DEMOUNTABLE DISTRIBUTION 12
Page 86
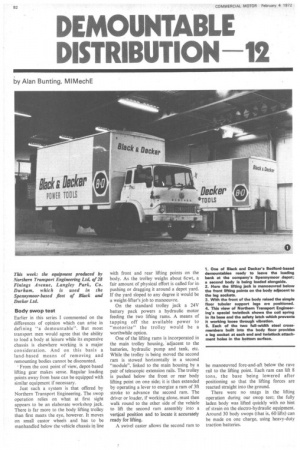
Page 87
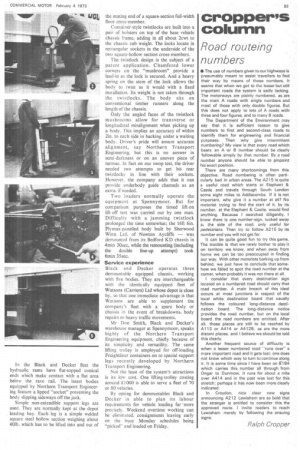
If you've noticed an error in this article please click here to report it so we can fix it.
by Alan Bunting, MIMechE
Body swop test Earlier in this series I commented on the differences of opinion which can arise in defining "a derriountable". But most transport men would agree that the ability to load a body at leisure while its expensive chassis is elsewhere working is a major consideration. And on this basis a land-based means of removing and remounting bodies cannot be discounted.
From the cost point of view, depot-based lifting gear makes sense. Regular loading points away from base can be equipped with similar equipment if necessary.
Just such a system is that offered by Northern Transport Engineering. The swop operation relies on what at first sight appears to be an elaborate workshop jack. There is far more to the body lifting trolley than first meets the eye, however. It moves on small castor wheels and has to be manhandled below the vehicle chassis in line
with front and rear lifting points on the body. As the trolley weighs about 6cwt, a fair amount of physical effort is called for inpushing or dragging it around a depot yard. If the yard sloped to any degree it would be a weight-lifter's job to manoeuvre.
On the standard trolley jack a 24V battery pack powers a hydraulic motor feeding the two lifting rams. A means of tapping off the available power to "motorize" the trolley would be a worthwhile option.
One of the lifting rams is incorporated in the main trolley housing, adjacent to the batteries, hydraulic pump and tank, etc. While the trolley is being moved the second ram is stowed horizontally in a second "module", linked to the main housing by a pair of telescopic extension rails. The trolley is pushed below the front or rear body lifting point on one side; it is then extended by operating a lever to energize a ram of 3f1 stroke to advance the second ram. The driver or loader, if working alone, must then walk round to the other side of the vehicle to lift the second ram assembly into a vertical position and to locate it accurately ready for lifting.
A swivel caster allows the second ram to be manoeuvred fore-and-aft below the rave rail to the lifting point. Each ram can lift 8 tons, the base being lowered after positioning so that the lifting forces are reacted straight into the ground.
There were no snags in the lifting operation during our swop test; the fully laden body was lifted quickly with no hint of strain on the electro-hydraulic equipment. Around 30 body swops (that is, 60 lifts) can be made on one charge, using heavy-duty traction batteries.
In the Black and Decker fleet the hydraulic rams have flat-topped conical ends which make contact with a flat area below the rave rail. The latest bodies equipped by Northern Transport Engineering feature a lipped "socket" preventing the bod.■, slipping sideways off the jack.
Simple non-extendible support legs are used. They are normally kept at the depot loading bay. Each leg is a simple welded square steel hollow section weighing about 401b, which has to be lifted into and out of the mating end of a square-section full-width floor cross-member.
Container-style twistlocks are built into a pair of bolsters on top of the base vehicle chassis frame, adding in all about 2cwt to the chassis cab weight. The locks locate in rectangular sockets in the underside of the two square-hollow-section cross-members.
The twistlock design is the subject of a patent application. Chamfered lower corners on the "mushroom" provide a lead-in as the lock is secured. And a heavy spring on the stem of the lock allows the body to twist as it would with a fixed installation. Its weight is not taken through the twistlocks. The body sits on conventional timber runners along the length of the chassis.
Only the angled faces of the twistlock mushrooms allow for transverse or longitudinal misalignment when picking up a body. This implies an accuracy of within 2in. to each side in backing under a waiting body. Driver's pride will ensure accurate alignment, say Northern Transport Engineering, but this is no answer in semi .darkness or on an uneven piece of tarmac. In fact on our swop test, the driver needed two attempts to get his rear twistlocks in line with their sockets. However, the company adds that it can provide underbody guide channels as an extra, if needed.
Two loaders normally operate the equipment at Spennymoor. But for comparison purposes the timed lift-on lift-off test was carried out by one man. Difficulty with a jamming twistlock prolonged the time somewhat; the 16ft 6in. Plymax-panelled body built by Sherwood Winn Ltd. of Newton Aycliffe — was demounted from its Bedford KD chassis in 4min 30sec, while the remounting (including the double line-up attempt) took 6min 35sec.
Service experience Black and Decker operates three demountable equipped chassis, working with five bodies. They are interchangeable with the identically equipped fleet of Watsons (Carriers) Ltd whose depot is close by, so that one immediate advantage is that Watsons are able to supplement the company's fleet with a spare body or chassis in the event of breakdowns, body repairs or heavy traffic movements.
Mr Don Smith, Black and Decker's warehouse manager at Spennymoor, speaks highly of the Northern Transport Engineering equipment, chiefly because of its simplicity and versatility. The same lifting trolley is employed for off-loading Freightliner containers on to special support legs recently developed by . Northern Transport Engineering.
Not the least of the system's attractions is its low cost. One lifting-trolley costing around £1000 is able to serve a fleet of 70 or 80 vehicles.
By opting for demountables Black and Decker is able to plan its labour requirements for vehicle loading far more precisely. Weekend overtime working can be eliminated, consignments leaving early on the busy Monday schedules being "picked" and loaded on Friday.