Ford Introduce Light Oilers
Page 44
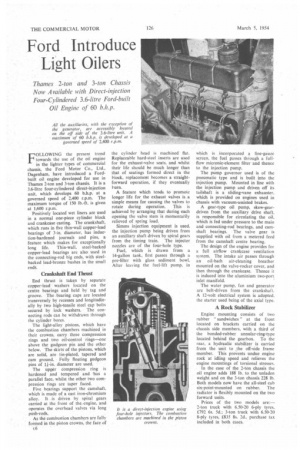
If you've noticed an error in this article please click here to report it so we can fix it.
Thames 2-ton and 3-ton Chassis Now Available with Direct-injection Four-Cylindered 3.6-litre Ford-built Oil Engine of 60 b.h.p.
FOLLOWING the present trend towards the use of the oil engine in the lighter types of commercial chassis, the Ford Motor Co., Ltd., Dagenham, have introduced a Fordbuilt oil engine developed for use in Thames 2-ton and 3-ton chassis. It is a 3.6-litre four-cylindered direct-injection unit, which develops 60 b.h.p. at a governed speed of 2,400 r.p.m. The maximum torque of 150 lb.-ft. is given at 1,600 r.p.m.
Positively located wet liners are used in a normal one-piece cylinder block and crankcase casting. The crankshaft, which runs in five thin-wall copper-lead bearings of 3-in, diameter, has induction-hardened journals and pins, a feature which makes for exceptionally long life. Thin-wall, steel-backed copper-lead bearings are also used in the connecting-rod big ends, with steelbacked lead-bronze bushes in the small ends.
Crankshaft End Thrust
End thrust is taken by separate copper-lead washers located on the centre bearings and held by tag and groove. The bearing caps are located transversely by recesses and longitudinally by two high-tensile steel cap bolts secured by lock washers. The connecting rods can be withdrawn through the cylinder bores.
The light-alloy pistons, which have the combustion chambers machined in their crowns, carry three compression rings and two oil-control rings—one above the gudgeon pin and the other below. The skirts of the pistons, which are solid, are tin-plated, tapered and cam ground. Fully floating gudgeon pins of 14-in. diameter are used.
The upper compression ring is hardened and tempered and has a parallel face, whilst the other two compression rings are taper faced.
Five bearings support the camshaft. which is made of a cast iron-chromium alloy. It is driven by spiral gears carried at the front of the,...engine, and operates the overhead valves via long push-rods.
As the combustion chambers are fully formed in the piston crowns, the face of c6 the cylinder head is machined flat. Replaceable hard-steel inserts are used for the exhaust-valve seats, and whilst their life should be much longer than that of seat ings formed direct in the block, replacement becomes a straightforward operation, if they eventually A feature which tends to promote longer life for the exhaust valves is a simple means for causing the valves to rotate during operation. This is achieved by arranging that during each opening the valve stem is momentarily relieved of spring load.
Simms injection equipment is used, the injection pump being driven from an auxiliary shaft driven by spiral gears from the timing train. The injector nozzles are of the four-hole type.
Fuel, which is drawn from a 14-gallon tank, first passes through a pre-filter with glass sediment bowl. After leaving the fuel-lift pump, in which is incorporated a fine-gauze screen, the fuel passes through a fullflow micronic-element filter and thence to the injection pump.
The pump governor used is of the pneumatic type and is built into the injection pump. Mounted in line with the injection pump and driven off its tailshaft is a sliding-vane exhauster, which is provided on engines used in chassis with vacuum-assisted brakes.
A gear-type oil pump, skew-geardriven from the auxiliary drive shaft. is responsible for circulating the oil, which is fed under pressure to the main and connecting-rod bearings, and camshaft bearings. The valve gear is supplied with oil from a metered feed from the camshaft centre hearing. The design of the engine provides for a full airflow crankcase ventilation system. The intake air passes through an oil-bath air-cleaning breather mounted on the valve-rocker cover, and then through the crankcase. Thence it is induced into the aluminium two-port inlet manifold.
The water pump, fan and generator arc belt-driven from the crankshaft. A 12-volt electrical system is adopted, the starter used being of the axial type.
A Rock Stabilizer
Engine mounting consists of two rubber " sandwiches " at the front located on brackets carried on the chassis side members, with a third of the bonded-rubber annular-ring-type located behind the gearbox. To the rear, a hydraulic stabilizer is carried from the unit to the off-side frame member. This prevents undue engine rock at idling speed and relieves the engine mountings of torsional stresses.
In the case of the 2-ton chassis the oil engine adds 188 lb. to the unladen weight and on the 3-ton chassis 228 lb. Both models now have the all-steel cab six-point-mounted on rubber. The radiator is flexibly mounted on the two forward units.
Prices of the two models are:2-ton truck with 6.50-20 6-ply tyres, £792 6s. 5d.: 3-ton truck with 6.50-20 8-ply tyres, £835 8s. 2d., purchase tax included in both cases.