Going round in circles
Page 59
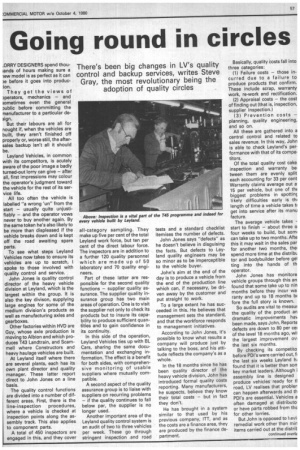
Page 60
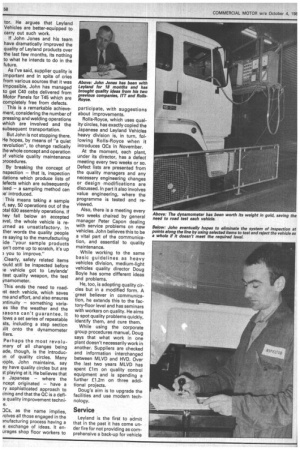
Page 61
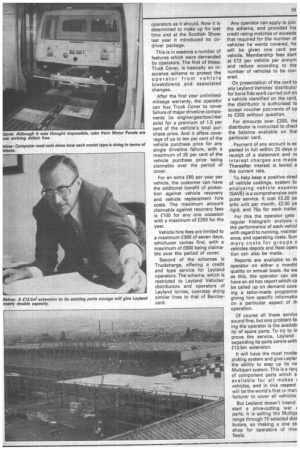
If you've noticed an error in this article please click here to report it so we can fix it.
There's been big changes in LV's quality control and backup services, writes Steve Gray, the most revolutionary being the adoption of quality circles
_ORRY DESIGNERS spend thou;ands of hours making sure a Iew model is as perfect as it can )e before it goes into producion.
They get the views of verators, mechanics — and sometimes even the general public before committing the -nanufacturer to a particular design.
But their labours are all for nought if, when the vehicles are built, they aren't finished off properly or, worse still, the aftersales backup isn't all it should be.
Leyland Vehicles, in common with its competitors, is acutely aware of the poor image a badly turned-out lorry can give — after all, first impressions may colour the operator's judgment toward the vehicle for the rest of its service life.
All too often the vehicle is labelled "a wrong 'un" from the start — usually quite unjustifiably — and the operator vows never to buy another again. By the same token he's also likely to be more than displeased if the vehicle breaks down and is kept off the road awaiting spare parts.
To see what steps Leyland Vehicles now takes to ensure its vehicles are up to scratch, I spoke to those involved with quality control and service.
John Jones is quality control director of the heavy vehicle division at Leyland, which is the largest within the group. It is also the key divison, supplying large engines for some of the medium division's products as well as manufacturing axles and gearboxes.
Other factories within HVD are Guy, whose axle production is moving to Albion and which produces T43 Landtrain, and Scammell where Constructors and heavy haulage vehicles are built.
At Leyland itself where there are several plants, each has its own plant director and quality manager. These latter report direct to John Jones on a line basis.
The quality control functions are divided into a number of different areas. First, there is the line-inspection procedures, where a vehicle is checked at inspection points along the assembly track. This also applies to component parts.
A total of 450 inspectors are engaged in this, and they cover all-category sampling. They make up five per cent of the total Leyland work force, but ten per cent of the direct labour force. The inspectors are in addition to a further 120 quality personnel which are made up of 50 laboratory and 70 quality engineers.
Part of these latter are responsible for the second quality functions — supplier quality assurance. The supplier quality insurance group has two main areas of operation. One is to visit the supplier not only to check its products but to insure its capability to produce sufficient quantities and to gain confidence in its continuity.
In this side of the operation, Leyland Vehicles ties up with BL Cars, sharing the same documentation and exchanging information. The effect is a benefit for both sides, with comprehensive monitoring of usable suppliers where mutually compatible.
A second aspect of the quality assurance group is to liaise with suppliers on recurring problems — if the quality continues to fall below par, the supplier is no longer used.
Another important area of the Leyland quality control system is an audit of two to three vehicles per week. These go through stringent inspection and road tests and a standard checklist itemises the number of defects.
John Jones says "defects" as he doesn't believe in disguising the facts. But defects to Leyland quality engineers may be so minor as to be imperceptible to the vehicle buyer.
John's aim at the end of the day is to produce a vehicle from the end of the production line which can, if necessary, be driven away by the customer and put straight to work.
To a large extent he has succeeded in this. He believes that management sets the standard, and that the workforce responds to management initiatives.
According to John Jones, it's possible to know what results a company will produce just by talking to the boss, and his attitude reflects the company's as a whole.
In the 18 months since he has been quality director of the heavy vehicle division, John has introduced formal quality costs reporting. Many manufacturers, he suspects, believe they know their total costs — but in fact they don't.
He has brought in a system similar to that used by his previous company, ITT, and as the costs are a finance area, they are produced by the finance department.
Basically, quality costs fall into three categories: (1) Failure costs — those incurred due to a failure to produce products that confirm. These include scrap, warranty work, re-work and rectification.
(2) Appraisal costs — the cost of finding out (that is, inspection, supplier inspection.) (3) Prevention costs — planning, quality engineering, and so on.
All these are gathered into a central control and related to sales revenue. In this way, John is able to check Leyland's performance with that of its competitors.
Of the total quality cost cake inspection and warranty be tween them are evenly split each accounting for 33 per cent Warranty claims average out a 15 per vehicle, but one of thE biggest problems in spottinc likely difficulties early is thr length of time a vehicle takes tr get into service after its menu facture.
The average vehicle takes start to finish — about three o four weeks to build, but soma can take up to two months. Afte this it may wait in the sales par for another two months, thei spend more time at the distribi tor and bodybuilder before gel ting into the hands of th operator.
John Jones has monitore vehicle groups through this an found that some take up to nin months before they incur wa ranty and up to 18 months La fore the full story is known.
So audits are vital to measur the quality of the product an dramatic improvements haN, been made, says John. Reporte defects are down to 80 per cet of the level 18 months ago, MI the largest improvement ovi the last six months.
By checking its competito before PDI's were carried out, fi the last six weeks Leyland hi found that it is better than son key market leaders. Although i assembly line is designed produce vehicles ready for tl road, LV realises that probler can happen afterwards and th PDI's are essential. Vehicles a often damaged at distributo or have parts robbed from the for other lorries.
But John is opposed to I lavii remedial work other than min items carried out at the distriL continued overle tor. He argues that Leyland Vehicles are better-equipped to carry out such work.
If John Jones and his team have dramatically improved the quality of Leyland products over the last few months, its nothing to what he intends to do in the future.
As I've said, supplier quality is important and in spite of cries from various sources that it was impossible, John has managed to get C40 cabs delivered from Motor Panels for T45 which are completely free from defects.
This is a remarkable achievement, considering the number of pressing and welding operations which are involved and the subsequent transportation.
But John is not stopping there. He hopes, by means of "a quiet revolution", to change radically the whole concept and operation pf vehicle quality maintenance procedures.
By breaking the concept of nspection — that is, inspection aations which produce lists of iefects which are subsequently ixed — a sampling method can )e' introduced.
This means taking a sample if, say, 50 operations out of the Dta I 630 assembly operations. If hey fall below an accepted avel, the whole vehicle is reJrned as unsatisfactory. In ther words the quality people re saying to the manufacturing ide "your sample products on't come up to scratch, it's up ) you to improve."
Clearly, safety related items ,ould still be inspected before le vehicle got to Leyfands' test quality weapon, the test ynamometer.
This ends the need to roadist each vehicle, which save me and effort, and also ensure mtinuity — something varia es like the weather and th .iasons can't guarantee. I lows a set series of repeatabl sts, including a step sectio Jilt onto the dynamomete Ilers.
Perhaps the most revolu mary of all changes being ade, though, is the introduc m of quality circles. Man ople, John maintains, say ey have quality circles but are it playing at it. He believes tha e Japanese — where the ncept originated — have a ry sophisticated approach to lining and that the QC is a defi:e quality improvement technie.
aCs, as the name implies, tolves all those engaged in the inufacturing process having a e exchange of ideas. It enurages shop floor workers to participate, with suggestions about improvements.
Rolls-Royce, which uses quality circles, has exactly copied the Japanese and Leyland Vehicles heavy division is, in turn, following Rolls-Royce when it introduces QCs in November.
At the moment, each plant, under its director, has a defect meeting every two weeks or so. Defect lists are presented from the quality managers and any necessary engineering changes or design modifications are discussed. In part it also involves value engineering, where the programme is tested and reviewed.
Also, there is a meeting every two weeks chaired by general manager Peter Capon dealing with service problems on new vehicles. John believes this to be a vital part of the communication, and essential to quality maintenance.
While working to the same basic guidelines as heavy vehicles division, medium-light vehicles quality director Doug Boyle has some different ideas and problems.
He, too, is adopting quality circles but in a modified form. A s great believer in communication, he extends this to the fac tory-floor level and has seminars e with workers on quality. He aims t to spot quality problems quickly, e identify them, and cure them.
• While using the corporate group procedures manual, Doug says that what work in one plant doesn't necessarily work in another. Suppliers are checked and information interchanged y between MLVD and HVD. Over the last two years IVILVD has spent Elm on quality control t equipment and is spending a further E1.2m on three additional projects.
Doug's aim is to upgrade the facilities and use modern technology.
Service
Leyland is the first to adroit that in the past it has come under fire for not providing as comprehensive a back-up for vehicle operators as it should. Now it is determined to make up for lost time and at the Scottish Show last year it introduced its codriver package.
This is in essence a number of features which were demanded by operators. The first of these, Truck Cover, is basically an insurance scheme to protect the operator from vehicle breakdowns and associated changes.
After the first year unlimitedmileage warranty, the operator can buy Truck Cover to cover failure of major driveline components (ie engine/gearbox/rear axle) for a premium of 1.5 per cent of the vehicle's total purchase price. And it offers coverage of up to ten per cent of the vehicle purchase price for any single driveline failure, with a maximum of 25 per cent of the vehicle purchase price being claimable over the period of cover.
For an extra £65 per year per vehicle, the customer can have the additonal benefit of protection against vehicle recovery and vehicle replacement hire costs. The maximum amount claimable against recovery fees is E100 for any one occasion with a maximum of £250 for the year.
Vehicle hire fees are limited to a maximum £300 of seven days, whichever comes first, with a maximum of £600 being claimable over the period of cover.
Second of the schemes is Truckcharge, offering a credit and type service for Leyland operators. The scheme, which is restricted to Leyland Vehicles' distributors and operators of Leyland lorries, operates along similar lines to that of Barclaycard. Any operator can apply to join the scheme, and provided his credit rating matches or exceeds that required for the number of vehicles he wants covered, he will be given one card per vehicle. Membership fees start at £12 per vehicle per annum and reduce according to the number of vehicles to be covered.
On presentation of the card to any Leyland Vehicles' distributor for bona fide work carried out on a vehicle identified on the card, the distributor is authorised to accept voucher payments of up to £200 without question.
For amounts over £200, the distributor is instructed to check the balance available on that particular card.
Payment of any account is ex pected in full within 25 days a receipt of a statement and nc interest charges are made Thereafter interest is levied a the current rate.
To help keep a positive checl of vehicle castings, system fo analysing vehicle expenst (SAVE) is a comprehensive corn puter service. It cost £2.20 pe artic unit per month, £2.50 pe rigid, and 75p for each trailer.
For this the operator gets regular histogram analysis c the performance of each vehicl with regard to running, mainter ance, and operating costs. Surr mary costs for groups o vehicles depots and fleet operE tion can also be made.
Reports are available to th operator on either a monthl quality or annual basis. As we as this, the operator can als have an ad hoc report which ca be called up on demand cove ing a tailor-made programm giving him specific informatio on a particular aspect of th operation.
Of course all these service sound fine, but one problem fai ing the operator is the availabi ity of spare parts. To try to in prove the service, Leyland expanding its parts centre with £13.5m extension.
It will have the most mode( picking system and give Leylar the ability to step up its no Multipart system. This is a ranç of component parts which a available for all makes ( vehicles, and in this respect will be the world's first cv man facturer to cover all vehicles.
But Leyland doesn't intend start a price-cutting war c parts. It is selling the Multip range through 70 selected dist butors, so making a one stt shop for operators of mix( fleets.