Power for the future
Page 48
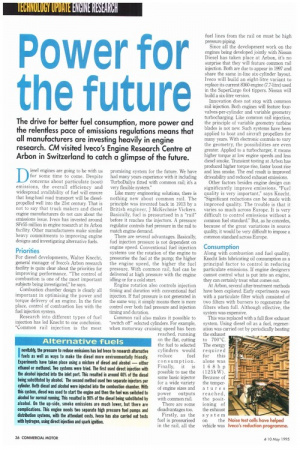
Page 49
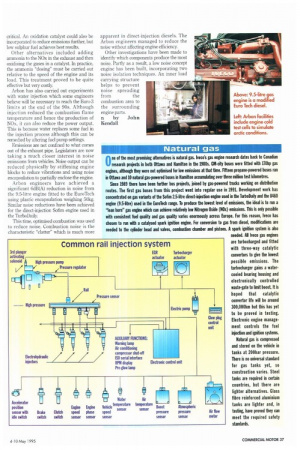
If you've noticed an error in this article please click here to report it so we can fix it.
The drive for better fuel consumption, more power and the relentless pace of emissions regulations means that all manufacturers are investing heavily in engine research. CM visited lveco's Engine Research Centre at Arbon in Switzerland to catch a glimpse of the future.
Diesel engines are going to be with us for some time to come. Despite concerns about particulate (soot) emissions, the overall efficiency and widespread availability of fuel will ensure that long-haul road transport will be dieselpropelled well into the 21st century That is not to say that truck makers and diesel engine manufacturers do not care about the emissions issue. Iveco has invested around SFr55 million in engine research at its Arbon facility. Other manufacturers make similar heavy commitments to improving engine designs and investigating alternative fuels.
Priorities
For diesel developments, Walter Knecht, general manager of Iveco's Arbon research facility is quite clear about the priorities for improving performance. "The control of combustion is one of the most important subjects being investigated," he says.
Combustion chamber design is clearly all important in optimising the power and torque delivery of an engine. In the first place, control of combustion lies with the fuel injection system.
Research into different types of fuel injection has led Knecht to one conclusion. "Common rail injection is the most promising system for the future. We have had many years experience with it including TurboDailys fitted with common rail; it's a very flexible system."
Like many engineering solutions, there is nothing new about common rail. The principle was invented back in 1913 by a British engineer, J McKechnie Vickers. Basically, fuel is pressurised in a "rail" before it reaches the injectors. A pressure regulator controls fuel pressure in the rail to match engine demand.
There are several advantages. Basically, fuel injection pressure is not dependent on engine speed. Conventional fuel injection systems use the rotation of the engine to pressurise the fuel at the pump; the higher the engine speed, the higher the fuel pressure. With common rail, fuel can be delivered at high pressure with the engine idling or for a cold start.
Engine rotation also controls injection timing and duration with conventional fuel injection. If fuel pressure is not generated in the same way, it simply means there is more control over both fuel pressure and injection timing and duration.
Common rail also makes it possible to "switch off" selected cylinders. For example, when motorway cruising speed has been reached, running on the flat, cutting the fuel to selected cylinders would reduce fuel consumption. Finally, it is possible to use the same basic injector for a wide variety of engine sizes and power outputs with common rail.
There are some disadvantages too.
Firstly, as the fuel is pressurised in the rail, all the fuel lines from the rail on must be high pressure piping.
Since all the development work on the engines being developed jointly with Nissan Diesel has taken place at Arbon, it's no surprise that they will feature common rail injection. Both are due to appear in 1997 and share the same in-line six-cylinder layout. Iveco will build an eight-litre variant to replace its current 8360 engine (7.7-litre) used in the SuperCargo 6x4 tippers. Nissan will build a six-litre version.
Innovation does not stop with common rail injection. Both engines will feature fourvalves-per-cylinder and variable geometry turbocharging Like common rail injection, the principle of variable geometry turbine blades is not new. Such systems have been applied to boat and aircraft propellers for many years. With electronic controls to vary the geometry, the possibilities are even greater. Applied to a turbocharger, it means higher torque at low engine speeds and less diesel smoke. Transient testing at Arbon has produced higher torque rise, faster boost rise and less smoke. The end result is improved driveability and reduced exhaust emissions.
Other factors besides engine design can significantly improve emissions. "Fuel quality is very important," says Knecht. "Significant reductions can be made with improved quality. The trouble is that it varies so much across Europe. It is very difficult to control emissions without a common fuel standard." But, as he concedes, because of the great variations in source quality, it would be very difficult to impose a common standard across Europe.
Consumption
Along with combustion and fuel quality, Knecht lists lubricating oil consumption as a principal factor to control in reducing particulate emissions. If engine designers cannot control what is put into an engine, they can certainly treat what comes out.
At Arbon, several after-treatment methods have been explored. Early experiments were with a particulate filter which consisted of two filters with burners to regenerate the filters when full. Although effective, the system was expensive.
on the vehicle was critical. An oxidation catalyst could also be incorporated to reduce emissions further, but low sulphur fuel achieves best results.
Other alternatives included adding ammonia to the NOx in the exhaust and then oxidising the gases in a catalyst In practice, the ammonia "dosing" must be carried out relative to the speed of the engine and its load. This treatment proved to be quite effective but very costly.
Arbon has also carried out experiments with water injection which some engineers believe will be necessary to reach the Euro-3 limits at the end of the 90s. Although injection reduced the combustion flame temperature and hence the production of NOx, it can also reduce the power output. This is because water replaces some fuel in the injection process although this can be remedied by altering fuel pump settings.
Emissions are not confined to what comes out of the exhaust pipe. Legislators are now taking a much closer interest in noise emissions from vehicles. Noise output can be reduced physically by stiffening engine blocks to reduce vibrations and using noise encapsulation to partially enclose the engine.
Arbon engineers have achieved a significant 6dB(A) reduction in noise from the 9.5-litre engine fitted to the EuroTech using plastic encapsulation weighing 50kg. Similar noise reductions have been achieved for the direct-injection Sofim engine used in the TurboDaily.
This time, optimised combustion was used to reduce noise. Combustion noise is the characteristic "clatter" which is much more apparent in direct-injection diesels. The Arbon engineers managed to reduce the noise without affecting engine efficiency.
Other investigations have been made to identify which components produce the most noise. Partly as a result, a low noise concept engine has been built, incorporating two noise isolation techniques. An inner load carrying structure helps to prevent noise spreading from the combustion area to the surrounding engine parts.
n by John Kendall