Weight Saving I ; Money in the Operator's Pocket
Page 92
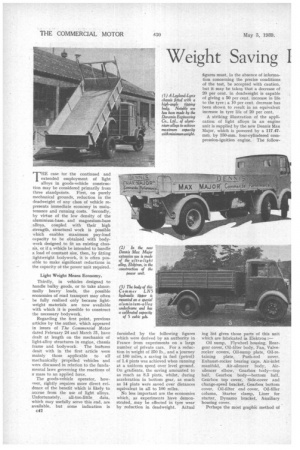
Page 93
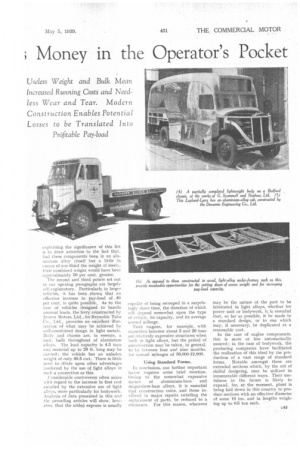
If you've noticed an error in this article please click here to report it so we can fix it.
Useless Weight and Bulk Mean Increased Running Costs and Needless Wear and Tear. Modern Construction Enables Potential Losses to be Translated Into
Profitable Pay-load
THE case or the continued and extended employment of light alloys in goods-vehicle construction may be considered primarily from three standpoints. First, on purely mechanical grounds, reduction in the deadweight of any class of vehicle represents immediate economy in maintenance and running costs. Secondly, by virtue of the low density of the aluminium-base and magnesium-base alloys, coupled with their high strength, structural work is possible which enables maximum pay-load capacity to be obtained with bodywork designed to fit an existing chassis, or if a vehicle be intended to handle a load of constant size, then, by fitting lightweight bodywork, it is often possible to make significant reductions in the capacity of the power unit required.
Light Weight Means Economy.
Thirdly, in vehicles designed to handle bulky goods, or to take abnormally heavy loads, the possible economies of road transport may often be fully realized only because lightweight materials are now available with which it is possible to construct the necessary bodywork.
Regarding the first point, previous articles by the author, which appeared in issues of The Commercial Motor dated February 24 and March 31, have dealt at length on the mechanics of light-alloy structures in engine, chassis frame and bodywork. The features dealt with in the first article were mainly those applicable to all mechanically propelled vehicles and were discussed in relation to the fundamental laws governing the reactions of a mass to an applied force.
The goods-vehicle operator, howwer, rightly requires more direct evidence of the benefit which is likely to accrue from the use of light alloys. Unfortunately, all-too-little data, which may usefully serve this end, are available, but some indication is c42
furnished by the following figures which were derived by an authority in France from experiments on a large number of private cars. For a reduction in weight of 250 lb., and a journey of 100 miles, a saving in fuel (petrol) of 1.4 pints was achieved when running at a uniform speed over level ground. On gradients, the saving amounted to as much as 8.5 pints, whilst, during acceleration in bottom gear, as much as 14 pints were saved over distances equivalent in all to 100 miles.
No less important are the economies which, as experiments have demonstrated, may be effected in tyre wear by reduction in deadweight. Actual figures must, in the absence of information concerning the precise conditions of the test, be accepted with caution, but it may be taken that a decrease of 20 per cent, in deadweight is capable of giving a 50 per cent. increase in life to the tyre ; a 10 per cent, decrease has been shown to result in an equivalent increase in tyre life of 20 per cent.
A striking illustration of the application of light alloys in an engine unit is supplied by the new Dennis Max Major, which is powered by a 117.47mm. by 150-mm. four-cylindered compression-ignition engine. The follow ing list gives those parts of this unit which are fabricated in Elektron :— Oil sump, Flywheel housing, Reargear cover, Oil-filter body, Fan, Valverocker covers, Oil-sump plate, Oil-retaining plate, Push-rod cover, Exhaust-rocker bearing caps, Air-inlet manifold, Air-silencer body, Airsilencer elbow, Gearbox body—top half, Gearbox body—bottom half, Gearbox top cover, Side-cover and change-speed bracket. Gearbox bottom cover, Oil-filter end cover, Oil-filler column, Starter clamp, Liner for starter, Dynamo bracket, Auxiliary housing cover.
Perhaps the most graphic method of explaining the significance of this list is to draw attention to the fact that, had these components been in an aluminium alloy (itself but a little' in excess of one-third the weight of steel), their combined weight would have been . approximately 50 per cent. greater.
.1-tu, second and third points set out in our opening paragraphs are largely self explanatory. Particularly in larger . vehicles, it has been shown that an effective increase in pay-load of :40 per cent. is quite possible.. As to the case of vehicles designed to handle unusual loads, the lorry constructed by Jensen Motors. Ltd., for Reynolds Tube Co., Ltd., provides an excellent illustration of what may be achieved by well-considered design in light metals. Body and chassis are, in essence, a unit, built throughout of aluminium alloys. The load capacity is 4.5 tons and material up to 29 ft. long may be carried ; the vehicle has an unladen weight of only 40.5 cwt. There is little need to dilate upon other advantages conferred by the use of light alloys in such a connection as this.
Considerable controversy often arises tt ith regard to the increase in first cost entailed by the extensive use of light alloys, more particularly for bodywork. Analysis of data presented in this and the preceding articles will show, however, that the added expense is usually capable of being recouped in a surprisingly short time, the duration of which will depend somewhat upon the type of vehicle, its capacity, and its average annual mileage.
Tank wagons, for example, with capacities between about 5 and 20 tons are relatively expensive structures when built in light alloys, but the period of amortization may be taken, in general, to be between four and nine months, for annual mileages of 50,000-12,000.
Using Standard Forms.
In conclusion, one further important factor requires some brief mention. Owing to the somewhat expensive nature of aluminium-base and magnesium-base alloys, it is essential that construction costs, and those invillved in major repairs entailing the replacement of parts, be reduced to a minimum. For this reason, whatever may he the nature of the part to be fabricated in light alloys, whether for power unit or bodywork, it is essential that, so far as possible, it he made to a standard design, or to one which may, if necessary, be duplicated at a reasonable cost.
In the case of engine components, this is more or less automatically assured; in the case of bodywork, the producing companies have facilitated the realization of this ideal by the production of a vast range of standard forms. Notable amongst these are extruded sections which, by the aid of skilful designing, may be utilized in innumerable different ways. Their usefulness in the future is likely to expand, for, at the moment, plant is being laid down in this country toTroduce sections with an effective diameter of some 16 ins, and in lengths weighing up to 0.5 ton each.