TURBOCHARGING
Page 69
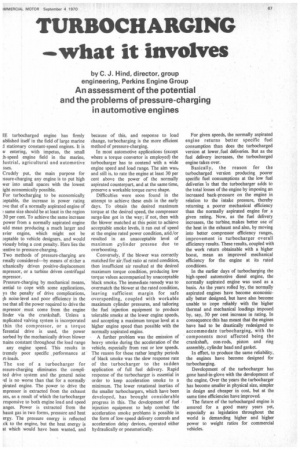
If you've noticed an error in this article please click here to report it so we can fix it.
4=M what it involves by C. J. Hind, director, group engineering, Perkins Engine Group
An assessment of the potential and the problems of pressure-charging in automotive engines
IE turbocharged engine has firmly ablished itself in the field of large marine d stationary constant-speed engines. It is w entering, with impetus, the small ;h-speed engine field in the marine, lustrial, agricultural and automotive sses.
Crudely put, the main purpose for ;ssure-charging any engine is to put high wer into small spaces with the lowest ight economically possible.
For turbocharging to be economically eptable, the increase in power rating Dye that of a normally aspirated engine of ; same size should be at least in the region 30 per cent. To achieve the same increase power from a normally aspirated engine ould mean producing a much larger and avier engine, which might not be eptable to vehicle designers, and would viously bring a cost penalty. Here lies the :entive to pressure-charging.
Two methods of pressure-charging are rmally considered----by means of either a ;chanically driven positive-displacement mpressor, or a turbine driven centrifugal mpressor.
Pressure-charging by mechanical means, tential to cope with some applications, ys the penalty of drive complications, ;h noise-level and poor efficiency in the ise that all the power required to drive the mpressor must come from the engine Under via the crankshaft. Unless a mplicated valving system is incorporated thin the compressor, or a torque Terential drive is used, the power sorbed by the mechanically driven blower nains constant throughout the load range any engine speed. This results in tremely poor specific performance at rt-loads.
The use of a turbocharger for essure-charging eliminates the complited drive system and the general noise rel is no worse than that for a normally pirated engine. The power to drive the mpressor is extracted from the exhaust ses, as a result of which the turbocharger responsive to both engine load and speed anges. Power is extracted from the haust gas in two forms, pressure and heat ergy. The pressure energy is reflected .ck to the engine, but the heat energy is at which would have been wasted, and because of this, and response to load change, turbocharging is the more efficient method of pressure-charging.
In most automotive applications (except where a torque convertor is employed) the turbocharger has to contend with a wide engine speed and load range. The aim was and still is, to rate the engine at least 30 per cent above the power of the normally aspirated counterpart, and at the same time, preserve a workable torque curve shape.
Difficulties were soon found in the attempt to achieve these ends in the early days. To obtain the desired maximum torque at the desired speed, the compressor surge-line got in the way; if not, then with the blower matched at this point to achieve acceptable smoke levels, it ran out of speed at the engine rated power condition, and/or resulted in an unacceptable level of maximum cylinder pressue due to overboosti ng.
Conversely, if the blower was correctly matched for air/fuel ratio at rated condition, then insufficient air resulted at the desired maximum torque condition, producing low torque values accompanied by unacceptable black smoke. The immediate remedy was to overmatch the blower at the rated condition, leaving sufficient margin for safe overspeeding, coupled with workable maximum cylinder pressures, and tailoring the fuel injection equipment to produce tolerable smoke at the lower engine speeds, and accepting a maximum torque level at a higher engine speed than possible with the normally aspirated engine.
• A further problem was the emission of heavy smoke during the acceleration of the vehicle, especially from rest or low speeds. The reason for these rather lengthy periods of black smoke was the slow response rate of the turbocharger to the sudden application of full fuel delivery. Rapid response of the turbocharger is essential in order to keep acceleration smoke to a minimum. The lower rotational inertias of the smaller turbochargers, which have been developed, has brought considerable progress in this. The development of fuel injection equipment to help combat the acceleration smoke problems is possible in the form of low-speed delivery controls and acceleration delay devices, operated either hydraulically or pneumatically. For given speeds, the normally aspirated engine returns better specific fuel consumption than does the turbocharged version at lower, fuel deliveries. But as the fuel delivery increases, the turbocharged engine takes over.
Basically, the reason for the turbocharged version producing poorer specific fuel consumptions at the low fuel deliveries is that the turbocharger adds to the total losses of the engine by imposing an increased back-pressure on the engine in relation to the intake pressure, thereby returning a poorer mechanical efficiency than the normally aspirated engine for a given rating. Now, as the fuel delivery increases, the turbine, makes better use of the heat in the exhaust and also, by moving into better compressor efficiency ranges, improvement in turbocharger overall efficiency results. These results, coupled with the work return obtainable with a higher boost, mean an improved mechanical efficiency for the engine at its rated conditions.
In the earlier days of turbocharging the high-speed automotive diesel engine, the normally aspirated engine was used as a basis. As the years rolled by, the normally aspirated engines have become economically better designed, but have also become unable to Cope reliably with the higher thermal and mechanical loadings imposed by, say, 30 per cent increase in rating. In consequence this has meant that the engines have had to be drastically redesigned to accommodate turbocharging, with the components most affected being the crankshaft, con-rods, piston and ring assembly, cylinder head and gasket.
In effect, to produce the same reliability, the engines have become designed for turbocharging.
Development of the turbocharger has gone hand-in-glove with the development of the engine. Over the years the turbocharger has become smaller in physical size, simpler in design and cheaper in cost, but at the same time efficiencies have improved.
The future of the turbocharged engine is assured for a good many years yet, especially as legislation throughout the world is demanding higher and higher power to weight ratios for commercial vehicles.