DUE 11,11-10ENCIE IDEFIENCE
Page 31
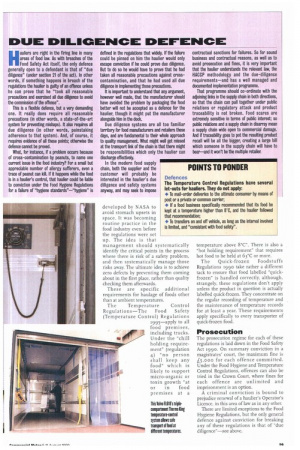
If you've noticed an error in this article please click here to report it so we can fix it.
Hauliers are right in the firing line in many areas of food law. As with breaches of the Food Safety Act itself, the only defence generally open to a defendant is that of "due diligence" (under section 21 of the act). In other words, if something happens in breach of the regulations the haulier is guilty of an offence unless he can prove that he "took all reasonable precautions and exercised all due diligence to avoid the commission of the offence".
This is a flexible defence, but a very demanding one. It really does require all reasonable precautions (in other words, a state-of-the-art system for preventing mishaps). It also requires all due diligence (in other words, painstaking adherence to that system). And, of course, it requires evidence of all these points; otherwise the defence cannot be proved.
What, for instance, if a problem occurs because of cross-contamination by peanuts, to name one current issue in the food industry? For a small but appreciable number of allergy sufferers, even a trace of peanut can kill. If it happens while the food is in a haulier's control, that haulier could be liable to conviction under the Food Hygiene Regulations for a failure of "hygiene standards"—"hygiene is defined in the regulations that widely. If the failure could be pinned on him the haulier would only escape conviction if he could prove due diligence. But to do so he would have to prove that he had taken all reasonable precautions against crosscontamination, and that he had used all due diligence in implementing those precautions.
It is important to understand that any argument, however well made, that the manufacturer should have avoided the problem by packaging the food better will not be accepted as a defence for the haulier, though it might put the manufacturer alongside him in the dock.
Due diligence systems are all too familiar territory for food manufacturers and retailers these days, and are fundamental to their whole approach to quality management. What might well get missed at the transport link of the chain is that there might be responsibilities which only the haulier can discharge effectively.
In the modern food supply chain, both the supplier and the customer will probably be interested in the haulier's due diligence and safety systems anyway, and may seek to impose contractual sanctions for failures. So for sound business and contractual reasons, as well as to avoid prosecution and fines, it is very important that the haulier understands the relevant law, the HACCP methodology and the due-diligence requirements—and has a well managed and documented implementation programme.
That programme should co-ordinate with the adjoining links in the supply chain in both directions, so that the chain can pull together under public relations or regulatory attack and product traceability is not broken. Food scares are extremely sensitive in terms of public interest; so public relations and a supply chain in disarray mean a supply chain wide open to commercial damage. And if traceability goes to pot the resulting product recall will be all the bigger, creating a large bill which someone in the supply chain will have to bear—and it won't be the multiple retailer.