Massive movement needs
Page 66
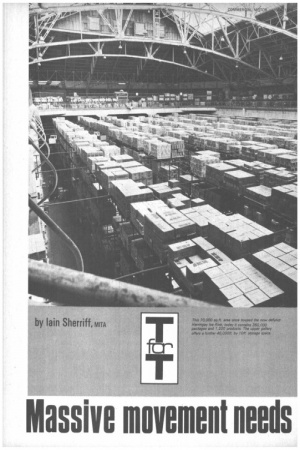
Page 67
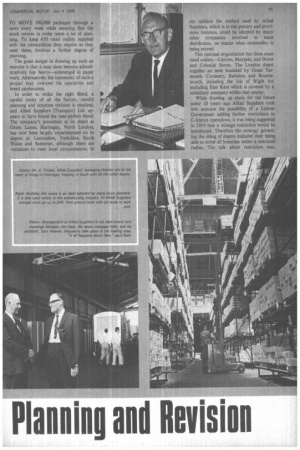
Page 68
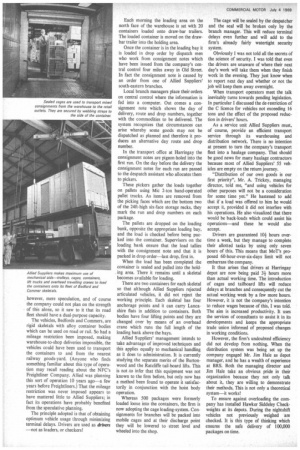
If you've noticed an error in this article please click here to report it so we can fix it.
Planning and Revision by lain Sherriff, MITA
TO MOVE 100,000 packages through a store every week while ensuring that the stock rotates in order takes a lot of planning. To keep 450 retail outlets supplied with the commodities they require as they need them, involves a further degree of planning.
The great danger in drawing up such an xercise is that it may soon become administratively top heavy—submerged in paper work..Alter natively the immensity of such a project may overawe the operatives and breed carelessness.
In order to strike the right blend, a careful study of all the factors, careful planning and constant revision is required, and Allied Suppliers (Transport) Ltd. appears to have found the near-perfect blend. The company's procedure at its depot at Green Lanes, Harringay, North London, has now been largely superimposed on its depots at Lancashire, Yorkshire, South Wales and Somerset, although there are variations to meet local circumstances. In my opinion the method used by Allied Suppliers, which is in the grocery and pro sions business, could be adopted by in other companies involved in mass distribution, no matter what commodity being moved.
This national organization has three main retail outlet s--Liptons, Maypole. and Home and Colonial Stores. The London supplies an area bounded by Grea mouth, Coventry, Swindon and Bo mouth, including the Isle of Wight excluding East Kent which is covered b subsidiary company within that county.
While drawing up plans for the fut some 10 years ago Allied Suppliers t into account the possibility of a La Government adding further restrictions C-licence operations; it was being suggest in 1959 that a mileage restriction would be introduced. Therefore the strategy governing the siting of depots included their b able to cover all branches within a restrict radius. The talk about restriction was.
however, mere speculation, and of course the company could not plan on the strength of this alone, so it saw to it that its road fleet should have a dual-purpose capacity.
The vehicles, Bedfords and Cornmers, are rigid skeletals with alloy container bodies which can be used on road or rail. So had a mileage restriction been imposed, making warehouse-to-shop deliveries impossible, the vehicles could have been used to transport the containers to and from the nearest railway goods-yard. (Anyone who finds something familiar about this type of operation may recall reading about the NFC's Freightliner Company. Allied was planning this sort of operation 10 years ago—a few years before Freightliners.) That the mileage restriction was never imposed appears to have mattered little to Allied Suppliers; in fact its operations have probably benefited from the speculative planning.
The principle adopted is that of obtaining optimum vehicle usage through minimizing terminal delays. Drivers are used as drivers —not as loaders, or checkers!
Each morning the loading area on the north face of the warehouse is set with 20 containers loaded onto draw-bar trailers. The loaded container is moved on the drawbar trailer into the holding area.
Once the container is in the loading bay it is loaded in drop order by dispatch men who work from consignment notes which have been issued from the company's central control four miles away in Old Street. In fact the consignment note is caused by an order from one of Allied Suppliers' south-eastern branches.
Local branch managers place their orders on central control where the information is fed into a computer. Out comes a consignment note which shows the day of delivery, route and drop numbers, together with the commodities to be delivered. The system recognizes that circumstances can arise whereby some goods may not be dispatched as planned and therefore it produces an alternative day route and drop number.
In the transport office at Harringay the consignment notes are pigeon-holed into the first run. On the day before the delivery the consignment notes for each run are passed to the despatch assistant who allocates them to pickers.
These pickers gather the loads together on pallets using Mic 2-ton hand-operated pallet trucks. As items are removed from the picking faces which are the bottom two of the 2411-high six-face storage racks, they mark the run and drop numbers on each package.
The pallets are dropped on the loading bank, opposite the appropriate loading bay, and the load is checked before being packed into the container. Supervisors on the loading bank ensure that the load tallies with the consignment note and that it is packed in drop order—last drop, first in. When the load has been completed the container is sealed and pulled into the hold_ ing area. There it remains until a skeletal becomes available for loading.
There are two containers for each skeletal so that although Allied Suppliers rejected articulated vehicles, it did not reject the working principle. Each skeletal has four anchorage points and it can carry Lancashire flats in addition to containers. Both bodies have four lifting points and they are changed over by means of an overhead crane which runs the full length of the loading bank above the bays.
Allied Suppliers' management intends to take advantage of improved techniques and this applies equally to mechanical handling as it does to administration. It is currently studying the separate merits of the Burtonwood and the Ratcliffe tail-board lifts. This is not to infer that this equipment was not known to the firm before, but only now has a method been found to operate it satisfactorily in conjunction with the hoist body operation.
Whereas 500 packages were formerly loaded loose into the containers, the firm is now adopting the cage loading-system. Consignments for branches will be packed into mobile cages and at their discharge point they will be lowered to street level and wheeled into the shop. The cage will be sealed by the despatcher and the seal will be broken only by the branch manager. This will reduce terminal delays even further and will add to the firm's already fairly watertight security system.
Obviously I was not told all the secrets of the science of security. I was told that even the drivers are unaware of where their next day's work will take them when they finish work in the evening. They just know when to report next day and whether or not the job will keep them away overnight.
When transport operators meet the talk inevitably turns towards pending legislation. In particular I discussed the de-restriction of the C licence for vehicles not exceeding 16 tons and the effect of the proposed reduction in drivers' hours.
As a service unit Allied Suppliers must, of course, provide an efficient transport service through its warehousing and distribution network. There is no intention at present to turn the company's transport fleet into a haulage company. That should be good news for many haulage contractors because most of Allied Suppliers' 55 vehicles are empty on the return journey.
"Distribution of our own goods is our first priority", Mr. A. Trickey, managing director, told me, "and using vehicles for other purposes will not be a consideration for some time yet." He hastened to add that if a load was offered to him he would accept it, provided it did not interfere with his operations. He also visualized that there would be back-loads which could assist his operations—and these he would also accept.
Drivers are guaranteed 10+ hours overtime a week, but they manage to complete their allotted tasks by using only seven hours of this. This means that MoT's proposed 60-hour-over-six-days limit will not embarrass the company.
It thus arises that drivers at Harringay depot are now being paid 3+ hours more than actual working time. The introduction of cages and tailboard lifts will reduce delays at branches and consequently cut the actual working week by a few more hours. However, it is not the company's intention to reduce wages because of this, I was told. The aim is increased productivity. It uses the services of consultants to assist it in its developments and keeps the appropriate trade union informed of proposed changes in working conditions.
However, the firm's undoubted efficiency did not develop from nothing. When the distribution system was being set up the company engaged Mr. Jim Hale as depot manager, and he has a wealth of experience at BRS. Both the managing director and Jim Hale take an obvious pride in their organization because they not only talk about it, they are willing to demonstrate their methods. This is not only a theoretical system—it works!
To ensure against overloading the company has installed Hawker Siddeley Checkweights at its depots. During the nightshift vehicles not previously weighed are checked. It is this type of thinking which ensures the safe delivery of 100,000 packages on time.