Ford rolls along
Page 14
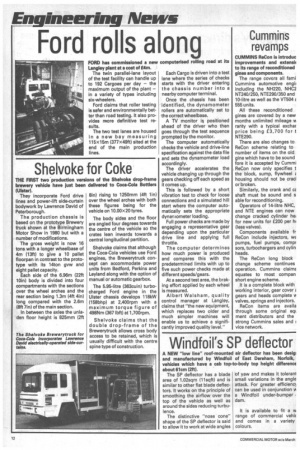
If you've noticed an error in this article please click here to report it so we can fix it.
FORD has commissioned a new Langley plant at a cost of £4m.
The twin parallel-lane layout of the test facility can handle up to 192 Cargoes per day — the maximum output of the plant — in a variety of types including six-wheelers.
Ford claims that roller testing is safer and environmentally better than road testing. It also provides more definitive test results.
The two test lanes are housed in a new bay measuring 115x 15m (377x 49ft) sited at the end of the main production lines. Each Cargo is driven into a test lane where the series of checks starts with the driver entering the chassis number into a nearby computer terminal.
Once the chassis has been identified, the dynamometer rollers are automatically set to the correct wheelbase.
A TV monitor is positioned ahead of the driver who then goes through the test sequence prompted by the monitor.
The computer automatically checks the vehicle and drive-line specification against the data file and sets the dynamometer load accordingly.
The driver accelerates the vehicle changing up through the gears checking off each speed as it comes up.
This is followed by a short vibration test to check for loose connections and a simulated hill start where the computer automatically sets the appropriate dynaniometer loading.
Full power checks are made by engaging a representative gear depending upon the particular drive line and applying full throttle.
The computer determines how much power is produced and compares this with the predetermined limits with up to five such power checks made at different speeds/gears.
At a second test area, the braking effort applied by each wheel is measured.
Albert Walsham, quality control manager at Langley, claims that "the new equipment, which replaces two older and much simpler machines will enable us to achieve a significantly improved quality level."