Ingenious Design in NEW REAR-ENGINED CHASSIS D URING the past few
Page 39
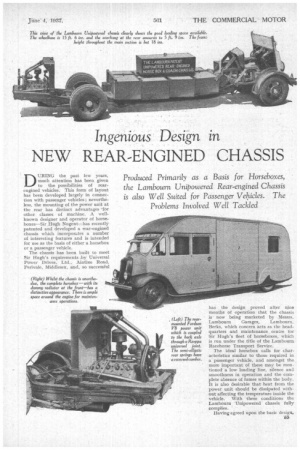
Page 40
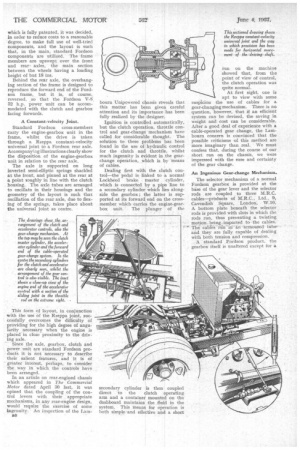
Page 41
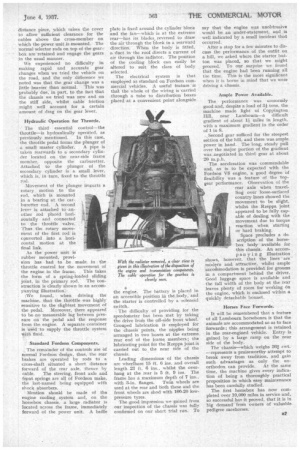
If you've noticed an error in this article please click here to report it so we can fix it.
years, much attention has been given to the possibilities of rearengined vehicles. This form of layout has been developed largely in connection with passenger vehicles ; nevertheless, the mounting of the power unit at the rear has distinct advantages for other classes of machine. A wellknown designer and operator of horseboxes—Sir Hugh Nugent—has recently patented and developed a rear-engined chassis which incorporates a number of interesting features and is intended for use as the basis of either a horsebox or a passenger vehicle.
The chassis has been built to meet Sir Hugh's requirements by Universal Power Drives, Ltd., Ainfree Road, Perivale, Middlesex, and, so successful has the design proved after nine months of operation that the chassis is now being marketed by Messrs. Lambourn Garages, Lambourn, Berks, which concern acts as the headquarters and maintenance ceM:re for Sir Hugh's fleet of horseboxes, which is run under the title of the Lambourn Racehorse Transport Service.
The ideal horsebox calls for characteristics similar to those required in a pa,ssenger vehicle, and amongst the more important of these may be mentioned a low loading line, silence and smoothness in operation and the complete absence of fumes within the body. It is also desirable that heat from the power unit should be dissipated without affecting the temperature inside the vehicle. With these conditions the Lambourn Unipowered chassis fully complies.
Having agreed upon the basic design, which is fully patented, it was decided, in order to reduce costs to a reasonable degree, to make full use of well-tried components, and the layout is such that, in the main, standard Fordson components are utilized. The frame members are upswept over the front and rearaxles, the main section between the wheels having a loading height of but 18 ins.
Behind the rear axle, the overhanging section of the frame is designed to reproduce the forward end of the Fordson frame,. but it is, of course, reversed, .so that the Fordson V-8 32 h.p. power unit can be accommodated with the clutch and gearbox facing forwards.
A Constant-velocity joint.
Standard Fordson cross-members carry the engine-gearbox unit in the frame, whilst the drive is taken through a Rzeppa constant-velocity universal joint to a Fordson rear axle. Accompanying illustrations clearly show the disposition of the engine-gearbox unit in relation to the rear axle.
The axle is supported on long inverted semi-elliptic springs shackled at the front, and pinned at the rear at a point -toughly in line with the clutch housing. The axle tubes are arranged to oscillate in their housings and the geometry of the layout is such that oscillation of the rear axle, due to flexing of the springs, takes place about the universal joint as centre.
This form of layout, in conjunction with the use of the Rzeppa joint, successfully o-vercomes the difficulty of providing for the high degree of angularity necessary when the engine is
• placed in dose proximity to the driv ing axle. .
Since the axle, gearbox, clutch and power unit are standard Fordson product's it is not necessary to describe their salient features, and it is Of greater interest, Perhaps, to consider the way in which the controls have been arranged.
In an article on rear-engiued chassis which appeared in The Commercial Motor dated April 30 last, it was opined that the coupling of the control levers with their appropriate mechanisms, in any rear-engine design, would require the exercise of some Ingenuity. An inspection of the La:11
• '36 bourn Unipowered chassis rbveals that this matter has been given careful attention and its importance has been fully realized by the designer.
Ignition is controlled automatically, but the clutch operation, throttle control and gear-change mechanism have called for considerable thought. The solution to these problems has been found in the use of hydraulic control for the clutch and throttle, whilst much ingenuity is evident in the gearchange operation, which is by means of cables.
Dealing first with the clutch control—the pedal is linked to a normal Lockheed brake master cylinder, which is connected by a pipe line to a secondary cylinder which lies alongside the gearbox ; the latter is supported at its forward end on the crossmember which carries the engine-gearbox unit. The plunger of the•
run on the machine showed that, from the point of view of control, the clutch operation was quite normal.
At first sight, one is apt to view with some suspicion the use of cables for a gear-changing mechanism. There is no question, however, that if an efficient system can be devised, the saving in weight and cost can be considerable. After a good deal of experienee with a cable-operated gear change, the Lambourn concern is convinced that the possible criticisms of this method are more imaginary than real. We must confess that, during the course of our short run on the chassis, we were impressed with the ease and certainty of the gear change.
An Ingenious Gear-change Mechanism.
The selector mechanism of a normal Fordson gearbox is provided at the base' of the gear lever and the selector rods are coupled to three M.R.C. cables—prOducts of Ltd., 9, Cavendish Square, London, W.10. A bottom plate beneath the selector rods is provided with slots in which the rods run, thus preventing a twisting motion being imparted to the cables.
The cables ari armoured fube)and they are fully capable of dealing with both tension and compression.
. A standard Fordson product,. the gearbox itself is unaltered except for a
distance piece, which raises the cover to allow sufficient clearance for the cables above the cross-member on .which the power unit is mounted. The normal selector rods on top of the gearbox are retained and engage the gears in the usual manner.
We experienced no difficulty in making rapid and accurate gear changes when we tried the vehicle on the road, and the only difference we noted was that the gear change was a little heavier than normal. This was probably due, in part, to the fact that the chassis we tried was new and on the stiff side, whilst cable friction might well account for a certain amount of drag on the gear lever.
• Hydraulic Operation for Throttle.
The third essential control—the throttle—is hydraulically operated, as
previously mentioned. In this case, the throttle pedal forms the plunger of a small master cylinder. A pipe is taken rearwards to a secondary cylinder located on the near-side frame member, opposite the carburetter. Attached to the plunger of the secondary cylinder is a small lever, which is, in turn, fixed to the throttle rod.
Movement of the plunger imparts a rotary motion to the rod, which is mounted in a bearing at the carburetter end. A second lever is attached to -another rod placed horizontally and connected to the throttle valve. Thus the rotary movement of the first rod is converted into a horizontal motion at the final link.
As the power unit is rubber mounted, provision has had to be made in the throttle control for the movement of the engine in the frame. This takes the form of a spring-loaded sliding joint, in the primary rod. The construction is clearly shown in an accompanying illustration.
We found, when driving the machine, that the throttle was highly sensitive to the slightest movement of the pedal. Moreover, there appeared to be• no measurable lag between piessure on the pedal and the response from the engine. A separate container is used to supply the throttle system With fluid.
Standard Fordson Components.
The remainder of the controls are Of normal Fordson design, thus, the rear brakes are operated by rods to a cross-shaft situated a short distance forward of the rear axle, thence by
cable. The steering, front axle and front springs are all of Fordson make, the last-named •being equipped with shock absorbers.
Mention should be made of the engine cooling system and, on the horsebox chassis, a large radiator is located across the frame, immediately forward of the power unit. A baffle plate is fixed around the cylinder block and the fan—which is at the extreme rear—has its blades, reversed to draw the air through the block in a rearward direction. When the body is fitted, a duct in the roof directs a current of air through the radiator. The position of the cooling block can easily be altered to suit the class of body selected.
The electrical system is that employed as standard on Fordson commercial vehicles. A usreful feature is that the whole of the wiring is carried through a tube to distribution boxes placed at a convenient point alongside the engine. The battery is placed in an accessible pOsition in the ,body and the starter is controlled by a solenoid switch.
The difficulty of providing for the speedometer has been met by taking the drive from the off-side front wheel. Grouped lubrication is employed for the chassis points, the nipples being arranged in two boxes at the extreme rear end of the frame members; the lubricating point for the Rzeppa joint is carried out to the near side of the chassis.
Leading dimensions of the chassis are wheelbase 15 ft. 6 ins, and overall length 23 ft. 6 ins., whilst the overhang at the rear is 5 ft. 9 ins. The frame has a maximum depth of 7 ins.,
with 3-in. flanges. Twin wheels are used at the rear and lioth these and the front wheels are shod with 100-20 lowpressure tyres.
The good impression we gained from our inspection of the chassis was fully confirmed on our short trial run. To
say that the engine was unobtrusive would be an under-statement, and is well indicated by a small incident that occurred.
After a stop for a few minutes to discuss the performance of the outfit on a hill, we asked where the starter button was placed, so that we might proceed. To our surprise we found that the engine had been running all the time. This is the more significant when it is borne in mind that we were driving a chassis.
Ample Power Available.
The performance was unnormly good and, despite a load of 3i tons, the machine made light of Coppington Hill, near Lambourn—a difficult gradient of about 1A miles in length. with a maximum gradient in the order of 1 in S.
Second gear sufficed for the steepest seetion of the hill, and there was ample power in hand. The long, steady pull over the major portion of the gradient was .negotiated in third gear at about 20 mph.
The acceleration was commendable and, as is to be expected with the Fordson VS engine, a good degree bf flexibility was a feature of the top gear performance. Observation of the rear axle when travelling over loose-surfaced country lanes showed the movement to be slight, whilst the Rzeppa joint appeared to be fully capable of dealing with the movement due to torque reaction when startin or hard braking.
Space precludes a de. scription of the horsebox body available for this chassis. An accompanying illustration shows, however, that the lines are modern and attractive, whilst ample a.ccorlimodation is provided for grooms in a compartment behind the driver. Good luggage space is available and the full width of the body at the rear leaves plenty of room for working on the engine, which is enclosed within a quickly detachable bonnet.
Horses Face Forwards.
It will be remembered that a feature of all Lambourn horseboxes is that the animals are accommodated so as to face forwards; this arrangement is retained in the rear-engined vehicle. Entry is gained by a large ramp on the near side of the body.
The chassis—which weighs 36i cwt. —represents a praiseworthy attempt to break away from tradition, and gain such advantages as only the unorthodox can provide. At the same time, the machine gives every indication of being a thoroughly practical proposition in which easy maintenance has been carefully studied.
The first horsebox has now completed over 10,000 miles in service and, so successful has it proved, that it is in big demand from owners of valuable pedigree racehorses.