GOING PLACES
Page 53
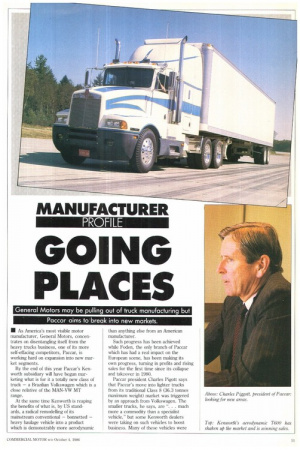
Page 54
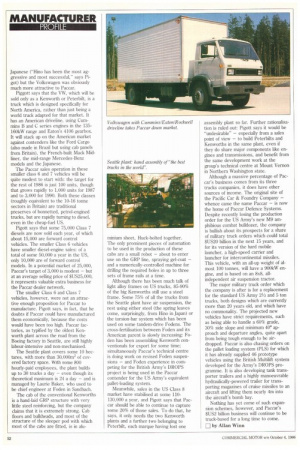
If you've noticed an error in this article please click here to report it so we can fix it.
General Motors may be pulling out of truck manufacturing but
Paccar aims to break into new markets.
• As America's most visible motor manufacturer, General Motors, concentrates on disentangling itself from the heavy trucks business, one of its more self-effacing competitors, Paccar, is working hard on expansion into new market segments.
By the end of this year Paccar's Kenworth subsidiary will have begun marketing what is for it a totally new class of truck — a Brazilian Volkswagen which is a close relative of the MAN-VW MT range.
At the same time Kenworth is reaping the benefits of what is, by US standards, a radical remodelling of its mainstream conventional — bonnetted — heavy haulage vehicle into a product which is demonstrably more aerodynamic than anything else from an American manufacturer.
Such progress has been achieved while Foden, the only branch of Paccar which has had a real impact on the European scene, has been making its own progress, turning in profits and rising sales for the first time since its collapse and takeover in 1980.
Paccar president Charles Pigott says that Paccar's move into lighter trucks from its traditional Class 8 (36.3 tonnes maximum weight) market was triggered by an approach from Volkswagen. The smaller trucks, he says, are ". . . much more a commodity than a specialist vehicle," but some Kenworth dealers were taking on such vehicles to boost business. Many of these vehicles were
Japanese ("Hino has been the most aggressive and most successful," says Pigot) but the Volkswagen was obviously much more attractive to Paccar.
Piggott says that the VW, which will be sold only as a Kenworth or Peterbilt, is a truck which is designed specifically for North America, rather than just being a world truck adapted for that market. It has an American driveline, using Cummins B and C series engines in the 135160kW range and Eaton's 4106 gearbox. It will stack up on the American market against contenders like the Ford Cargo (also made in Brazil but using cab panels from Britain), the French-built Mack Midliner, the mid-range Mercedes-Benz models and the Japanese.
The Paccar sales operation in these smaller class 6 and 7 vehicles will be quite modest to start with: the target for the rest of 1986 is just 100 units, though that grows rapidly to 1,000 units for 1987 and to 3,000 for 1990. Both these classes (roughly equivalent to the 10-16 tonne sectors in Britain) are traditional preserves of bonnetted, petrol-engined trucks, but are rapidly turning to diesel, even in the cheap-fuel US.
Pigott says that some 75,000 Class 7 diesels are now sold each year, of which about 15,000 are forward control vehicles. The smaller Class 6 vehicles have smaller diesel-engine sales: of a total of some 50,000 a year in the US, only 10,000 are of forward control models. In a potential market of 25,000, Paccar's target of 3,000 is modest — but at an average selling price of $US25,000, it represents valuable extra business for the Paccar dealer network.
The smaller Class 6 and Class 7 vehicles, however, were not an attractive enough proposition for Paccar to manufacture. Pigott says, in fact, that he doubts if Paccar could have manufactured them economically, because the costs would have been too high. Paccar factories, as typified by the oldest Kenworth plant across the road from the Boeing factory in Seattle, are still highly labour-intensive and non-mechanised.
The Seattle plant covers some 10 hectares, with more than 30,000m2 of covered factory space. With some 800 hourly-paid employees, the plant builds up to 30 trucks a day — even though its theoretical maximum is 24 a day — and is managed by Laurie Baker, who used to be chief engineer at Foden in Sandbach.
The cab of the conventional Kenworths is a hand-laid GRP structure with very little steel reinforcing, but the company claims that it is extremely strong. Cab floors and bulkheads, and most of the structure of the sleeper pod with which most of the cabs are fitted, is in alu minium sheet, Huck-bolted together. The only prominent pieces of automation to be used in the production of these cabs are a small robot — about to enter use on the GRP line, spraying gel-coat — and a numerically-controlled machine for drilling the required holes in up to three sets of frame rails at a time.
Although there has been much talk of light alloy frames on US trucks, 85-90% of the big Kenworths still use a steel frame. Some 75% of all the trucks from the Seattle plant have air suspension, the rest using either steel (the spring leaves come, surprisingly, from Hino in Japan) or the torsion-bar system which has been used on some tandem-drive Fodens. The cross-fertilisation between Foden and its American parent is slowly increasing: Foden has been assembling Kenworth conventionals for export for some time; simultaneously Paccar's technical centre is doing work on revised Foden suspensions — and Foden experience in competing for the British Army's DROPS project is being used in the Paccar contender for the US Army's equivalent pallet-loading system.
Meanwhile, sales in the US Class 8 market have stabilised at some 110130,000 a year, and Pigott says that Paccar should be able to continue to capture some 20% of those sales. To do that, he says, it only needs the two Kenworth plants and a further two belonging to Peterbilt, each marque having lost one
assembly plant so far. Further rationalisation is ruled out: Pigott says it would be "undesirable" — especially from a sales point of view — to build Peterbilts and Kenworths in the same plant, even if they do share major components like engines and transmissions, and benefit from the same development work at the group's technical centre at Mount Vernon in Northern Washington state.
Although a massive percentage of Paccar's business comes from its three trucks companies, it does have other sources of income. The original site of the Pacific Car & Foundry Company — whence came the name Paccar — is now the home of Paccar Defence Systems. Despite recently losing the production order for the US Army's new M9 amphibious combat bulldozer, the company is bullish about its prospects for a share of military truck orders which could total $U520 billion in the next 15 years, and for its version of the hard mobile launcher, a high-speed carrier and launcher for intercontinental missiles. This vehicle, with an all-up weight of almost 100 tonnes, will have a 900kW engine, and is based on an 8x8, allindependent air suspension tractor.
The major military truck order which the company is after is for a replacement for the standard US Army 21/2 and 5 ton trucks, both designs which are currently more than 20 years old, and which have no commonality. The projected new vehicles have strict requirements, such as being able to handle a 60% grade, 30% side slope and minimum 40° approach and departure angles, quite apart from being tough enough to be airdropped. Paccar is also chasing orders on the pallet loading system (PLS) for which it has already supplied 46 prototype vehicles using the British MuWI& system developed for the Army's DROPS programme. It is also developing tank transporter trailers and a highly manoeuvrable hydraulically-powered trailer for transporting magazines of cruise missiles to an aircraft and lifting them nearly 4m into the aircraft's bomb bay.
Nothing has yet come of such expansion schemes, however, and Paccar's $US2 billion business will continue to be truck-based for a long time to come.
by Allan Winn