Facing Millions of Brakes
Page 56
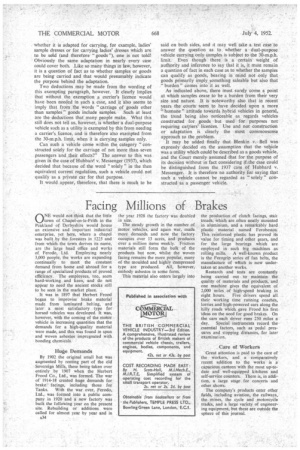
If you've noticed an error in this article please click here to report it so we can fix it.
ONE would not think that the little town of Chapel-en-le-Frith in the Peaktand of Derbyshire would house an extensive and important industrial enterprise, yet here, where a chapel was built by the foresters in 1225 and from which the town derives its name, are the large head office and works of Ferodo, Ltd. Employing nearly 3,000 people, the works are expanding continually to meet the constant demand from home and abroad for a range of specialized products of proved effieiency. The employees, too, seem hard-working and keen, and do not appear to need the ancient stocks still to be seen in the market place. .
It was in 1897 that Herbert Frond began to improvise brake material made. from laminated belting, and later a most satisfactory type for horsed -vehicles was developed. It was, however, with the coming of the motor vehicle in increasing quantities that the demands for a high-quality material were made, and this was found in spun and woven asbestos impregnated with bonding chemicals.
Huge Demands By 1902 the original small hut was augmented by renting part of the old Sovereign Mills, these being taken over entirely by 1907 when the Herbert Frood Co., Ltd., was formed. The war of 1914-18 created huge demands for brake facings, including those for Tanks. With the war over, Ferodo, Ltd., was formed into a public company in 1920 and a new factory wag built the following year on the present site. Rebuilding or additions were called for almost year by year and in
A34 the year 1928 the factory was doubled in size.
The steady growth in the number of motor vehicles, and again war, made more demands and now the factory occupies over 13 acres, and produces over a million items weekly. Friction materials still form the bulk of the products but now, whilst the woven facing remains the more popular, many of the moulded and highly compressed type are produced. All, however, embody asbestos in some form.
This material also enters largely into
the production of clutch facings, stair treads, which are often neatly mounted in aluminium, and a remarkably hard plastic material named Ferobestos. This reinforced plastic has proved its value for timing and other gears, and for the large bearings which are employed in such big machines as
rolling mills. A well-known product is the Ferogrip series Of fan belts, the manufacture of which is now undertaken at another works.
Research and tests are constantly being carried out to maintain the quality of materials and products, and one machine gives the equivalent of 2,000 miles of high-speed braking in eight hours. Five drivers spend all. their working time running coaches, lorries and high-powered cars along the hilly roads which gave Frood his first ideas on the need for good brakes. On the cars each driver runs 250 Miles a day. Special instruments record the essential factors, such as pedal pressures and slopping distances, for later examination.
Care of Workers
Great attention is paid to the care of the workers, and a comparatively recent addition to the works is a capacious canteen with the most up-todate and well-equipped kitchens and self-service counters. There is, in addition, a large stage for concerts and other shows.
The company's products enter other fields, including aviation, the railways, the mines, the cycle and motorcycle trades, and a large variety of engineering equipment, but these are outside the sphere of this journal.