Modern Metallurgy Makes Goods Vehicles Pay
Page 115
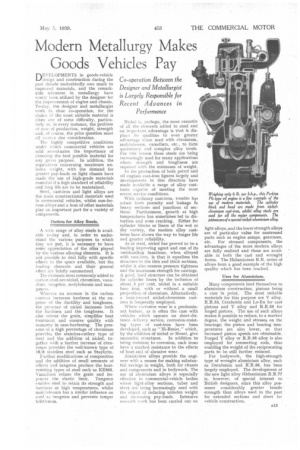
If you've noticed an error in this article please click here to report it so we can fix it.
Co-operation Between the Designer and Metallurgist is Largely Responsible for Recent Advances in
Performance
riE E ORM EN T S in goods-vehicle L./design and construction during the past decade undoubtedly owe much to improved materials, and the remarkable advances in metallurgy have wisely been utilized by the designer for the implevement of engine and chassis. To-day, the designer and metallurgist work in close co-operation, for the choice of the most suitable material is often one of some difficulty, particulady as, in every instance, the problem of ease of production, weight, strength and, of course, the price question must all receite due consideration.
The highly competitive conditions under which commercial vehicles are sold accentuates the importance of choosing the best possible material for any given purpose. In addition, the regulations concerning maximum unladen weight, with the demand for greater pay-loads on light chassis have made the use of high-grade materials essential if a high standard of reliability and long life are to be maintained.
Steel, cast-iron and light alloys are the main constructional materials used in commercial vehicles, whilst non-ferrous alloys and a host of other materials play an important part for a variety of components .
Outlets for Alloy Steels.
A wide range of alloy steels is available to-day and, in order to understand the various purposes to which they are put, it is necessary to have some appreciation of the roles played by the various alloying elements. It is not possible to deal fully with specific effects in the space available, but the leading elements and their general effect are briefly summarized.
The elements most commonly added to carbon steel are nick-el, chromium, vanadium, tungsten, molybdenum and manganese.
Whereas an increase in the carbon content increases hardness at the expense of the ductility and toughness, the presence of nickel increases both the lia,rdness and the toughness. It also refines the grain, simplifies heat treatment and ensuresquality with economy in case-hardening: The presence of a high percentage of chromium provides the stainless-cutlery type of steel and the addition of nickel, together with a further increase of chromium provides the well-known type of 18/8 stainless steel such as Staybrite.
Further modifications of composition and the addition of small amounts of silicon and tungsten produce the heatresisting types of steel such as KE9135. Vanadium refines the grain and improves the elastic limit. Tungsten enables steel to retain its strength and hardness at high temperatures, whilst molybdenum has a similar influence on steel as tungsten and prevents temper brittleness,
Nickel is, perhaps, the most versatile of all the elements added to steel and an important advantage is that it displays its qualities to even greater advantage when used with chromium, molybdenum, vanadium, etc., to form quaternary and complex alloy -steels. For this reason these steels are being increasingly used for many applications where strength and toughness are required with the minimum of weight.
In the production of both petrol and oil engines cast-iron figures largely and developments in this direction have made available a range of alloy castirons capable of meeting the most severe service conditions, With ordinary cast-iron, trouble has arisen from porosity and leakage in heavy sections and junctions of sections. Furthermore, growth at high temperatures has sometimes' led to distortion and even cracking. Either for cylinder blocks or liners of the wet or dry variety, the modern alloy castirons have shown the way to longer life and greater reliability.
As in steel, nickel has proved to be a leading improving agent and one of its outstamding functions, when alloyed with cast-iron, is that it equalizes the structure in the thin and thick sections, whilst it also ensures pressure tightness and the maximum strength for castings. A good, hard structure can be obtained for cylinder liners by the inclusion of about 5 per cent, nickel in a suitable base iron, with or without a small proportion of chromium. Alternatively, a heat-treated nickel-chromium castiron is frequently employed.
Where corrosive wear is a predominant feature, as is often the case with vehicles which operate on short-distance delivery service, corrosion-resisting types of cast-iron have been developed, such as "Ni-Resist," which, by the addition of nickel or Monel, give austenitic structures. In addition to being resistant to corrosion, such irons have a marked resistance to the effects of heat and of abrasive wear.
Aluminium alloys provide the engineer with a means for making substantial savings in 'weight, both for chassis and components and in bodywork. The use of aluminium alloys is especially effective in commercial-vehicle bodies where light-alloy sections, tubes and sheet are being increasingly used with the object of reducing unladen weight and increasing pay-loads. Intensive research work has been carried out on
light alloys, and the lowerstrength alloys are of particular value for unstressed parts such as engine sumps, gearcases, etc. For stressed components, the advantages of the more modern alloys are fully nalized and these are available in both the caSt and wrought forms. The Ididuminium R.R. series of alloys form a good example of the high quality which has been reached.
Uses for Aluminium.
Many components lend themselves to aluminium construction, pistons being a case in point. The most suitable materials for this purpose are Y alloy, R.R.53, Ceralumin and Lo-Ex for cast pistons and 'Y alloy and R.R.59 for forged pistons. The use of such alloys makes it possible to reduce, to a marked degree, the weight and stresses on the bearings; the piston and bearing temperatures are also lower, so that increased piston speeds are obtainable. Forged Y alloy or R.R.56 alloy is also employed for connecting rods, thus enabling the weight of the reciprocating parts to be still further reduced.
For bodywork, the high-strength type of wrought aluminium alloy, such as Duralurnin and Int.56, has been largely employed. The development of the new light alloy Eliduminium R.R.77 is, however, of special interest to British designers, since this alloy possesses considerably greater tensile strength than alloys used in the past for extruded sections and sheet for vehicle construction.