Standards represent flags of quality, and also risk mitigation. CM looks at the benefits they can bring to a haulier.
Page 46
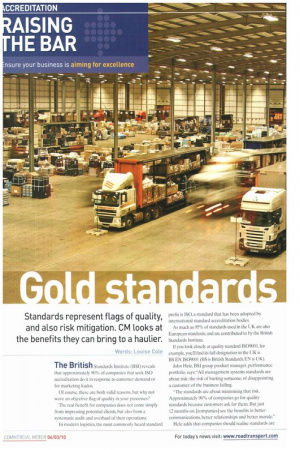
Page 47
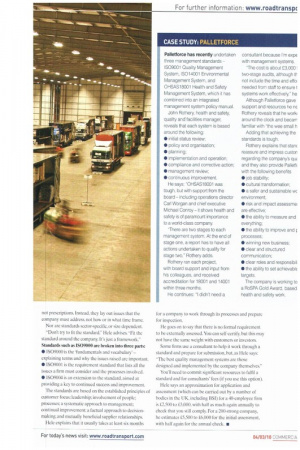
If you've noticed an error in this article please click here to report it so we can fix it.
Words: Louise Cole The British Standards Institute (BSI) reveals that approximately 90% of companies that seek ISO accreditation do it in response to customer demand or for marketing kudos.
Of course. these arc both valid reasons, but why not wave an objective flag of quality in your processes?
The real benefit for companies does not come simply from impressing potential clients, but also from a systematic audit and overhaul of their operations.
In modern logistics, the most commonly heard standard prefix is ISO. a standard that has been adopted by international standard accreditation bodies.
As much as 95% of standards used in the UK are also European standards, and are contributed to by the British Standards Institute.
If you look closely at quality standard 1S0900 I. for example, you'll find its full designation in the UK is BS EN IS09001 (BS is British Standards. EN is UK).
John Hele, BSI group product manager, performance portfolio. says; "All management systems standards are about risk; the risk of hurting someone: of disappointing a customer; of the business failing.
"The standards arc about minimising that risk. Approximately 90% of companies go for quality standards because customers ask for them. But just 12 months on. 'companies] see the benefits in better communications, better relationships and better morale."
Fide adds that companies should realise standards are
not prescriptions Instead, they lay out issues that the company must address, not how or in what time frame.
Nor are standards sector-specific. or size dependent.
"Don't try to fit the standard." Hele advises. "Fit the standard around the company. It's just a framework." Standards such as 1S09000 are broken into three parts: • IS09000 is the 'fundamentals and vocabulary' explaining terms and why the issues raised are important.
• IS09001 is the requirement standard that lists all the issues a firm must consider and the processes involved.
• IS09004 is an extension to the standard, aimed at providing a key to continued success and improvement.
The standards are based on the established principles of customer focus: leadership; involvement of people; processes; a systematic approach to management; continual improvement: a factual approach to decisionmaking: and mutually beneficial supplier relationships.
Hele explains that it usually takes at least six months for a company to work through its processes and prepare for inspection.
He goes on to say that there is no formal requirement to be externally assessed. You can self-certify, but this may not have the same weight with customers or investors.
Some firms use a consultant to help it work through a standard and prepare for submission, but, as Hele says: "The best quality management systems are those designed and implemented by the company themselves."
You'll need to commit significant resources to fulfil a standard and for consultants' fees (if you use this option).
Hele says an approximation for application and assessment (which can be carried out by a number of bodies in the IJK. including BSI) for a 40-employee firm is £2,500 to £3,000. with half as much again annually to check that you still comply. For a 200-strong company, he estimates £5,500 to £6,000 for the initial assessment, with half again for the annual check. •