Phoenix steers a revolutic
Page 19
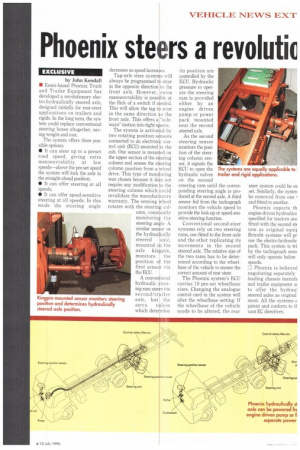
If you've noticed an error in this article please click here to report it so we can fix it.
EXCLUSIVE
by John Kendall • Essex-based Phoenix Truck and Trailer Equipment has developed a revolutionary electro-hydraulically steered axle, designed initially for rear-steer applications on trailers and rigids. In the long term, the system could replace conventional steering boxes altogether, saving weight and cost.
The system offers three possible options: • It can steer up to a preset road speed, giving extra manoeuvrability at low speeds—above the pre-set speed the system will lock the axle in the straight ahead position; • It can offer steering at all speeds; • It can offer speed-sensitive steering at all speeds. In this mode the steering angle decreases as speed increases.
Tag-axle steer systenis will always be programmed tO steer in the opposite direction to the front axle. However, lextra manoeuvrability is possible at the flick of a switch if needed. This will allow the tag to steer in the same direction as the front axle. This offers a "sideways" motion into tight spaces.
The system is activated by two rotating position sensors connected to an electronic control unit (ECU) mounted in the cab. One sensor is mounted on the upper section of the steering column and senses the steering column position from a wheel drive. This type of monitoring was chosen because it does not require any modification to the steering column which could invalidate the manufacturers warranty. The sensing wheel rotates with the steering column, constantly monitoring the steering ankle. A similar senior on the hydraulically steered Iaxle, mounted dn the axle kingpin,
monitors the position of the first sensor via the ECU.
A conventional hydraulic steering ram steers the second/trailer axle, but the servo valves which determine its position are controlled by the ECU. Hydraulic pressure to operate the steering ram is provided either by an engine driven pump or power pack mounted near the second steered axle.
As the second steering sensor monitors the position of the steering column sensor, it signals the ECU to open the hydraulic valves on the second steering ram until the corresponding steering angle is produced at the second axle. A third sensor fed from the tachograph monitors the vehicle speed to provide the lock-up or speed-sensitive steering function.
Conventional second-steer systems rely on two steering rams, one fitted to the front axle and the other replicating its movements in the second steered axle. The relative size of the two rams has to be determined according to the wheelbase of the vehicle to ensure the correct amount of rear steer.
The Phoenix system's ECU carries 10 pre-set wheelbase sizes. Changing the analogue control card in the system will alter the wheelbase setting. If the wheelbase of the vehicle needs to be altered, the rear
steer system could be ea set. Similarly, the systen be removed from one and fitted to another.
Phoenix expects th engine-driven hydraulics specified for tractors anc fitted with the second stt tern as original equil Retrofit systems will pr use the electro-hydraulic pack. This system is tri by the tachograph sens will only operate below speeds.
0 Phoenix is believed negotiating separately leading chassis manufa and trailer equipment si to offer the hydraul steered axles as original ment. All the systems c patent and conform to if vant EC directives.