Mighty micro tests mew Perkins diesels
Page 25
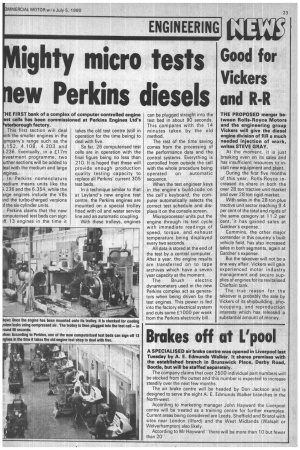
If you've noticed an error in this article please click here to report it so we can fix it.
'HE FIRST bank of a complex of computer controlled engine est cells has been commissioned at Perkins Engines Ltd's eterborough factory.
This first section will deal takes the old test centre (still in vith the smaller engines in the operation for the time being) to ompany's range such as the deal with five.
.152, 4.108, 4.203 and So far, 26 computerised test .236. Eventually, in a £.17m cells are in operation with the vestment programme, two final figure being no less than rther sections will be added to 210. It is hoped that these will eal with the medium and large provide enough production ngines. quality testing capacity to In Perkins nomenclature replace all Perkins' current 305 edium means units like the test beds, _236 and the 6.354, while the In a technique similar to that rge engines include the V8s at Leyland's new engine test ind the turbo-charged versions centre, the Perkins engines are )f the six-cylinder units. mounted on a special trolley Perkins claims that the new fitted with oil and water service :omputerised test beds can sign line and an automatic coupling.
iff 13 engines in the time it With these trolleys, engines can be plugged straight into the test bed in about 90 seconds. This compares with the 14 minutes taken by the old method.
The rest of the time saving comes from the processing of the performance data and the control systems. Everything is controlled from outside the cell with the whole procedure being operated on automatic sequence.
When the test engineer keys in the engine's build-code on the cell's keyboard, the computer automatically selects the correct test schedule and displays it on the console screen.
Microprocessor units put the engine through its test cycle with immediate readings of speed, torque, and exhaust temperature being displayed every two seconds.
All data is stored at the end of the test by a central computer. After a year, the engine results are transferred on to tape archives which have a seven year capacity at the moment.
The Brush electric dynamometers used in the new Perkins complex act as generators when being driven by the test engines. This power is fed into the factory electrical system and cuts some E1000 per week from the Perkins electricity bill.