This DIY wrecker is a winner
Page 29
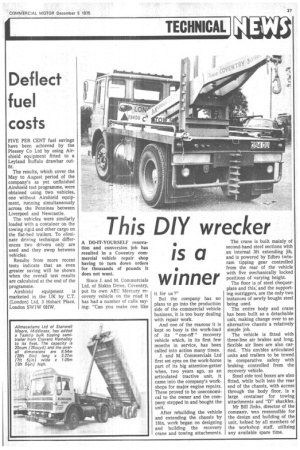
If you've noticed an error in this article please click here to report it so we can fix it.
A DO-IT-YOURSELF renovation and conversion job has resulted in a Coventry commercial vehicle repair shop having to turn down orders for thousands of pounds it does not want.
Since J. and M. Commercials Ltd, of Siskin Drive, Coventry, put its own AEC Mercury recovery vehicle on the road it has had a number of calls saying: "Can you make one like it for us ?"
But the company has no plans to go into the production side of the commercial vehicle business, it is too busy dealing with repair work.
And one of the reasons it is kept so busy is the work-load of its " one-off " recovery vehicle which, in its first few months in service, has been called into action many times.
J. and M. Commercials Ltd first set eyes on the work-horse part of its big 'attention-getter when, two years ago, as an articulated tractive unit, it came into the company's workshops for major engine repairs. These proved to be uneconomical to the owner and the company stepped in and bought the unit.
After rebuilding the vehicle and extending the chassis by 1Sin, work began on designing and building the recovery crane and towing attachments. The crane is built mainly of second-hand steel sections with • an internal 3ft extending jib, and is powered by Edbro twinram tipping gear controlled from the rear of the vehicle with five mechanically locked positions of varying height.
The floor is of steel chequerplate and this and the supporting outriggers, are the only two instances of newly bought steel being used.
The entire body and crane has been built as a detachable unit, making change over to an alternative chassis a relatively simple job.
The vehicle is fitted with three-line air brakes and long, flexible air lines are also carried. This enables articulated units and trailers to be towed in comparative safety with braking controlled from the recovery vehicle.
Steel side tool boxes are also fitted, while built into the rear end of the chassis, with access through the body floor, is a large container for towing attachments and "D" shackles.
Mr Bill Jinks, director of the company, was responsible for the design and building of the unit, helped by all members of the workshop staff, utilising any available spare time.