibrator that produces 4w-frequency vibrations at the resonance frequency of the first lateral mode of the chassis frame, the mode shape being measured by accelerometers located at intervals along the frame. A galvanometer recorder is mounted on the vehicle which is operated from the vehicle battery and enables spring and cab-mount motion to be recorded also. Data obtained on road tests are compared with the results derived from theoretical analyses and vibrator tests.
Dealing with another aspect of suspension problems, the Cranfield Staff emphasize that the elimination of friction in the system is essential to obviate uncontrollable vibrations at a critical road speed. A. conventional multi-leaf spring normally remains " solid " when the wheels are caused to vibrate at a low frequency by out-of-balance forces or because they are out-of-round and the vibration is transmitted to the tyres, which act as undamped springs. This produces resonance in the chassis structure when wheel rotation frequency matches the natural bending frequency of the. frame and can cause pronounced cab nod. Components may also resonate at the critical speed. which in a typical case is about 30 m.p.h.
Curve Modified
The normal smooth, low-frequency sine curve of the vibration cycle is modified with regard to the peaks of the curve to give multiple kicks at each-turnback. These are eliminated if the springs of the suspension. system are frictionless, which ensures that they are in operation at all times when the vehicle is running, but the elimination of friction creates an absolute necessity for an efficient form of damping. ,
Efficiency combined with reliability is difficult to obtain with the types of damper available because of the overheating Problem. It is of pertinent interest that experiments by Russian scientists have indicated that this can be overcome by designing a damper to control vibrations selectively, so that the actual work done. by the damper is greatly reduced, together with the heat created by normal operations.
Reverting to chassis frame design. information obtained at Cranfield shows that Poland, Hungary and other Eastern European countries are far more spaceframe conscious than are designers on this side of the fast-eroding iron curtain. Their projects include space frames for goods vehicles which extend downwards to the space between the wheels and provide a very rigid lightweight structure that can be used as. a container to increase the bulk capacity of the vehicle. In this case, it would, of course, he necessary to eliminate the engine and transmission components from the area if full advantage were to 'he taken.