testing
Page 123
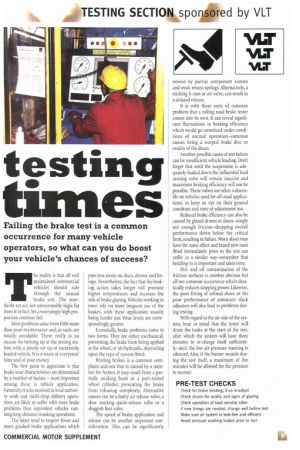
If you've noticed an error in this article please click here to report it so we can fix it.
tint
Failing the brake test is a common occurrence for many vehicle operators, so what can you do boost your vehicle's chances of success?
The reality is that all well maintained commercial vehicles should sale through the annual brake test. The standards set are not unreasonably high, far from it in fact.Yet a worryingly high proportion continue fail.
Most problems arise from little more than poor maintenance and, as such, are totally avoidable. There really is no excuse for turning up at the testing station with a poorly set-up or incorrectly loaded vehicle. It is a waste of everyones' time and of your money.
The first point to appreciate is that brake wear characteristics are determined by a number of factors — most important among these is vehicle application. Generally, trucks involved in local authority work and multi-drop delivery operations are likely to suffer with more brake problems than equivalent vehicles running long-distance trunking operations. The latter tend to require fewer and more gradual brake applications which puts less strain on discs, drums and linings. Nevertheless, the fact that the braking action takes longer will promote higher temperatures and increase the risk of brake glazing. Vehicles working in town rely on more frequent use of the brakes, with these application usually being harder too. Wear levels are correspondingly greater.
Essentially, brake problems come in two forms. They are either mechanical, preventing the brake from being applied at the wheel, or air/hydraulic, depending upon the type of system fitted, Binding brakes is a common complaint and one that is caused by a number for factors. It may result from a partially sticking bush or a part-seized wheel cylinder, preventing the brake from releasing completely. Alternative causes can be a faulty air release valve, a slow reacting quick-release valve or a sluggish foot valve.
' The speed of brake application and release can be another important consideration. This can be significantly slowed by partial component seizure and weak return springs. Alternatively, a sticking S-cam or air valve, can result in a delayed release.
It is with these sorts of common problem that a rolling road brake tester comes into its own. It can reveal significant fluctuations in braking efficiency which would go unnoticed under conditions of normal operation—common causes being a warped brake disc or ovality of the drum.
Another possible cause of test failure can be insufficient vehicle loading. Don't forget that until the suspension is adequately loaded down the influential load sensing valve will remain inactive and maximum braking efficiency will not be possible. These valves are often vulnerable on vehicles used for off-road applications, so keep an eye on their general condition and state of adjustment too.
Reduced brake efficiency can also be caused by glazed drums or shoes—simply not enough friction—dropping overall performance down below the critical limit, resulting in failure. Worn shoes may have the same effect and brand new ones fitted immediately prior to the test can suffer in a similar way—remember that bedding-in is important and takes time.
Dirt and oil contamination of the friction surfaces is another obvious but all too common occurrence which drastically reduces stopping power. Likewise, the poor fitting of relined shoes or the poor performance of automatic slack adjusters will also lead to problems during testing.
With regard to the air side of the system, bear in mind that the tester will drain the tanks at the start of the test, after which the system will have three minutes to re-charge itself sufficiently—until the low air pressure warning is silenced. Also, if the buzzer sounds during the test itself, a maximum of five minutes will be allowed for the pressure to recover.
PRE-TEST CHECKS
Check for brake binding, if so re-adjust Check drums for ovality and signs of glazing Check operation of load sensing valve If new linings are needed, change well before test Make sure air system is leak-free and efficient Avoid pressure washing brakes prior to test