S eddon Atkinsons have a reputation for being good fleet vehicles
Page 95
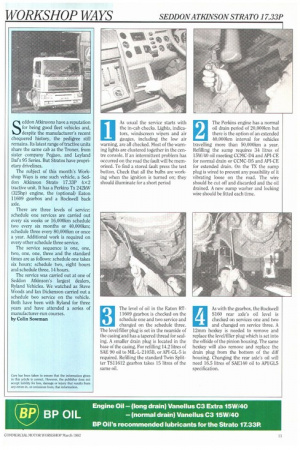
Page 96
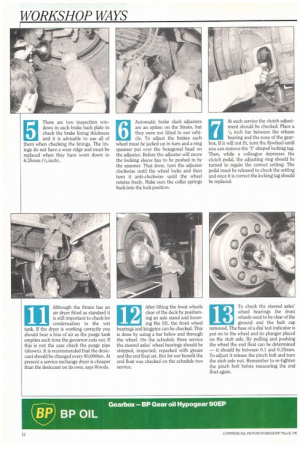
Page 97
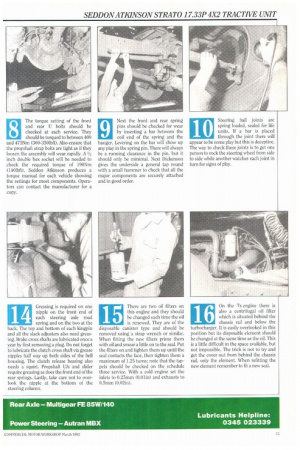
Page 98
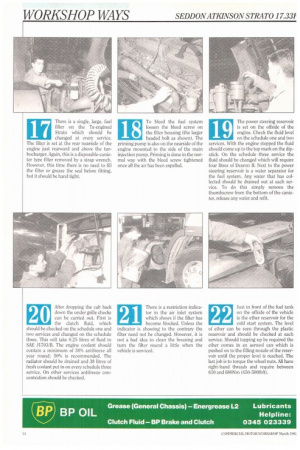
If you've noticed an error in this article please click here to report it so we can fix it.
and, despite the manufacturer's recent chequered history, the pedigree still remains. Its latest range of tractive units share the same cab as the Troner, from sister company Pegaso, and Leyland Dars 95 Series. But Stratos have proprietary drivelines.
The subject of this month's Workshop Ways is one such vehicle, a Seddon Atkinson Strata 17.33P 4 x 2 tractive unit. It has a Perkins Tx 242kW (325hp) engine, the (optional) Eaton 11609 gearbox and a Rockwell back axle.
There are three levels of service: schedule one services are carried out every six weeks or 16,000km schedule two every six months or 40,000km; schedule three every 80,000km or once a year. Additional work is required on every other schedule three service.
The service sequence is one, one, two, one, one, three and the standard times are as follows: schedule one takes six hours: schedule two, eight hours and schedule three, 14 hours.
The service was carried out at one of Seddon Atkinson's largest dealers, Ryland Vehicles. We watched as Steve Woods and Ian Dickenson carried out a schedule two service on the vehicle. Both have been with Ryland for three years and have attended a series of manufacturer-run courses.
by Colin Sowman
As usual the service starts with the in-cab checks. Lights, indicators, windscreen wipers and air gauges, including the low air warning, are all checked. Most of the warning lights are clustered together in the centre console. If an intermittent problem has occurred on the road the fault will be memorised. To find a stored fault press the test button. Check that all the bulbs are working when the ignition is turned on; they should illuminate for a short period
1
The Perkins engine has a normal oil drain period of 20,000km but there is the option of an extended 40,000km interval for vehicles travelling more than 50,000km a year. Refilling the sump requires 34 litres of 15W/40 oil meeting CCMC-D4 and API-CE for normal drain or CCMC-D5 and API-CE for extended drain. On the TX the sump plug is wired to prevent any possibility of it vibrating loose on the road. The wire should be cut off and discarded and the oil drained. A new sump washer and locking wire should be fitted each time.
The level of oil in the Eaton RT11609 gearbox is checked on the schedule one and two service and changed on the schedule three. The leveVfiller plug is set in the nearside of the casing and has a tapered thread for sealing. A smaller drain plug is located in the base of the casing. For refilling 14.2 litres of SAE 90 oil to MIL-L-2105B, or API-GL-5 is required. Refilling the standard Twin Splitter TS11612 gearbox takes 15 litres of the same oil.
3
As with the gearbox, the Rockwell S160 rear axle's oil level is checked on services one and two and changed on service three. A 12mm hexkey is needed to remove and replace the leveVfiller plug which is set into the offside of the pinion housing. The same hexkey will also remove and replace the drain plug from the bottom of the diff housing. Changing the rear axle's oil will need 16.5 litres of SAE140 oil to APVGL5 specification.
There are two inspection windows in each brake back plate to check the brake lining thickness and it is advisable to use all of them when checking the linings. The linings do not have a wear ridge and must be replaced when they have worn down to 6.35mm (3/4 inch).
Automatic brake slack adjusters are an option on the Strato, but they were not fitted to our vehicle. To adjust the brakes each wheel must be jacked up in turn and a ring spanner put over the hexagonal head on the adjuster. Before the adjuster will move the locking sleeve has to be pushed in by the spanner. That done, turn the adjuster clockwise until the wheel locks and then turn it anti-clockwise until the wheel rotates freely. Make sure the collar springs back into the lock position. At each service the clutch adjustment should be checked. Place a 1/2 inch bar between the release bearing and the nose of the gearbox. If it will not fit, turn the flywheel until you can remove the 'Y'-shaped locking tag. Then, while a colleague depresses the clutch pedal, the adjusting ring should be turned to regain the correct setting. The pedal must be released to check the setting and once it is correct the locking tag should be replaced.
The torque setting of the front and rear U bolts should be checked at each service. They should be torqued to between 400 and 475Nrn (300-350ibfl). Also ensure that the propshaft strap bolts are tighl as if they loosen the assembly will wear rapidly. A 1/2 inch double hex socket will be needed to check the required torque of 190Nm (1401bft). Seddon Atkinson produces a torque manual for each vehicle showing the settings for most components. Operators can contact the manufacturer for a copy.
Next the front and rear spring pins should be checked for wear by inserting a bar between the coil end of the spring and the hanger. Levering on the bar will show up any play in the spring pin. There will always be a running clearance in the pin, but it should only be minimal. Next Dickenson gives the underside a general tap round with a small hammer to check that all the major components are securely attached and in good order.
10 Steering ball joints are spring loaded, sealed for life
units. If a bar is placed through the joint there will appear to be some play but this is deceptive. The way to check these joints is to get one person to rock the steering wheel from side to side while another watches each joint in turn for signs of play.
11 Although the Strato has an air dryer fitted as standard it
is still important to check for condensation in the wet tank. If the dryer is working correctly you should hear a hiss of air as the purge tank empties each time the governor cuts out. If this is not the case check the purge pipe (shown). It is recommended that the desiccant should be changed every 80,000km. At present a service exchange dryer is cheaper than the desiccant on its own, says Woods.
12 After lifting the front wheels
clear of the deck by position ing an axle stand and lower ing the lift, the front wheel bearings and kingpins can be checked. This is done by using a bar below and through the wheel. On the schedule three service the steered axles' wheel bearings should be stripped, inspected, repacked with grease and the end float set. But for our benefit the end float was checked on the schedule two service. To check the steered axles' wheel bearings the front wheels need to be clear of the ground and the hub cap removed. The base of a dial test indicator is put on to the wheel and its plunger placed on the stub axle. By pulling and pushing the wheel the end float can be determined — it should be between 0.1 and 0.15mm. To adjust it release the pinch bolt and turn the stub axle nut.. Remember to re-tighten the pinch bolt before measuring the end float again.
13 14 Greasing is required on one
nipple on the front end of each steering axle road spring and on the two at the back. The top and bottom of each kingpin and all the slack adjusters also need greasing. Brake cross shafts are lubricated once a year by first removing a plug. Do not forget to lubricate the clutch cross shaft via grease nipples half way up both sides of the bell housing. The clutch release bearing also needs a squirt. Propshaft Ws and slider require greasing as does the front end of the rear springs. Lastly, take care not lo overlook the nipple at the bottom of the steering column.
flj There are two oil filters on
this engine and they should be changed each time the oil is renewed. They are of the disposable canister type and should be removed using a strap wrench or similar. When fitting the new filters prime them with oil and smear a little on to the seal. Put the filters on and tighten them up until the seal contacts the face, then tighten them a maximum of 1.25 turns; note that the tappets should be checked on the schedule three service. With a cold engine set the inlets to 0.25mm (0.01in) and exhausts to 0.5mm (0.02in).
16 On the Tx engine there is
also a centrifugal oil filler which is situated behind the
chassis rail and below the turbocharger. IL is easily overlooked in this position but its disposable element should be changed at the same time as the oil. This is a little difficult in the space available, but not impossible. The trick is not to try and get the cover out from behind the chassis rail, only the element. When refilling the new element remember to fit a new seal. 17 There is a single, large, fue
filter on the Tx-engined Strato which should be changed at every service. The filter is set at the rear nearside of the engine just rearward and above the turbocharger. Again, this is a disposable-canister type filter removed by a strap wrench. However, this time there is no need to fill the filter or grease the seal before fitting, but it should be hand Light.
18 To bleed the fuel system loosen the bleed screw on
the filter housing (the larger headed bolt as shown). The priming pump is also on the nearside of the engine mounted to the side of the main injection pump. Priming is done in the normal way with the bleed screw tightened once all the air has been expelled.
19 The power steering reservoir
is set on the offside of the engine. Check the fluid level on the schedule one and two services. With the engine stopped the fluid should come up to the top mark on the dipstick. On the schedule three service the fluid should be changed which will require four litres of Dexron II. Next to the power steering 'reservoir is a water separator for the fuel system. Any water that has collected should he drained out at each service. To do this simply remove the thumbscrew from the bottom of the canister, release any water and refit.
20 After dropping the cab back
down the under grille checks can be carried out. First. is the clutch fluid, which should be checked on the schedule one and two services and changed on the schedule three. This will take 0.25 litres of fluid to SAE J1703/13. The engine coolant should contain a minimum of 30% antifreeze all year round; 50% is recommended. The radiator should be drained and 38 litres of fresh coolant put in on every schedule three service. On other services antifreeze concentration should be checked.
21 There is a restriction indica
tor in the air inlet system which shows if the filler has become blocked. Unless the indicator is showing to the contrary the filter need not be changed. However, it is not a bad idea to clean the housing and turn the filter round a little when the vehicle is serviced.
22 Just in front of the fuel tank
on the offside of the vehicle is the ether reservoir for the cold start system. The level of ether can be seen through the plastic reservoir and should be checked at each service. Should topping up be required the ether comes in an aerosol can which is pushed on to the filling nozzle of the reservoir until the proper level is reached. The last job is Lo torque the wheel nuts. All have right-hand threads and require between 610 and 680Nm (450-500lbft).