Hannover: trail blazing
Page 10
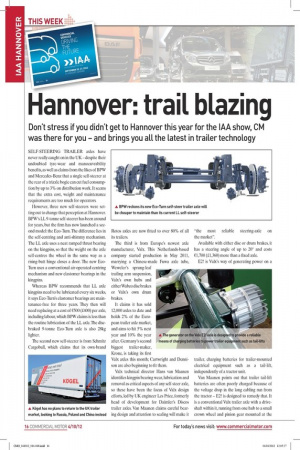
Page 11
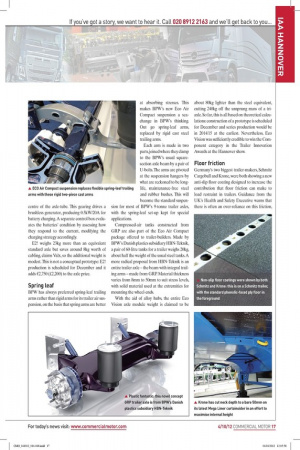
Page 12
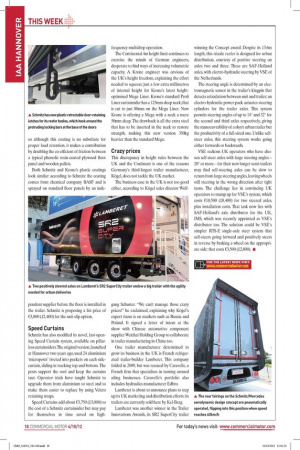
If you've noticed an error in this article please click here to report it so we can fix it.
Don’t stress if you didn’t get to Hannover this year for the IAA show, CM was there for you – and brings you all the latest in trailer technology
SELF-STEERING TRAILER axles have never really caught on in the UK – despite their undoubted tyre-wear and manoeuvrability benefits, as well as claims from the likes of BPW and Mercedes-Benz that a single self-steerer at the rear of a triaxle bogie can cut fuel consumption by up to 3% on distribution work. It seems that the extra cost, weight and maintenance requirements are too much for operators.
However, three new self-steerers were setting out to change that perception at Hannover. BPW’s LL 9-tonne self-steerer has been around for years, but the firm has now launched a second model: the Eco-Turn. The difference lies in the self-centring and anti-shimmy mechanism. The LL axle uses a neat ramped thrust bearing on the kingpins, so that the weight on the axle self-centres the wheel in the same way as a rising-butt hinge closes a door. The new EcoTurn uses a conventional air-operated centring mechanism and new elastomer bearings in the kingpins.
Whereas BPW recommends that LL axle kingpins need to be lubricated every six weeks, it says Eco-Turn’s elastomer bearings are maintenance-free for three years. They then will need replacing at a cost of €500 (£400) per axle, including labour, which BPW claims is less than the routine lubrication of the LL axle. The discbraked 9-tonne Eco-Turn axle is also 28kg lighter.
The second new self-steerer is from Schmitz Cargobull, which claims that its own-brand Rotos axles are now fitted to over 80% of all its trailers.
The third is from Europe’s newest axle manufacturer, Valx. This Netherlands-based company started production in May 2011, marrying a Chinese-made Fuwa axle tube, Weweler’s sprung-leaf trailing arm suspension, Valx’s own hubs and either Wabco disc brakes or Valx’s own drum brakes.
It claims it has sold 12,000 axles to date and holds 2% of the European trailer axle market, and aims to hit 5% next year and 10% the year after. Germany’s second biggest trailer-maker, Krone, is taking its first Valx axles this month; Cartwright and Dennison are also beginning to fit them.
Valx technical director Hans van Maanen identifies kingpin bearing wear, lubrication and removal as critical aspects of any self-steer axle, so these have been the focus of Valx design efforts, led by UK engineer Les Price, formerly head of development for Daimler’s Discos trailer axles. Van Maanen claims careful bearing design and attention to sealing will make it “the most reliable steering-axle on the market” .
Available with either disc or drum brakes, it has a steering angle of up to 20° and costs €1,700 (£1,360) more than a fixed axle.
E2! is Valx’s way of generating power on a trailer, charging batteries for trailer-mounted electrical equipment such as a tail-lift, independently of a tractor unit.
Van Maanen points out that trailer tail-lift batteries are often poorly charged because of the voltage drop in the long cabling run from the tractor – E2! is designed to remedy that. It is a conventional Valx trailer axle with a driveshaft within it, running from one hub to a small crown wheel and pinion gear mounted at the centre of the axle-tube. This gearing drives a brushless generator, producing 0.5kW/20A for battery charging. A separate control box evaluates the batteries’ condition by assessing how they respond to the current, modifying the charging strategy accordingly.
E2! weighs 23kg more than an equivalent standard axle but saves around 8kg worth of cabling, claims Valx, so the additional weight is modest. This is not a conceptual prototype: E2! production is scheduled for December and it adds €2,750 (£2,200) to the axle price.
Spring leaf
BPW has always preferred spring-leaf trailing arms rather than rigid arms for its trailer air suspension, on the basis that spring arms are better at absorbing stresses. This makes BPW’s new Eco Air Compact suspension a seachange in BPW’s thinking. Out go spring-leaf arms, replaced by rigid cast steel trailing arms.
Each arm is made in two parts, joined where they clamp to the BPW’s usual squaresection axle beam by a pair of U-bolts. The arms are pivoted at the suspension hangers by what are reckoned to be longlife, maintenance-free steel and rubber bushes. This will become the standard suspension for most of BPW’s 9-tonne trailer axles, with the spring-leaf set-up kept for special applications.
Compressed-air tanks constructed from GRP are also part of the Eco Air Compact package offered to trailer-builders. Made by BPW’s Danish plastics subsidiary HBN-Teknik, a pair of 60-litre tanks for a trailer weighs 20kg, about half the weight of the usual steel tanks. A more radical proposal from HBN-Teknik is an entire trailer axle – the beam with integral trailing arms – made from GRP. Material thickness varies from 8mm to 50mm to suit stress levels, with solid material used at the extremities for mounting the wheel-ends.
With the aid of alloy hubs, the entire Eco Vision axle module weight is claimed to be about 80kg lighter than the steel equivalent, cutting 240kg off the unsprung mass of a triaxle. So far, this is all based on theoretical calculations: construction of a prototype is scheduled for December and series production would be in 2014/15 at the earliest. Nevertheless, Eco Vision was sufficiently credible to win the Component category in the Trailer Innovation Awards at the Hannover show.
Floor friction
Germany’s two biggest trailer-makers, Schmitz Cargobull and Krone, were both showing a new anti-slip floor coating designed to increase the contribution that floor friction can make to load restraint in trailers. Guidance from the UK’s Health and Safety Executive warns that there is often an over-reliance on this friction, so although this coating is no substitute for proper load retention, it makes a contribution by doubling the co-efficient of friction between a typical phenolic resin-coated plywood floor panel and wooden pallets.
Both Schmitz and Krone’s plastic coatings look similar: according to Schmitz the coating comes from chemical company BASF and is sprayed on standard floor panels by an inde pendent supplier before the floor is installed in the trailer. Schmitz is proposing a list price of €3,000 (£2,400) for the anti-slip option.
Speed Curtains
Schmitz has also modified its novel, fast-opening Speed Curtain system, available on pillarless curtainsiders. The original version, launched at Hannover two years ago, used 24 aluminium ‘microposts’ riveted into pockets on each sidecurtain, sliding in tracking top and bottom. The posts support the roof and keep the curtains taut. Operator trials have taught Schmitz to upgrade them from aluminium to steel and to make them easier to replace by using Velcro retaining straps.
Speed Curtains add about €3,750 (£3,000) to the cost of a Schmitz curtainsider but may pay for themselves in time saved on high frequency multidrop operation.
The Continental 4m height limit continues to exercise the minds of German engineers, desperate to find ways of increasing volumetric capacity. A Krone engineer was envious of the UK’s height freedom, explaining the effort needed to squeeze just a few extra millimetres of internal height for Krone’s latest heightoptimised Mega Liner. Krone’s standard Profi Liner curtainsider has a 125mm-deep neck; that is cut to just 80mm on the Mega Liner. Now Krone is offering a Mega with a neck a mere 50mm deep. The drawback is all the extra steel that has to be inserted in the neck to restore strength, making this new version 350kg heavier than the standard Mega.
Crazy prices
This discrepancy in height rules between the UK and the Continent is one of the reasons Germany’s third-largest trailer manufacturer, KÖgel, does not tackle the UK market.
The business case in the UK is not too good either, according to KÖgel sales director Wolf gang Schuster. “We can’t manage those crazy prices!” he exclaimed, explaining why KÖgel’s export focus is on markets such as Russia and Poland. It signed a letter of intent at the show with Chinese automotive component supplier Weichai Holding Group to collaborate in trailer manufacturing in China too.
One trailer manufacturer determined to grow its business in the UK is French refrigerated trailer-builder Lamberet. This company folded in 2009, but was rescued by Caravelle, a French firm that specialises in turning around ailing businesses. Caravelle’s portfolio also includes hydraulics manufacturer Edbro.
Lamberet is about to announce plans to step up its UK marketing and distribution efforts: its trailers are currently sold here by Kel-Berg.
Lamberet was another winner in the Trailer Innovations Awards, its SR2 SuperCity trailer winning the Concept award. Despite its 13.6m length, this triaxle reefer is designed for urban distribution, courtesy of positive steering on axles two and three. These are SAF-Holland axles, with electro-hydraulic steering by VSE of the Netherlands.
The steering angle is determined by an electromagnetic sensor in the trailer’s kingpin that detects articulation between unit and trailer; an electro-hydraulic power-pack actuates steering cylinders for the trailer axles. This system permits steering angles of up to 14° and 32° for the second and third axles respectively, giving the manoeuvrability of a short urban trailer but the productivity of a full-sized one. Unlike selfsteer axles, this steering system works going either forwards or backwards.
VSE reckons UK operators who have chosen self-steer axles with large steering angles – 20° or more – for their new longer semi-trailers may find self-steering axles can be slow to return from large steering angles, leaving wheels still steering in the wrong direction after tight turns. The challenge lies in convincing UK operators to stump up for VSE’s system, which costs €10,500 (£8,400) for two steered axles, plus installation costs. That task now lies with SAF-Holland’s axle distributor for the UK, IMS, which was recently appointed as VSE’s distributor too. The solution could be VSE’s simpler RTS-E single-axle steer system that self-steers going forward and positively steers in reverse by braking a wheel on the appropriate side: that costs €3,500 (£2,800). n