Planning ahead saves money
Page 55
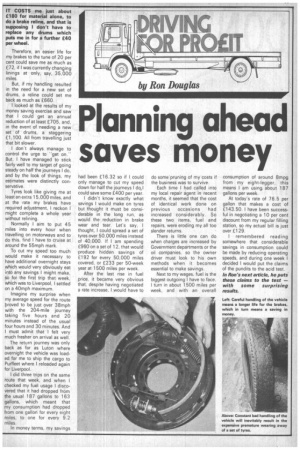
Page 57
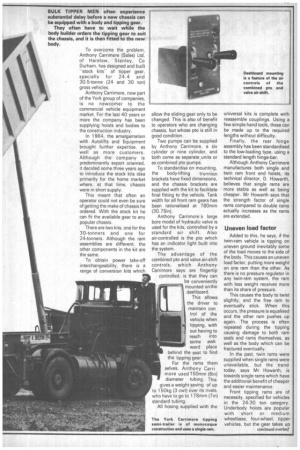
Page 58
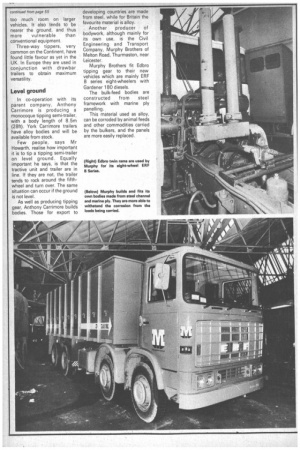
If you've noticed an error in this article please click here to report it so we can fix it.
Therefore, an easier life for my brakes to the tune of 20 per cent could save me as much as £72, if I was currently changing linings at only, say, 35,000 miles.
But, if my handling resulted in the need for a new set of drums, a reline could set me back as much as £660.
I looked at the results of my money saving exercise and saw that I could get an annual reduction of at least £705, and, in the event of needing a new set of drums, a staggering £1,100. All from travelling just that bit slower.
I don't always manage to control the urge to "get on." But, I have managed to stick fairly well to my target of going steady on half the journeys I do, and by the look of things, my estimates were distinctly conservative.
Tyres look like giving me at least an extra 15,000 miles, and at the rate my brakes have required adjustment, I reckon I might complete a whole year without relining.
Normally I aim to put 45 miles into every hour when travelling on motorways and to do this, find I have to cruise at around the 55mph mark.
To cut my speed too much would make it necessary to have additional overnight stays which would very obviously eat into any savings I might make, so for the first trip that week, which was to Liverpool, I settled on a 40mph maximum.
Imagine my surprise when my average speed for the route proved to be just over 38mph with the 204-mile journey taking five hours and 20 minutes instead of the usual four hours and 30 minutes. And I must admit that I felt very much fresher on arrival as well.
The return journey was only back as far as Luton where overnight the vehicle was loaded for me to ship the cargo to Purfleet where I reloaded again for Liverpool.
I did three trips on the same route that week, and when I checked my fuel usage I discovered that it had dropped from the usual 187 gallons to 163 gallons, which meant that my consumption had dropped from one gallon for every eight miles, to one for every 9.2 miles.
In money terms, my savings had been £16.32 so if I could only manage to cut my speed down for half the journeys I do,1 could save some £400 per year I didn't know exactly what savings I would make on tyres but thought it must be considerable in the long run, as would the reduction in brake wear and tear. Let's say, I thought, I could spread a set of tyres over 50,000 miles instead of 40,000. If I am spending £960 on a set of 12, that would produce hidden savings of £192 for every 50,000 miles covered, or £233 per 50-week year at 1500 miles per week.
After the last rise in fuel price, it became very obvious that, despite having negotiated a rate increase, I would have to do some pruning of my costs if the business was to survive.
Each time I had called into my local repair agent in recent months, it seemed that the cost of identical work done on previous occasions had increased considerably. So these two items, fuel and repairs, were eroding my all too slender returns.
There is little one can do when charges are increased by Government departments or the oil companies, so the owner driver must look to his own methods when it becomes essential to make savings.
Next to my wages, fuel is the biggest outgoing I have to face. I turn in about 1500 miles per week, and with an overall consumption of around 8mpg from my eight-legger, this means I am using, about 187 gallons per week.
At today's rate of 76.5 per gallon that makes a cost of £143.50 I have been successful in negotiating a 10 per cent discount from my regular filling station, so my actual bill is just over £129.
I remembered reading somewhere that considerable savings in consumption could be made by reducing operating speeds, and during one week I decided I would put the claims of the pundits to the acid test. In Ron's next article, he puts these claims to the test — with some surprising results.
To overcome the problem, Anthony Carrimore (Sales) Ltd, of Harelaw, Stanley, Co Durham, has designed and built "stock kits" of tipper gear, specially for 24.4 and 30.5-tonne (24 and 30 ton) gross vehicles.
Anthony Carrimore, now part of the York group of companies, is no newcomer to the commercial vehicle equipment market. For the last 40 years or more the company has been supplying hoists and bodies to the construction industry.
In 1964, the amalgamation with Autolifts and Equipment brought further expertise, as well as more customers.
Although the company is predominantly export oriented, it decided some three years ago to introduce the stock kits idea primarily for the home market where, at that time, chassis were in short supply.
This meant that often an operator could not even be sure of getting the make of chassis he ordered. With the stock kit he can fit the available gear to any popular chassis.
There are two kits, one for the 30-tonners and one for 24-tonners. Although the ram assemblies are different, the other components in the kit are the same.
To obtain power take-off interchangeability, there is a range of conversion kits which allow the sliding gear only to be changed. This is also of benefit to operators who are changing chassis, but whose pto is still in good condition.
Two pumps can be supplied by Anthony Carrimore, a six cylinder or nine cylinder, and both come as separate units or as combined pto pumps.
To standardise on mounting, the body-lifting trunnion brackets have fixed dimensions, and the chassis brackets are supplied with the kit to facilitate final fitting to the vehicle. Tank width for all front ram gears has been rationalised at 780mm (30.75in).
Anthony Carrimore's large bore model of hydraulic valve is used for the kits, controlled by a standard air shift. Also air-controlled is the pto which has an indicator light built into the system.
The advantage of the combined pto and valve air-shift controls, which Anthony Carrimore says are fingertip controlled, is that they can be conveniently mounted onthe dashboard.
This allows the driver to maintain con trol of the vehicle when tipping, with out having to reach into some awk ward place behind the seat to find the tipping gear.
For the rams them selves, Anthony Carri more used 150mm (6in) diameter tubing. This gives a weight saving of up to 150kg (3 cwt) over its rivals, who have to go to 178mm (7in) standard tubing.
All hosing supplied with the universal kits is complete with reassemble couplings. Using a few simple hand tools, these can be made up to the required lengths without difficulty.
Finally, the rear hinge assembly has been standardised to the low-loading type, using a standard length hinge-bar.
Although Anthony Carrimore manufactures both single and twin ram front end hoists, its technical director, D. Howarth, believes that single rams are more stable as well as being cheaper. Mr Howarth says that the strength factor of single rams compared to double rams actually increases as the rams are extended.
Uneven load factor
Added to this, he says, if the twin-ram vehicle is tipping on uneven ground inevitably some of the load moves to the side of the body. This causes an uneven load factor, putting more weight on one ram than the other. As there is no pressure regulator in any twin-ram system, the ram with less weight receives more than its share of pressure.
This causes the body to twist slightly, and the free ram to eventually stick. When this occurs, the pressure is equalised and the other ram pushes up again. The process is often repeated during the tipping causing damage to both ram seals and rams themselves, as well as the body which can be fractured eventually.
In the past, twin rams were supplied when single rams were unavailable, but the trend today, says Mr Howarth, is towards single rams which have the additional benefit of cheaper and easier maintenance.
Front tipping rams are of necessity, specified for vehicles in the 24-30 ton category. Underbody hoists are popular with short or medium wheelbase, four-wheel, tipper vehicles, but the gear takes up too much room on larger vehicles. It also tends to be nearer the ground, and thus more vulnerable than conventional equipment.
Three-way tippers, very common on the Continent, have found little favour as yet in the UK. In Europe they are used in conjunction with drawbar trailers to obtain maximum versatility.
Level ground
In co-operation with its parent company, Anthony Carrimore is producing a monocoque tipping semi-trailer, with a body length of 8.5m (28ft). York Carrimore trailers have alloy bodies and will be available from stock.
Few people, says Mr Howarth, realise how important it is to tip a tipping semi-trailer on level ground. Equally important he says, is that the tractive unit and trailer are in line. If they are not, the trailer tends to rock around the fifthwheel and turn over. The same situation can occur if the ground is not level.
As well as producing tipping gear, Anthony Carrimore builds bodies. Those for export to developing countries are made from steel, while for Britain the favourite material is alloy.
Another producer of bodywork, although mainly for its own use, is the Civil Engineering and Transport Company, Murphy Brothers of Melton Road, Thu rmaston, near Leicester, Murphy Brothers fit Edbro tipping gear to their new vehicles which are mainly ERF B series eight-wheelers with Gardener 180 diesels.
The bulk-feed bodies are constructed from steel framework with marine ply panelling.
This material used as alloy, can be corroded by animal feeds and other commodities carried by the bulkers, and the panels are more easily replaced,