60,000 Miles with Air Suspension
Page 73

Page 72
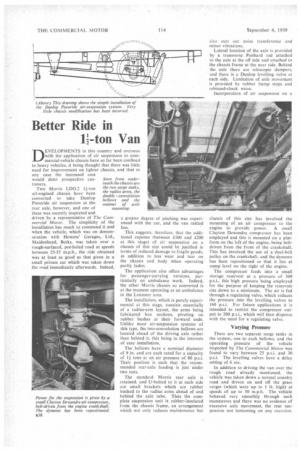
If you've noticed an error in this article please click here to report it so we can fix it.
Better Ride in E-ton Van
DEVELOPMENTS in this country and overseas with the application of air suspension to commercial-vehicle chassis have so far been confined to heavy vehicles, it being thought that there was little need for improvement on lighter chassis, and that in any case the increased cost would deter prospective customers.
Two Morris LD0.2 la-ton oil-cngined chassis have been converted to take Dunlop Pneuride air suspension at the rear axle, however, and one of these was recently inspected and driven by a representative of The Commercial Motor. The simplicity of the installation has much to commend it and when the vehicle, which was on demonstration with Hewens' Garages, Ltd., Maidenhead, Berks, was taken over a rough-surfaced, pot-holed road at speeds between 25-35 m.p.h., the ride obtained was at least as good as that given in a small private car which was taken down the road immediately afterwards. Indeed, a greater degree of pitching was experienced with the car, and the van rattled less.
This suggests. therefore, that the additional expense (between £100 and £200 at this stage) of air suspension on a chassis of this size could be justified in terms of reduced damage to fragile goods, in addition to less wear and tear on the chassis and body when operating partly laden.
The application also offers advantages for passenger-carrying versions, particularly on ambulance work. Indeed, the other Morris chassis so converted is at the moment operating as an ambulance in the Leicester area.
The installation, which is purely experimental at this stage, consists essentially of a radius-arm layout, the arms being fabricated box sections, pivoting on rubber bushes at their forward ends. Unlike most air-suspension systems of this type, the two-convolution bellows are located ahead of the driving axle rather than behind it, this being in the interests of easy installation.
The bellows have a nominal diameter of 9 in. and are each rated for a capacity of 14 tons at an air pressure of 80 p.s.i. Their position is such that the recommended rear-axle loading is just under two tons. • The standard Morris rear axle is retained, and U-bolted to it at each Side are small brackets which are rubber bushed to the radius arms ahead of and behind the axle tube. Thus the complete suspension unit is rubber-insulated from the chassis frame, an arrangement which not only reduces maintenance but chassis of this size has involved the mounting of an air compressor to the engine to provide power. A small Clayton Dewandre compressor has been employed and this is mounted on a platform on the left of the engine, being beltdriven from the front of the crankshaft. This has involved the use of a dual-belt pulley on the crankshaft, and the dynamo has been repositioned so that it lies at sump level on the right of the engine.
The compressor feeds into a small storage reservoir at a pressure of 300 p.s.i., this high pressure being employed for the purpose of keeping the reservoir size down to a minimum. The air is fed through a regulating valve, which reduces the pressure into the levelling valves to 160 p.s.i. For future applications it is intended to restrict the compressor output to 200 p.s.i., which will then dispense with the need for a regulating valve.
Varying Pressure
There are two separate surge tanks in the system, one to each bellows, and the operating pressure of the vehicle inspected by The Commercial Motor was found to vary between 25 and 30 p.s.i. The levelling valves have a delay setting of 6 sec.
In addition to driving the van over the rough road already mentioned, the vehicle was taken down a normal country road and driven on and off the grass verges (which were up to 1 ft. high) at speeds of up to 30 m.p.h. The vehicle behaved very smoothly through such manceuvres and there was no evidence of excessive axle movement, the rear suspension not bottoming on any occasion. far it has been difficult to assess ie merits of British air-suspension iesigns, because of the lack of ting experience with them. But some of the vehicles with air susin acquired by progressive operators they were first offered are beginto reach mileages at which some isions as to their efficiency can be such unit is a Crane 16-17-ton :railer with Airtrail pneumatic susni which went into operation with a Road Services experimentally in 1958. Since that time the semi-trailer iovered some 60.000 miles while ting from the B.R.S. depot at h its A.E.C. Mandator tractor unit, been engaged mainly on runs to home, carrying margarine on the rd journey and steel wire on the 1. Most of the mileage has been full load, unladen running being ed to shunting operations at each I the main run.
Independent Suspension
Crane Airtrail tandem-axle airision layout is derived from a predesign which used leaf springs as aspension medium. It provides :ndent wheel suspension by mounte stub axles for each pair of wheels trailing box-section arm, each arm rig at its forward end on selfig radial roller bearings.
Firestone two-convolution Airide s are interposed between the rear of the forward trailing arms and ions of the leading ends of the arms. Twin telescopic shock :lers provide damping and arc d alongside, and in a similar posio, the air springs.
rip stops limit upward deflection. two Hymatic valves perform the ng operation for the suspension. alves have a 10-second delay setting event excessive air losses during ml changes of altitude caused by ; and road camber. Air for the s is taken from the supply for the tg system through a one-way res. valve which does not release air suspension until pressure in the ig system has reached 75-80 p.s.i.
remainder of the semi-trailer is of conventional semi-lightweight construction, incorporating wooden flooring and light-alloy side raves, loading board and cross-bearers. It weighs 2 tons 19 cwt.. which is several hundredweight less than comparable semi-trailers in the B.R.S. fleet with conventional laminated springs.
B.R.S. are most concerned with reducing essential maintenance wherever possible. In this respect the Crane semitrailer has proved most successful. The only points on the bogie requiring regular attention are the pivots for the trailing arms (four grease points) and the air filters which protect the suspension valves (cleaned by air pressure approximatel every six weeks).
Maintenance costs, which have included one annual inspection, have been low. Trouble was experienced with both the levelling valves, one failing at 12,326 miles and -the other at 43,000 miles. This was caused by the ingress of dirt, which damaged the valve scatings.
Filters Now Fitted
Filters had been thought to he unnecessary, but this opinion has since been revised and they are now fitted to this and all other Airtrail bogies. No further trouble has been recorded, so it would appear that effective protection for the levelling valves is now provided.
When the second levelling valve failed the vehicle was in Scunthorpe. It was driven back to Grays fully laden with the air spring deflated, the rubber bump stops fitted inside the springs were adequate for the emergency.
During this trip a flint became caught between the two convolutions of the deflated air bag. causing abrasion and eventual perforation of it. This is regarded by the air-spring manufacturers as a most unlikely occurrence and gaiters, fitted to the springs on the original Crane installation to prevent it happening, were omitted later. Had filters been fitted to the air supply for the springing in the first place. these difficulties would not have arisen. However, this is the sort of teething trouble which only sustained operation can bring to light. Otherwise, the suspension has performed exceptionally well.
With improved suspension it is reasonable to suppose that tyre wear will be reduced. Whilst reliable conclusions cannot be drawn from the performance of one semi-trailer, it is of interest that in 60.000 miles of service, only two of the original tyres have been replaced and the remaining tyres have substantial tread remaining.
Drivers who have had experience of the air-sprung senUarailer have been enthusiastic about the reduction in movement and were loth to return to conventionally sprung units. Following the unladen A.E.C.-Crane outfit around the Grays area it was noticeable how much better the rear end rode than either the tractor unit or the front end of the platform.
Effective Damping
Even over severe bumps, such as a rough level crossing, the semi-trailer suspension damped itself far more quick!) than that of the tractor. Obviously after 60,000 miles the shock absorbers arc still performing well, denying past suggestions that these units would fail rapidly when dealing with a suspension system which has no inherent damping.
An operational benefit which has, yet to he fully exploited for air-sprung vehicles, such as the Crane semi-trailer, is their ability to provide a constant platform height. Where pallet handling is employed at present it-is usually necessary to load vehicles with fork-lift trucks rather than direct from a ramp, because platform heights differ from one vehicle to another and, for individual units, frOm the laden to the unladen condition.
With a self-adjusting air-suspension system (which must have a large air reservoir to allow. for the ,semi-trailer being detached from its motive unit) it is possible to provide and maintain a set loading-height irrespective of the load on the vehicle. This would make it possible to load pallets from a matching ramp direct on to the vehicle. using simple trolleys in place of the more expensive fork-lift truck.