Light Alloys for Commercial Bodies
Page 52
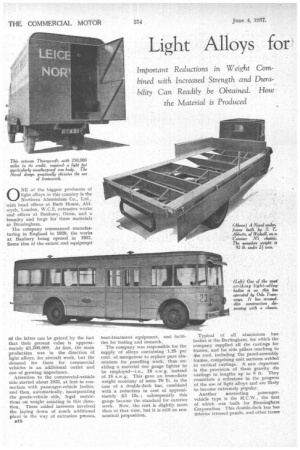
Page 53
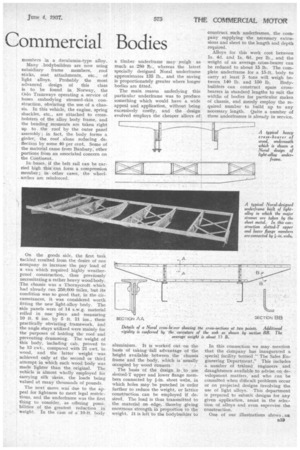
Page 54
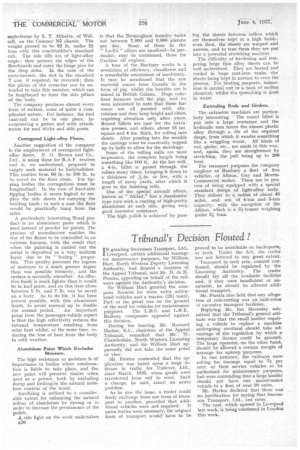
If you've noticed an error in this article please click here to report it so we can fix it.
0 NE of the biggest producers of light alloys in this country is the Northern Aluminium Co., Ltd., with head offices at Bush House, Aldwych, London, W.C.2, extensive works and offices at Banbury, Oxon, and a foundry and forge for these materials at Birmingham.
The company commenced manufacturing in England in 1928, the works at Banbury being opened in 1931. Some idea of the extent and equipment of the latter can be gained by the fact that their present value is approximately L1,500,000. At first, the main production was in the direction of light alloys, for aircraft work, but the demand for these for commercial vehicles is an additional outlet and one of growing importance.
Attention to the commercial-vehicle side started about 1933, at first in connection with passenger-vehicle bodies, and then, automatically, incorporating the goods-vehicle side, legal restrictions on weight assisting in this direction. These added interests involved the laying down of much additional plant in the way of extrusion presses, B18
heat-treatment equipment, and facilities for testing and research.
The company was responsible for the supply of alloys containing 1.25 per cent, of manganese to replace pure aluminium for panelling work, thus enabling a material one gauge lighter to be employed—i.e., 19 s.w.g. instead of 18 s.w.g. This gave an immediate weight economy of some 70 lb. in the case of a double-deck bus, combined with a reduction in cost of approximately £.3 15s.; subsequently this gauge became the standard for exterior work. Now, the cost is slightly more than at that time, but it is still an economical proposition.
Typical of all aluminium bus bodies is the Burlingham, for which the company supplied all the castings for frames, and for side pillars reaching to the roof, including the panel-assembly frames, comprising unit sections welded to vertical castings. A new departure is the provision of these gravity die castings in lengths up to 8 ft. They constitute a milestone in the progress of the use of light alloys and are likely to become extremely Popular.
Another interesting passengervehicle type is the M.C.W., the first of which was built for Birmingham Coiporation. This double-deck bus has intelior stressed panels, and other frame
members in a duralumin-type alloy.
Many bodybuilders are now using subsidiary frame members, roof sticks, seat attachments, etc., of light alloys. Probably the most advanced design of this class is to be found in Norway, the Oslo Tramways operating a service of buses embodying stressed-skin construction, obviating the use of a chassis. In this vehicle, the engine, spring shackles, etc., are attached to crossbolsters of the alloy body frame, and the bending moments are taken right up to the roof by the outer panel assembly ; in fact, the body forms a girder, the roof alone reducing deflection by some 40 per cent. Some of the material came from Banbury, other portions from an associated concern on the Continent.
In buses, if the belt rail can be carried high this can form a compression member ; in other cases, the wheelarches are reinforced.
On the goods side, the first task tackled resulted from the desire of one company to increase the pay load of a van which required highly weatherproof construction, thus previously necessitating a rather heavy wood body. The chassis was a Thornycroft which had already run 250,000 miles, but its condition was so good that, in the circumstances, it was considered worth . fitting the new light-alloy body. The side panels were of 14 s.w.g. material rolled in one piece and measuring 10 ft. 6 ins. by 5 ft. 11 ins., these practically obviating framework, and the angle stays utilized were mainly for the purposes of holding the roof and preventing. drumming. The weight of this body, including cab, proved to be la cwt., compared with 21 cwt. in wood, and the latter weight was achieved only at the second or third attempt in which each wood body was made lighter than the original. The vehicle is almost wholly employed for carrying silk skein, the loads being valued at many thousands of pounds.
The next move was due to the appeal for lightness to meet legal restrictions, and the underframe was the first thing to consider, as offering possibilities of the greatest reduction in weight. In the case of a 10-ft. body a timber underframe may weigh as much as 280 lb., whereas the latest specially designed Noral underframe approximates 135 lb., and the saving is proportionately greater where longer bodies are fitted.
The main reason underlying this particular underframe was to produce something which would have a wide appeal and application, without being excessively costly, and the design evolved employs the cheaper alloys of aluminium, It is worked out, on the basis of taking-'full advantage of the height available between , the chassis frame and the body, Nvhich is usually occupied by wood runners.
The basis of the design is to use slotted-T upper and lower flange mem bers connected by sheet webs, in which holes may be punched in order further to reduce the weight, or lattice construction can be employed if desired, The load is thus transmitted to the material on edge, thereby giving enormous strength in proportion to the weight. It is left to the bodybuilder to construct such underframes, the company supplying the necessary extrusions and sheet to the length and depth required.
Alloys for this work cost between 1s. 4d. and 1s. ficl. per lb., and the weight of an average cross-bearer can be reduced to about 15 lb. The complete underframe for a 15-ft. body to carry at least 5 tons will weigh be
tween 140 lb. and 150 lb. Bodybuilders can construct spare crossbearers in standard lengths to suit the widths of bodies for particular makes of chassis, and merely employ the required number to build up to any necessary length. Quite a number of these underframes is already in service.
In this connection we may. mention that the Company has inaugurated a , special facility termed "The Sales Engineering Department." This includes a number of trained engineersand draughtsmen available to advise on development matters, and who can be consulted when difficult prCiblems occur or on projected designs involving the use of light alloys. This department is prepared to submit designs for any given application, assist in the selection of alloys and even supervise the construction.
One of our illustrations shOws r, an B19
nnderframe by S. T. Abbotts, of Walsall, on the Commer N5 chassis. The weight proved to be 92 lb. under 21 tons with this coachbuilder's standard cab. The side sills are of light-alloy angle ; they protect the edges of the floorboards and carry the hinge pins for the drop sides. In the case of the cross-bearers, the slot in the standard T can, if required, be reversed; then the plates of the cross-bar can be extended to take this member, which can be lengthened to form the side pillars of the body.
The company produces almost every form of section, some of quite a complicated nature. For instance, the roof cant-rail can be in one piece, incorporating a gutter and with attachments for roof sticks and side posts.
Corrugated Light-alloy Floors. .
Another suggestion of the company is the employment of corrugated lightalloy floors. E. G. Brown and Co., Ltd., is using these for R.A.F. tenders and is, we understand, prepared to supply such material to bodybuilders. This enables from 60 lb. to 100 lb. to be saved on the floor alone. For tipping bodies the corrugations must be longitudinal. In the case of fixed-side tipping bodies it seems logical to employ the side sheets for carrying the bending loads ; in such a case the floor would be practically hung from the sides.
A particularly interesting NoraI product is an aluminium paste which is used instead of powder for paints. The process of manufacture enables the size of the flakes to be controlled to an extreme fineness, with the result that when the painting is carried out the metal is deposited as a very uniform layer, 'due to its " leafing " properties. This quality prevents the ingress of moisture to a much greater degree than was possible formerly, and the surface is naturally smoother. An effective finish is much lighter than it would be in lead paint, and on this item alone between 5 lb. and 7 lb. can be saved on a body. As to its life, it has been proved possible, with this aluminium finish, to avoid renewal up to double
the normal period. An important point from the passenger-vehicle aspect is that the high reflectivity reduces the internal temperature resulting from solar heat whilst, at the same time, reducing the loss of heat from the body in cold weather.
Aluminium Paint Which Excludes Moisture.
The high resistance to moisture is of importance in bodies where condensation is liable to take place, and the new paint will preserve timber when used as a primer, both by excluding damp and locking-in the natural moisture content of the wood.
Anodizing is utilized to a considerable extent for enhancing the natural colour of aluminium by dyeing or in order to increase the permanence of the polish.
Aside light on the work undertaken B20 is that the Birmingham foundry turns out between 7,000 and 8,000 pistons per day. Many of these in the " Lo-Ex" alloys are anodized—in particular, may be mentioned, those for Gardner oil engines.
A tour of the Banbury works is a revelation of efficiency,' cleanliness and a remarkable assortment of machinery. It may be mentioned that the raw material comes from Canada in the form of pig. whilst the bauxite ore is mined in British Guiana. Huge cokefired furnaces melt the pigs, and we were interested to note that these furnaces are all painted with aluminium and they keep bright and clean, requiring attention only after years. Round billets are cast for the extrusion presses, and others, about 18 ins. square and 4 ins, thick, for rolling into sheets. After pouring into the moulds the castings must be constantly topped up by ladle to allow for the shrinkage.
Some of the rolling mills are most impressive, the complete length being something like 100 ft. At the hot mill, a 4-in, billet is passed through the rollers many times, bringing it down to a thickness of A-in. or less, with a length of many yards, after which it goes to the finishing rolls.
One of the special aircraft alloys, known as " Alclad," has a duralumintype core with a coating of high-purity aluminium at each side, giving very good corrosive resistance.
The high polish is achieved by pass ing the sheets between rollers which are themselves kept at a high finish ; even then, the sheets are warped and uneven, and to true them they are put into a powerful stretching machine.
The difficulty of hardening and tempering large thin alloy sheets can be well understood. They are heated and cooled in huge cast-iron tanks, the sheets being kept in motion to even the process. For heating purposes, immersion is carried out in a tank of molten chemical, whilst the quenching is done in water.
Extruding Rods and Girders.
The extrusion machines are particularly interesting. The round billet is put into a large container and the hydraulic ram forces the almost plastic alloy through a die of the required shape, from which it exudes soniething like a wriggling wOrm. All kinds of rod, girder, etc., are made in this way, and, again, they are straightened by stretching, the pull being up to 200 tons.
For transport purposes the company employs at Banbury a fleet of five vehicles, of Albion, Guy and MorrisCommercial makes. These are in process of being equipped with a special standard design of light-alloy body. They deliver to a radius of about 45 miles, and are of 4-ton and 5-ton capacity, with the exception of the Albion, which is a 51-tanner weighing under 21 tons.