To ensure against contamination, which could result in the complete
Page 74
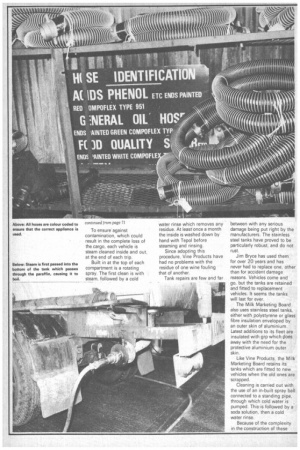
Page 75
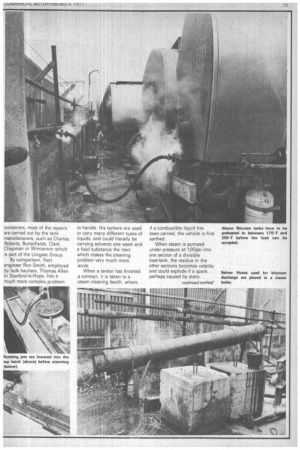
Page 76
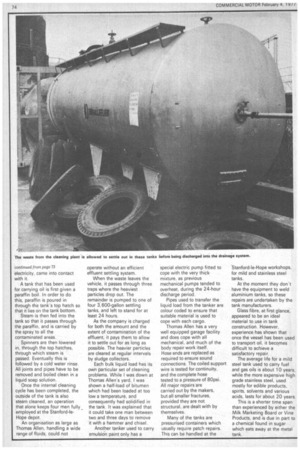
If you've noticed an error in this article please click here to report it so we can fix it.
loss of the cargo, each vehicle is steam cleaned inside and out, at the end of each trip.
Built in at the top of each compartment is a rotating spray The first clean is with steam, followed by a cold water rinse which removes any residue. At least once a month the inside is washed down by hand with Tepol before steaming and rinsing.
Since adopting this procedure, Vine Products have had no problems with the residue of one wine fouling that of another.
Tank repairs are few and far between with any serious damage being put right by the manufacturers. The stainless steel tanks have proved to be particularly robust, and do not rust.
Jim Bryce has used them for over 20 years and has never had to replace one, other than for accident damage reasons. Vehicles come and go, but the tanks are retained and fitted to replacement vehicles. It seems the tanks will last for ever.
The Milk Marketing Board also uses stainless steel tanks, either with polystyrene or glass fibre insulation enveloped by an outer skin of aluminium. Latest additions to its fleet are insulated with grp which cloes away with the need for the protective aluminium outer skin.
Like Vine Products, the Milk Marketing Board retains its tanks which are fitted to new vehicles when the old ones are -scrapped.
Cleaning is carried out with the use of an in-built spray bail connected to a standing pipe, through which cold water is pumped. This is followed by a soda solution, then a cold water rinse.
Because of the complexity in the construction of these containers, most of the repairs ' are carried out by the tank manufacturers, such as Charles Roberts, Butterfields, Clark Chapman or Wincanton which is part of the Unigate Group.
By comparison, fleet engineer Ron Smith, employed by bulk hauliers, Thomas Allen in Stanford-le-Hope, has a much more complex problem to handle. His tankers are used to carry many different types of liquids, and could literally be carrying solvents one week and a food substance the next, which makes the cleaning problem very much more acute.
When a tanker has finished a contract, it is taken to a steam cleaning booth, where, if a combustible liquid has been carried, the vehicle is first earthed.
When steam is pumped under pressure at 100psi into one section of a divisible load-tank, the residue in the other sections becomes volatile and could explode if a spark, perhaps caused by static electricity, came into contact with it.
A tank that has been used for carrying oil is first given a paraffin boil. In order to do this, paraffin is poured in through the tank's top hatch so that it lies on the tank bottom, Steam is then fed into the tank so that it passes through the paraffin, and is carried by the spray to all the contaminated areas.
Spinners are then lowered in, through the top hatches, through which steam is passed. Eventually this is followed by a cold water rinse. All joints and pipes have to be removed and boiled clean in a liquid soap solution.
Once the internal cleaning cycle has been completed, the outside of the tank is also steam cleaned, an operation that alone keeps four men fully _ employed at the Stanford-leHope depot.
An organisation as large as Thomas Allen, handling a wide range of fluids, could not operate without an efficient effluent settling system.
When the waste leaves the vehicle, it passes through three traps where the heaviest particles drop out. The remainder is pumped to one of four 3,600-gallon settling tanks, and left to stand for at least 24 hours.
As the company is charged for both the amount and the extent of contamination of the effluent, it pays them to allow it to settle out for as long as possible. The heavier particles are cleared at regular intervals by sludge collectors.
Each bulk liquid load has its own particular set of cleaning problems. While I was down at Thomas Allen's yard, I was shown a half-load of bitumen which had been loaded at too low a temperature, and consequently had solidified in the tank. It was explained that it could take one man between two and three days to remove it with a hammer and chisel.
Another tanker used to carry emulsion paint only has a special electric pump fitted to cope with the very thick mixture, as previous mechanical pumps tended to overheat, during the 24-hour discharge period.
Pipes used to transfer the liquid load from the tanker are colour coded to ensure that suitable material is used to cope with each cargo.
Thomas Allen has a very well equipped garage facility and does cope with all mechanical, and much of the body repair work itself.
Hose ends are replaced as required to ensure sound connections. The coiled support wire is tested for continuity, and the complete hose tested to a pressure of 80psi. All major repairs are carried out by the makers, but all smaller fractures, provided they are not structural, are dealt with by themselves.
Many of the tanks are pressurised containers which usually require patch repairs. This can be handled at the 'Stanford-le-Hope workshops, for mild and stainless steel tanks.
At the moment they don't have the equipment to weld aluminium tanks, so these repairs are undertaken by the tank manufacturers.
Glass fibre, at first glance, appeared to be an ideal material to use in tank construction. However, experience has shown that once the vessel has been used to transport oil, it becomes difficult to achieve a satisfactory repair.
The average life for a mild steel tank used to carry fuel and gas oils is about 10 years, while the more expensive high grade stainless steel, used mostly for edible products, spirits, solvents and various acids, lasts for about 20 years.
This is a shorter time span than experienced by either the Milk Marketing Board or Vine Products, and is due in part to a chemical found in sugar which eats away at the metal tank.