Fire engine design — which way ?
Page 58
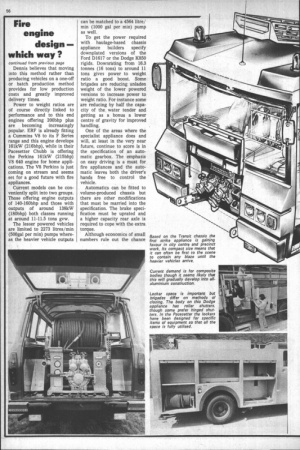
Page 59
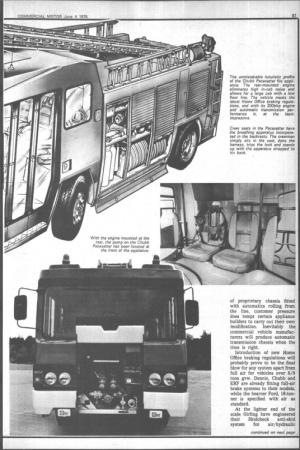
If you've noticed an error in this article please click here to report it so we can fix it.
continued from previous page
Dennis believes that moving into this method rather than producing vehicles on a one-off or batch production method provides for low production costs and greatly improved delivery times.
Power to weight ratios are of course directly linked to performance and to this end engines offering 200bhp plus are becoming increasingly popular. ERF is already fitting a Cummins V8 to its F Series range and this engine develops 161kW (216bhp), while in their Pacesetter Chubb is offering the Perkins 161kW (215bhp) V8 640 engine for home applications. The V8 Perkins is just coming on stream and seems set for a good future with fire appliances.
Current models can be conveniently split into two groups. Those offering engine outputs of 140-160bhp and those with outputs of around 138kW (180bhp) both classes running at around 11-11.5 tons gvw.
The lesser powered vehicles are limited to 2273 litres/min (500gal per min) pumps whereas the heavier vehicle outputs can be matched to a 4564 litre/ min (1000 gal per min) pump as well.
To get the power required with haulage-based chassis appliance builders specify downplated versions of the Ford D1617 or the Dodge K850 rigids. Downrating from 16.3 tonnes (16 tons) to around 11 tons gives power to weight ratio a good boost. Some brigades are reducing unladen weight of the lower powered versions to increase power to weight ratio. For instance some are reducing by half the capacity of the, water tender and getting as a bonus a lower centre of gravity for improved handling.
One of the areas where the specialist appliance does and will, at least in the very near future, continue to score is in the specification of an automatic gearbox. The emphasis on easy driving is a must for fire appliances and the automatic leaves both the driver's hands free to control the vehicle.
Automatics can be fitted to volume-produced chassis but there are other modifications that must be married into the specification. The brake specification must be uprated and a higher capacity rear axle is required to cope with the extra torque.
Although economics of small numbers rule out the chance
Based on the Transit chassis the first strike appliance is gaining favour in city centre and precinct work. Its compact size means that it can often be first to the scene to contain any blaze until the heavier vehicles arrive.
Locker space is important but brigades differ on methods of closing. The body on this Dodge appliance has roller shutters, though some prefer hinged shutters. In the Pacesetter the lockers have been designed for specific items of equipment so that all the space is fully utilised. The unmistakable futuristic profile of the Chubb Pacesetter fire appliance. The rear-mounted engine eliminates high in-cab noise and allows for a large cab with a low floor line. The vehicle meets the latest Home Office braking regulations, and with its 200bhp engine and automatic transmission performance is, at the least, impressive.
Crew seats in the Pacesetter have the breathing apparatus incorporated in the backrests The crewman simply sits in the seat, dons the harness, trips the lock and stands up with the apparatus strapped to hit back.
of proprietary chassis fitted with automatics rolling from the line, customer pressure does tempt certain appliance builders to carry out their own modification. Inevitably the commercial vehicle manufacturers will produce automatic transmission chassis when the time is right.
Introduction of new Home Office braking regulations will probably prove to be the final blow for any system apart from full air for vehicles over 8/9 tons gvw. Dennis, Chubb and ERF are already fitting full-air brake systems to their models, while the heavier Ford, 16-tonner is specified with air as standard.
At the lighter end of the scale Girling have engineered their Skidcheck anti-skid system for air/hydraulic